I . i – Generac Power Systems 53187 User Manual
Page 113
Attention! The text in this document has been recognized automatically. To view the original document, you can use the "Original mode".
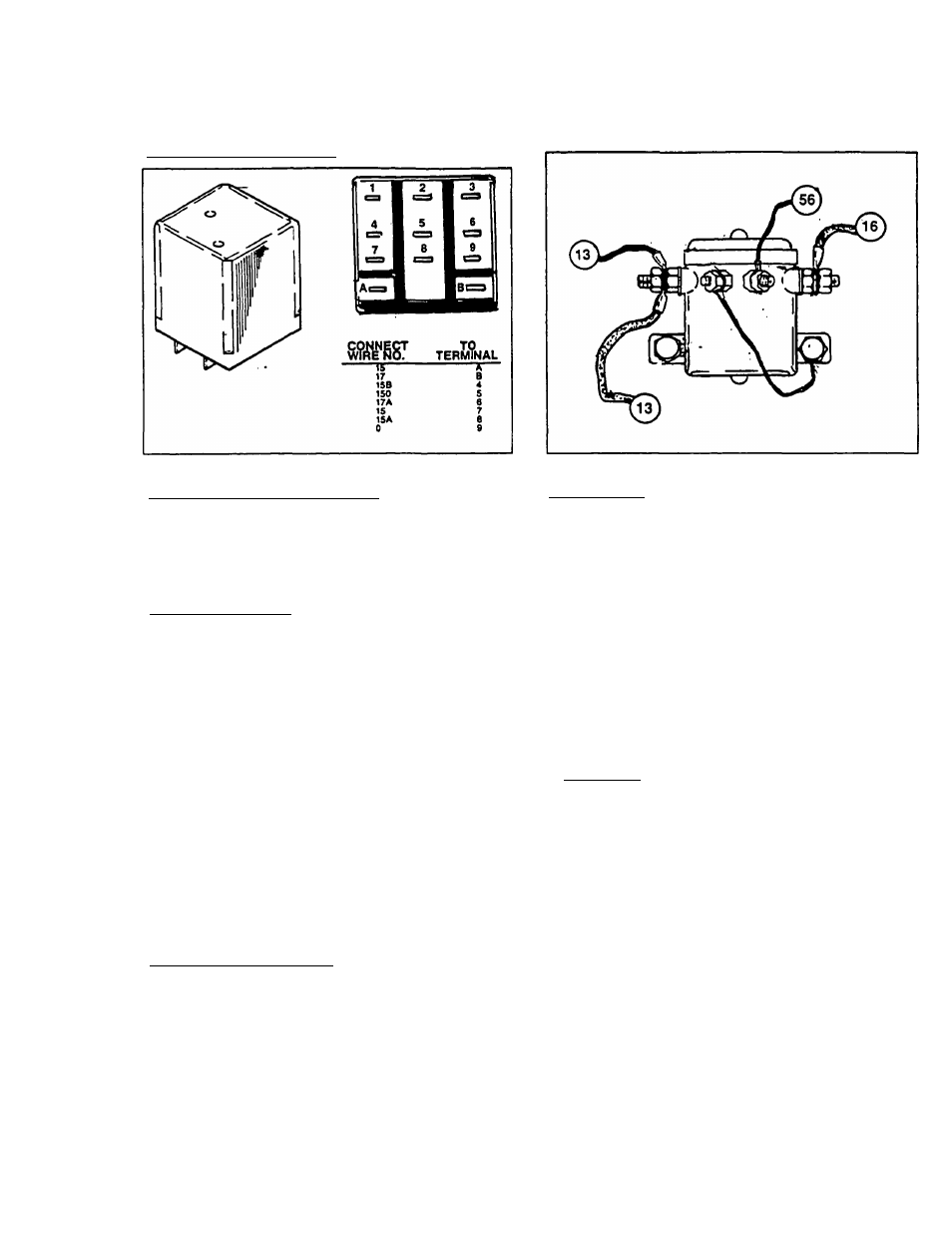
PARTS
ENGINE ELECTRICAL SYSTEM
1
SECTION 5.2
ENGINE CRANKING SYSTEM
Type 1 Engine Cranking System (Continued)
CRANK RELAY CR1 (CONT’D):
Figure 4. Crank Relay (CR1)
ENGINE CONTROL CIRCUIT BOARD;
See "Engine Control Circuit Board" in Section 5.1
(Page 5.1-1). Type 1 systems utilized an early produc
tion circuit board which required an externally mounted
crank relay (CR1) and run relay (CR2) for starting and
running operations.
START/STOP SWITCH;
When set to "Start", the switch connects Wire 17 to
frame ground. This energizes the crank relay (CR1)
and initiates engine cranking.
When set to "Stop", the switch connects a Wire 18
circuit to ground and initiates engine shutdown.
Schem atic
18 17
i . i
STOP
START
Pictorial
PTTn
START STOP
am
AVA' >rr Sr C VA
Figure 5. The Start/Stop Switch
STARTER CONTACTOR (SC);
When energized by battery voltage from the engine
control circuit board (Wire 56), the starter contactor’s
normally-open contacts close to deliver full batteiy
power to the starter motor. The engine is then cranked.
The automotive type starter contactor is equipped with
heavy duty contacts able to withstand high current.
Figure 6. Starter Contactor (SC)
THE STARTER;
General: The Type 1 and 2 engine starter assem
bly is shown in Figure 7 on next page. The motor is
rated 12 volts DC. Never exceed this rated voltage or
magnets in the starter may become demagnetized.
Starter
Performance
Test:
Starter
performance
can be tested using a fully charged 12 volts battery.
Use a No. 10 (or larger) cable that is not more than 6
feet long. Connect the battery positive (+) post to the
starter motor input stud; connect the battery negative
(-) terminal to the starter motor housing. Maximum
current draw and starter speed should be as follows:
CAUTION:
DO
NOT
operate the
starter
motor
continuously for longer than about 30 seconds
when testing._____________________________________
Inspection: Check for excessive wear on all bear
ings, gears, shafts, etc. Check the spring washer for
wear. Convex side of the spring washer should be next
to the bearing. Add a drop of oil to the face of the
bearing.
Thru-Bolts: Tighten thru-bolts to 75 inch-pounds
of torque.
Drive Cap: Apply a film of SAE 10 oil to the
bearings in the drive cap. During reassembly, the insu
lating washer must be placed against the drive cap.
Armature:
Check
the
armature
for
an
open,
shorted or grounded condition using a growler. Hold the
armature in a vise when Installing or removing the drive
assembly. Apply a thin film of special non-conducting
grease to the commutator end of the armature shaft and
to the portions of the shaft that contact the bearings.
PAGE 5.2-3