0 maintenance procedures (cont’d) – Reznor PDH Operation Manual PreevA User Manual
Page 24
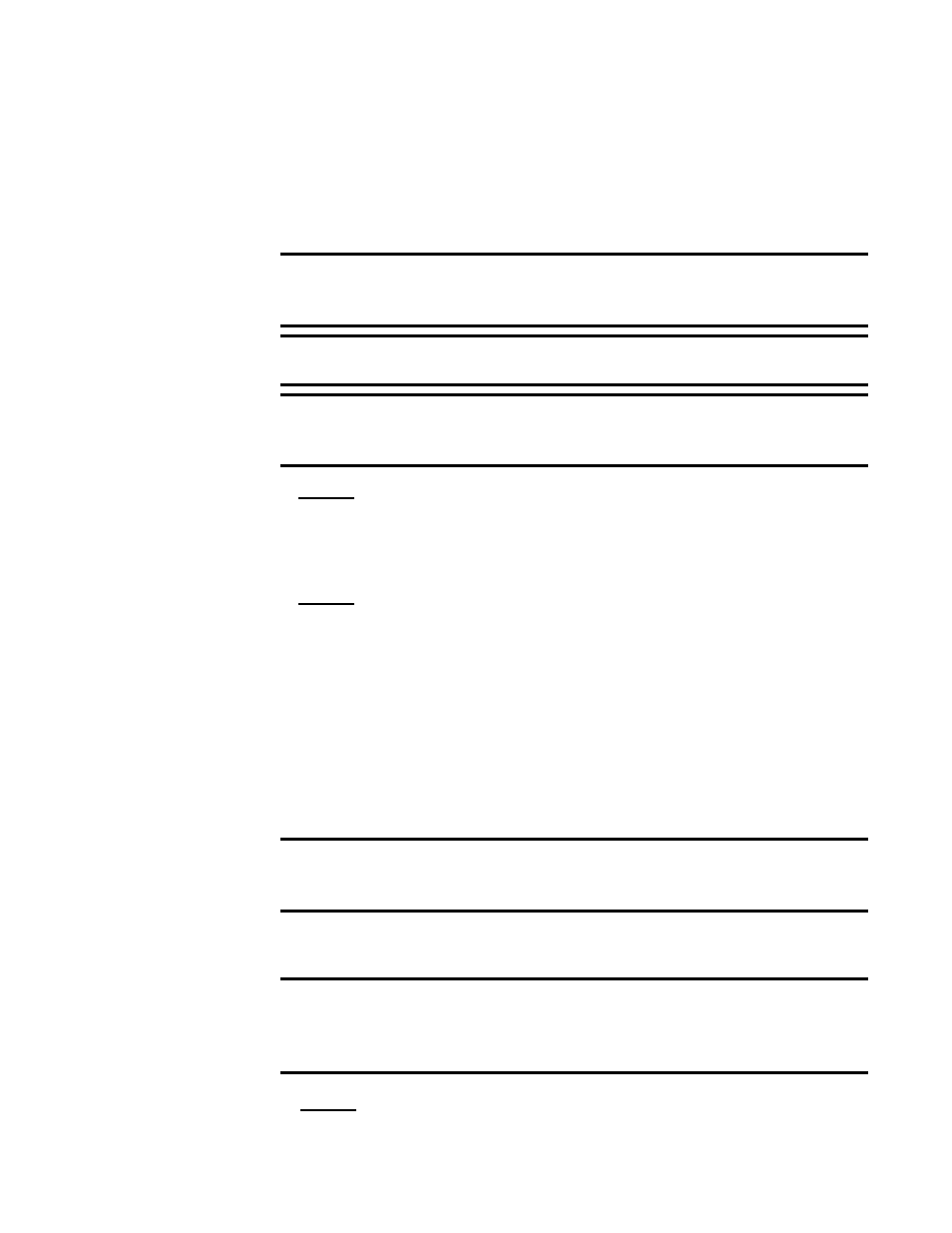
Form O-PreevA, Page 24
3.7 Optional
Cooling Coil
Module (cont’d)
Reheat Module Compressor Maintenance and Replacement (cont’d)
3.7.4 Optional Reheat
Module (cont’d)
Brazing materials must be able to withstand the high pressure of R410A refriger-
ant. A high temperature, silver phosphate type brazing with 5% or greater alloy is
recommended.
To prevent oxidation, purge tubing with 2-3 psig of regulated dry nitrogen while it is
being brazed. After the unit has been properly leak tested, the nitrogen remaining in
the circuit can be used as part of the purge while brazing. Open the service valve as
needed to release the nitrogen. Do not allow moisture to enter the system.
The installer is responsible for brazing and for complying with appropriate standard
refrigerant piping procedures.
CAUTION: All brazing should be done using a 2 to 3 psig dry
nitrogen purge flowing through the pipe being brazed. See Hazard
Levels, page 2.
CAUTION: Do not open the service valves until after the condenser
unit circuits are leak tested. See Hazard Levels, page 2.
CAUTION: When brazing, protect all painted surfaces and compo-
nents from excessive heat. Wet wrap all valves but do not allow
moisture to enter the tubing. See Hazard Levels, page 2.
□
Step 6. Check Reheat Refrigerant Circuit for Leaks
After installation is complete, pressurize the system with helium or dry nitrogen to
approximately 150 psi (maximum pressure is 450 psi). Check for leaks using soap
bubbles or other leak-detecting methods. Repair as needed to ensure a leak free
circuit.
□
Step 7. Evacuate the Reheat Circuit
Use a vacuum pump and micron gauge. The circuit must be evacuated to hold a
500 micron vacuum. Vacuum must be pulled on both the discharge (high) and suc-
tions (low) side. Do the suction side first; and the compressor discharge side sec-
ond. To establish that a circuit is leak-free and moisture-free, a standing vacuum
test is recommended. Close off the valve to the vacuum pump and observe the
micron gauge. If the vacuum gauge does not rise above 500 microns in one min-
ute, the evacuation should be complete. If the vacuum gauge does rise above 500
microns in one minute, evacuation is incomplete or the system has a leak. Repeat
as needed until evacuation is complete.
NOTE Evacuation will not remove moisture from POE oil. Moisture must be pre-
vented from getting in the oil.
Continue and/or repeat
Steps 6 and 7 until evacuation is complete.
CAUTION: Do not use the replacement compressor as an
evacuation assist and never apply voltage to a compressor while
it is in a vacuum. See Hazard Levels, page 2.
Moisture and air are harmful to the system because they increase the condensing
temperature, raise the discharge gas temperature, cause formation of acids, and
cause oil breakdown.
CAUTION: Do not leave a circuit open to the atmosphere any longer
than minimum required for installation. POE oil in the compressor
is extremely susceptible to moisture absorption. Evacuation will
not remove moisture from POE oil. See Hazard Levels, page 2.
3.0 Maintenance
Procedures
(cont’d)
□
Step 8. Check the Electrical System
After the system has been evacuated, reconnect the electrical plug to the com-
pressor or the wires to the compressor terminals. It is a normal practice to replace
all starting components any time a compressor is changed.