General idm system wiring, Hybrid cable – Rockwell Automation MDF-SB1304F Kinetix 6000M Integrated Drive-Motor System User Manual
Page 56
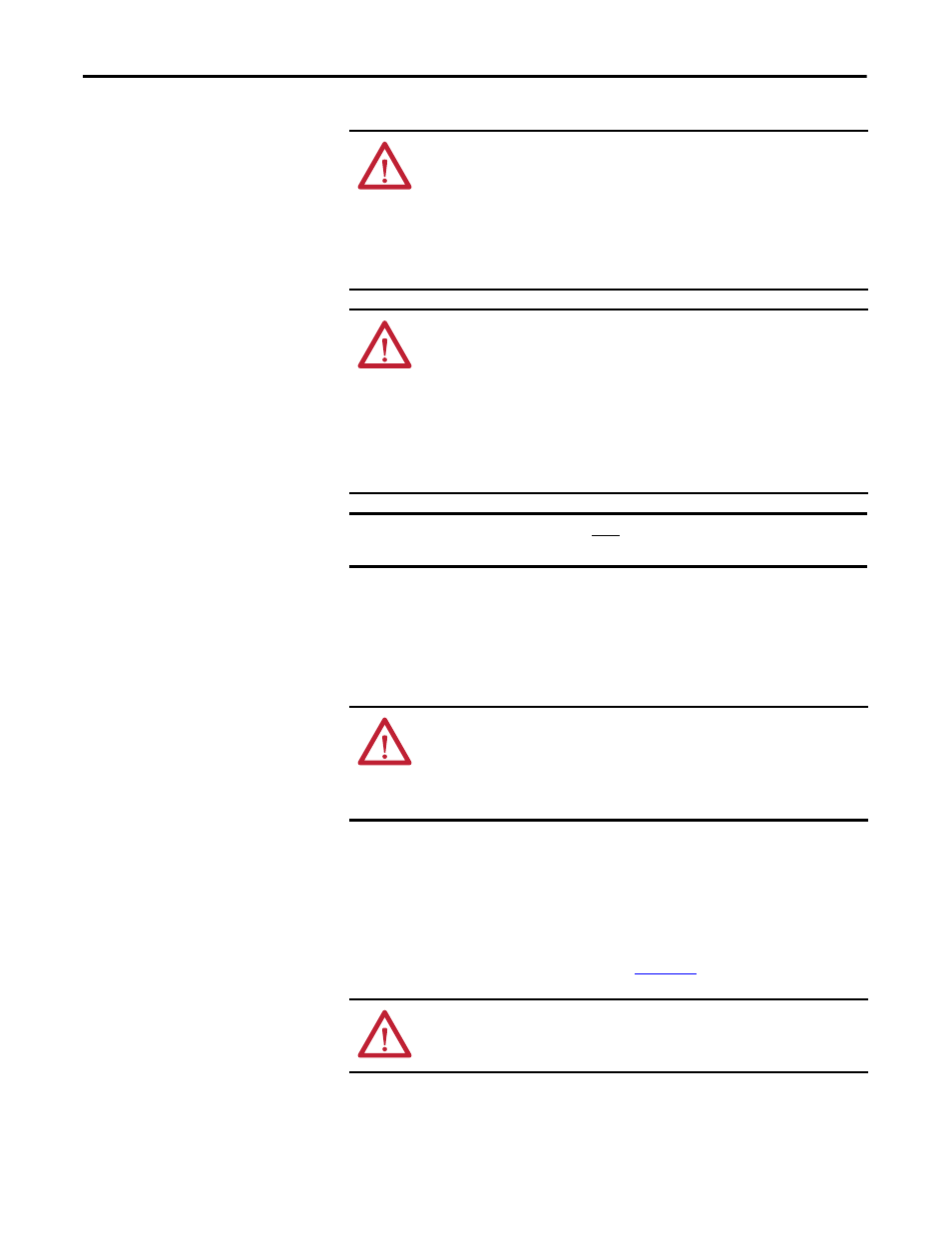
56
Rockwell Automation Publication 2094-UM003A-EN-P - May 2012
Chapter 5
Connecting the Kinetix 6000M System
General IDM System Wiring
Always form a drip loop in the cables directly before each cable enters and exits
the IDM unit. A drip loop is a low spot in the cable that lets liquids gather and
drip off the cable rather than flow along the cable to an electrical connection or
the motor.
Connect the network and hybrid cables only after the IDM unit is mounted.
Hybrid Cable
A hybrid cable, catalog number 2090-CHBIFS8-12AAxx, transfers DC bus
power and inter-module communication signals from the IPIM module to the
first IDM unit. Additional IDM units are daisy chained by using a
2090-CHBP8S8-12AAxx cable as shown in
ATTENTION: Arcing or unexpected motion can occur if cables are connected or
disconnected while power is applied to the IDM system. Before working on the
system, disconnect power and wait the full time interval indicated on the IPIM
module warning label or verify the DC bus voltage at the IPIM module measures
less than 50V DC.
Failure to observe this precaution could result in severe bodily injury or loss of life,
and damage to the product will occur.
ATTENTION: Be sure that installed cables are restrained to prevent uneven
tension or flexing at the cable connectors. Provide support at 3 m (10 ft)
intervals throughout the cable run.
Excessive and uneven lateral force at the cable connectors may result in the
connector’s environmental seal opening and closing as the cable flexes, or wires
separating at the cable gland.
Failure to observe these safety procedures could result in damage to the motor and
its components.
IMPORTANT
Building your own cables is not an option for the hybrid and network cables
used in the IDM system.
ATTENTION: Cable connectors must be properly aligned before the connection
is secured with the recommended degrees of turn or torque value. Improper
connector alignment is indicated by the need for excessive force, such as the use
of tools, to fully seat connectors. Failure to observe these safety procedures
could result in damage to the IDM unit, cables, and connector components.
ATTENTION: Verify that all connections are correct when wiring the connector
plugs and that the plugs are fully engaged in the module connectors. Incorrect
wiring/polarity or loose wiring can cause explosion or damage to equipment.