Rockwell Automation 1761-NET-ENIW MicroLogix Ethernet Interface (ENI) User Manual User Manual
Page 100
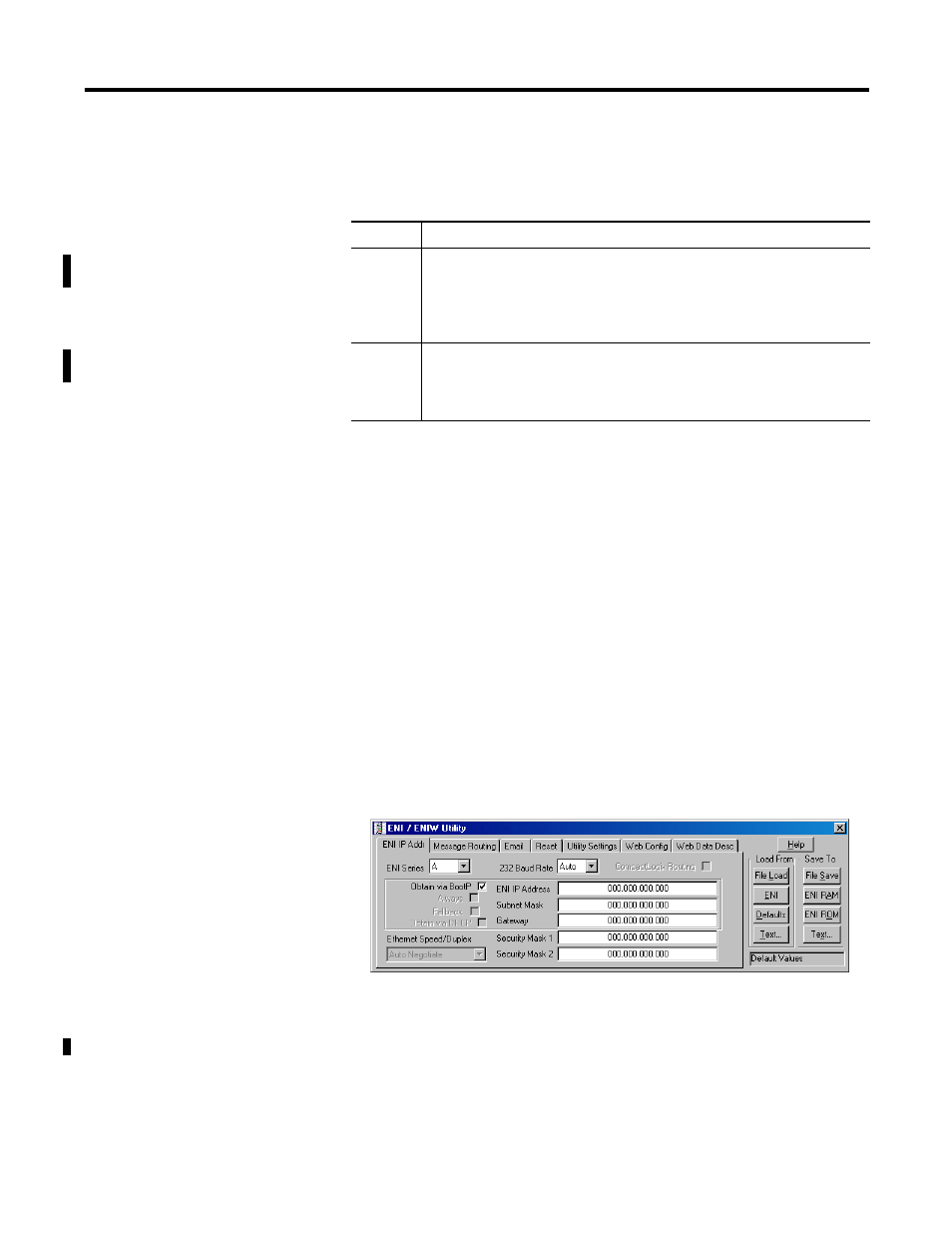
Publication 1761-UM006E-EN-P - August 2005
8-8 Connecting CompactLogix Controllers on Ethernet
be linked to DF1 destination node addresses, for the following
purposes:
At this point we need to configure ENI #2 as we did ENI #1, using the
ENI/ENIW Configuration Utility.
You could also use the method outlined in Chapter 5 to configure ENI
#2. This method sends configuration Messages from the CompactLogix
controller via the DF1 link. If for any reason this ENI/ENIW would
need to be replaced, it could then be easily and quickly configured
via messages from the CompactLogix controller. A ladder program to
accomplish this is shown on page 8-10.
Configure ENI #2 Via the ENI/ENIW Configuration Utility
When you start the ENI/ENIW Configuration Utility, the following
screen appears:
Figure 8.7 ENI/ENIW Configuration Utility ENI IP Addr Screen
For this example, we use 38400 baud on all serial connections. The
“232 Baud Rate” field on the “ENI IP Addr tab” must be left at “Auto”
for the series B/C/D ENI/ENIW to detect that a CompactLogix
controller is attached to it, and that it should use bridged mode,
allowing RSLogix 5000 to upload/download/go online with the
CompactLogix from Ethernet. We also assign IP addresses to all
Ethernet products rather than using BOOTP.
Table 8.2 Message Routing
Nodes
Function
0 to 44
Use when sending messages to any Ethernet device, other than Logix
controllers with integral Ethernet ports, that supports the same command set
as the CompactLogix controller, i.e. SLC 5/05, PLC-5E and other ENI/ENIW
modules. We will use the PLC-5 Typed Write commands for this example. CIP
commands are not supported by the ENI/ENIW.
45 to 49
Use when sending messages to Logix controllers with integral Ethernet ports.
When sending to a ControlLogix Controller via a 1756-ENBT, the controller
MUST be in slot 0 of the ControlLogix chassis for the message to be delivered
to it.