Communications – Rockwell Automation 1395 ControlNet Communication Board User Manual
Page 17
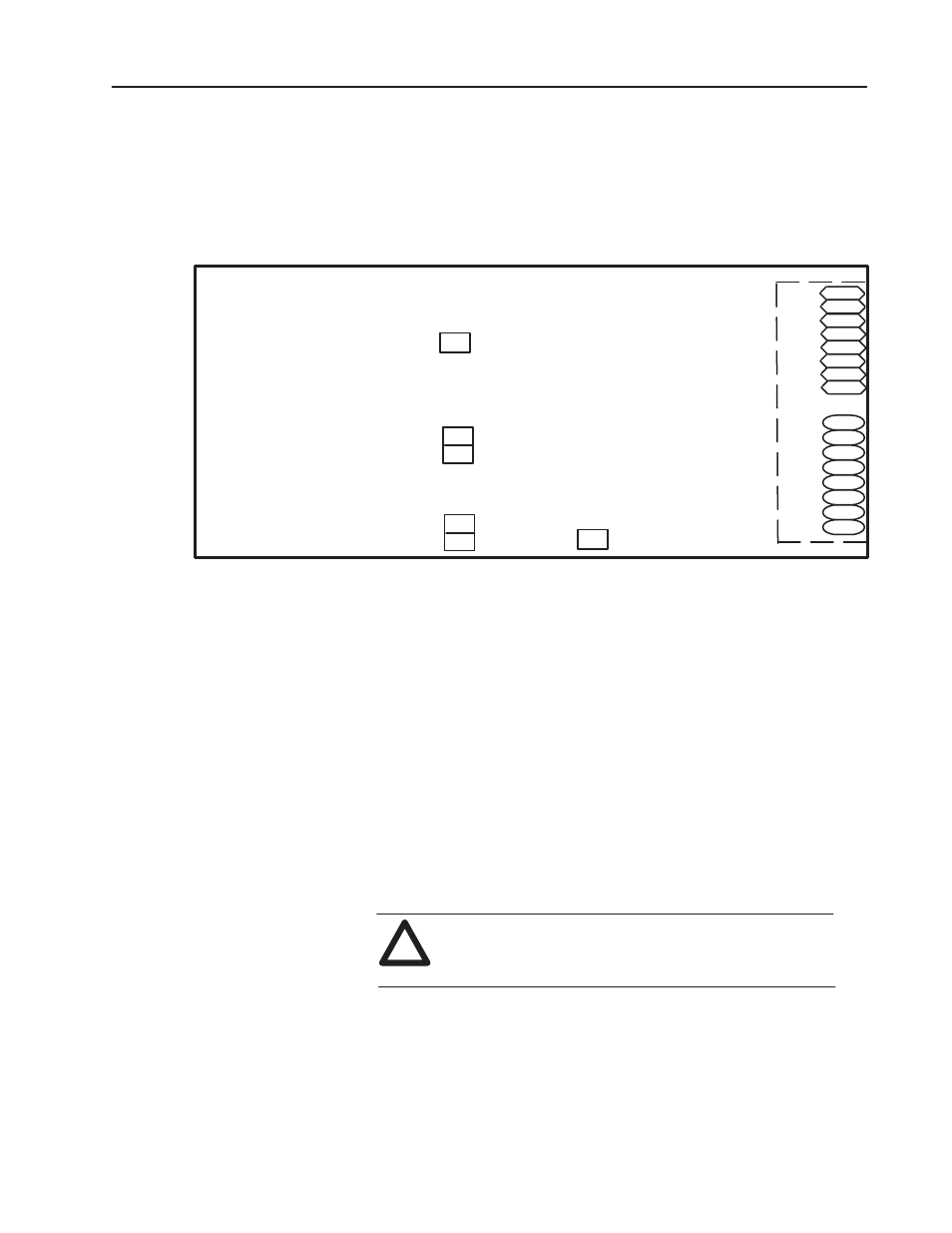
3–3
Configuration & PLC Interfacing
Publication 1395–5.37– March, 1999
Figure 3.1 presents an overview of the CNA board with a typical
Channel configuration. The parameter numbers shown are for a CNA
board mounted in Port B of the Drive. This is the standard Port for the
CNA Board.
Figure 3.1. CNA Board Channel Configuration for Port B
300
301
302
303
304
305
306
Comm Channel
350
351
352
353
354
355
356
Firmware
Version #
549
500
501
502
503
Fault/Warning
Configuration
Parameters
307
357
Fault/Warning
Status
Parameters
504
DIP Switch
for CNet
Node Address
Communications
When you use the ControlNet Adapter Board for ControlNet
communications, the drive looks like a remote I/O chassis to a PLC.
This allows you to use discrete data transfer.
With discrete data transfer, the PLC controller’s I/O image table is used
to transfer the data that the drive needs to have continuously updated
ControlNet has the option for redundancy. Redundancy for the entire
network is determined by the configuration tool (RS Networx
TM
).
Below is a listing of the CNA features on this Adapter:
S The board can be configured as a full I/O rack only.
S The board can be configured to ignore PLC fault conditions and
continue Drive operation.
!
ATTENTION: Configuring the board to ignore PLC
fault conditions could lead to erratic operation and
possible Drive or equipment damage.
S The messaging mechanism can support transfer of multiple Drive
parameters (up to 5) in a single request.
S A “redundant” feature allows the Drive to be connected to a
redundant network