3 wiring system bus (can), Wiring system bus (can), Installation – Lenze EMF2178IB User Manual
Page 25
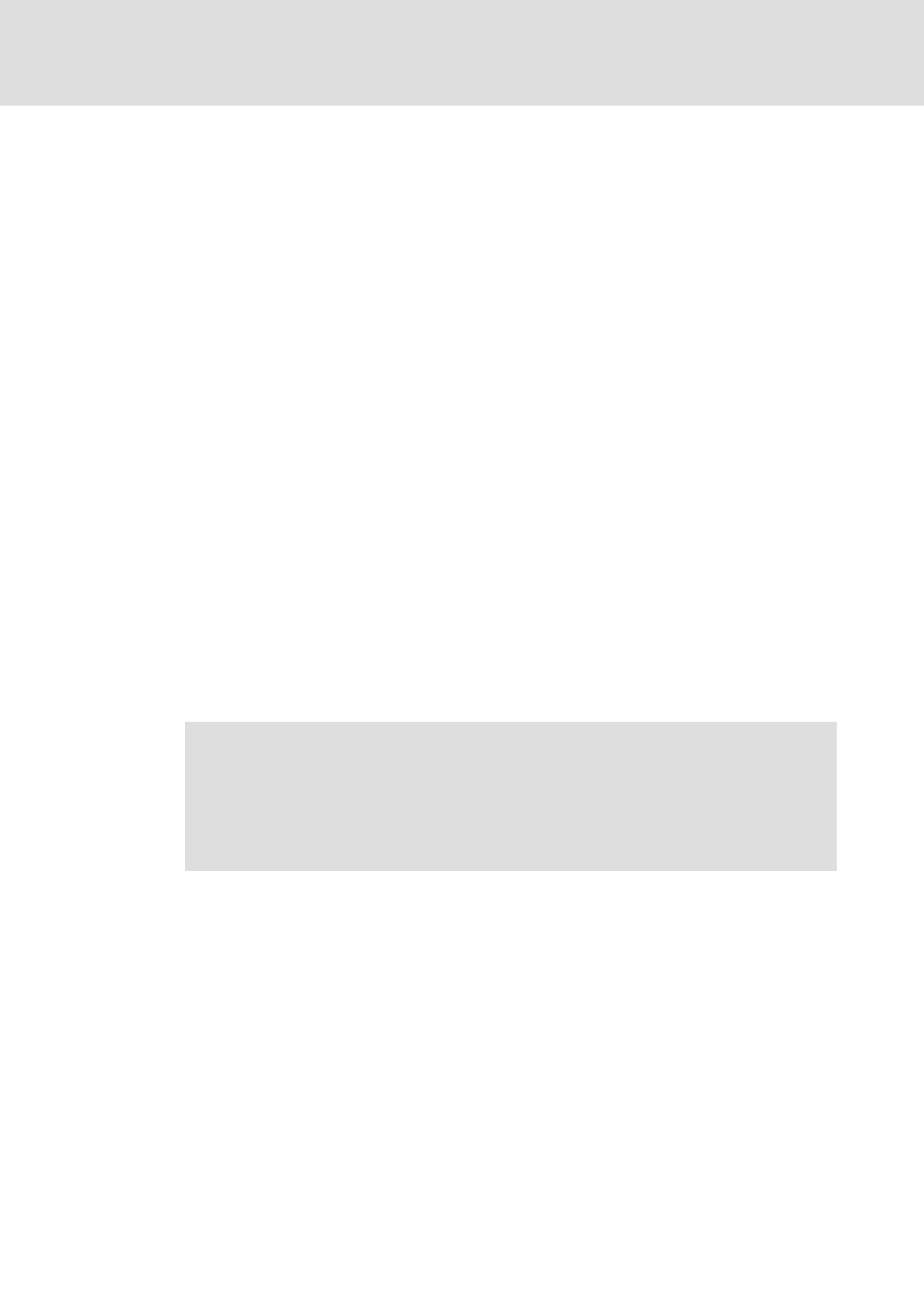
Installation
Electrical installation
Wiring system bus (CAN)
l
25
EDSMF2178IB EN 3.0
5.2.3
Wiring system bus (CAN)
Structure of a CAN bus system (example)
The CAN bus system is designed as a 2 conductor (twisted pair) shielded with additional
mass and termination at both ends of the line.
For sending and receiving data the following paths are available:
ƒ
Max. three process data channels (PDO = Process Data Object)
– Process data are sent via the process data channel and are used for high−speed and
high−priority control tasks. Typical process data are, for instance, control words,
status words, setpoints and actual values of a standard device.
ƒ
Two parameter data channels (SDO = Service Data Object)
– The parameters are transferred at lower priority than the process data and are set
or changed e.g. during commissioning or product change.
– The parameters are accessed via the parameter data channels of the EMF2178IB
communication module to the codes of the basic Lenze device or the
corresponding CANopen objects.
– With both parameter data channels, two masters can be connected to a standard
device. A PC (e.g. with the Lenze software "Global Drive Control") or an operator
terminal serve to change parameters directly at the standard device during
operation of a system connected to PLC. The second parameter data channel can
be reached under the set address (via DIP switch or C0009) with an offset of "64".
If, e.g., a PLC addresses the standard device with the address "1" and a second
commanding device the address "65", always the same standard device is
addressed.
– The second parameter channel is deactivated in the default state.
)
Note!
ƒ
The last telegram determines the parameter when a parameter is accessed
by two units (see CANopen objects 1200 and 1201 "Server SDO
Parameters".(
¶ 107)).
ƒ
Please observe the notes in the chapter 6Commissioning (
not select the baud rate and address via the front DIP switches.