KROHNE IFC 110 Converter User Manual
Page 88
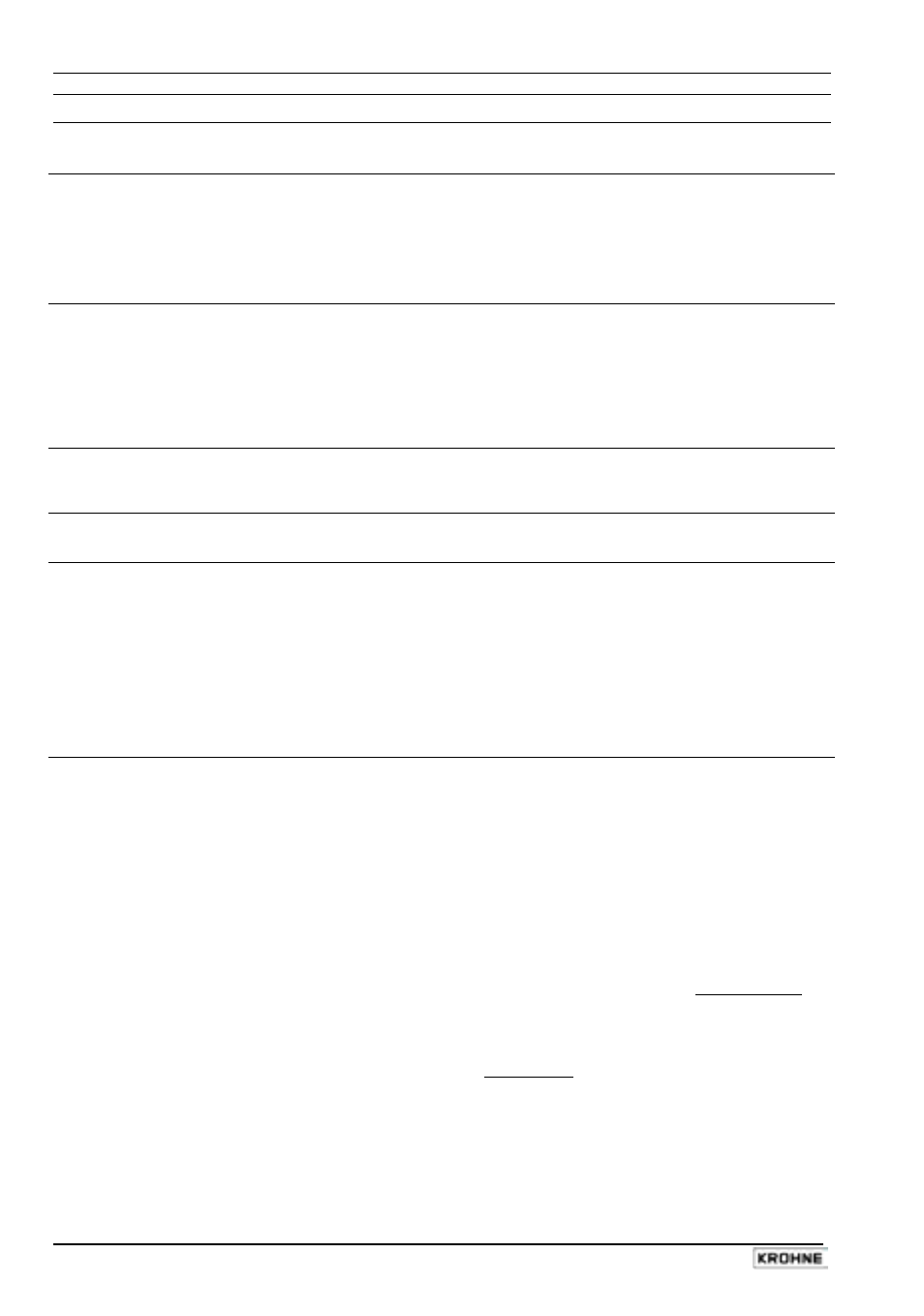
Sect. 10.1
Part D Technical Data, Measuring Principle and Block Diagram
88
IFC 110 F
05/2003
10 Technical
data
10.1 Signal
converter
Mode of operation and system structure
Measurement principle
Faraday’s law of induction
Modularity Measuring
system consisting of
signal converter and flow sensor
Measured variable
Volumetric flowrate
(electrode voltage from flow sensor)
Electrical conductivity of product
≥ 5 µS/cm
≥ 20 µS/cm for demineralized cold water
Versions
IFC 110 F / D (standard)
Display version, with local display / control elements (15 keys)
IFC 110 F / D / MP (option)
same as display version, additionally with magnetic sensors (MP) to control
the signal converter using bar magnet without opening the housing
IFC 110 F / D / MP / _ EEx (option)
ATEX-EEx version for hazardous areas, PTB 02 ATEX 2163 X
Interfaces
– HART
®
– RS 485 / PROFIBUS
}
add-on module
Add-on equipment
– CONFIG software and adapter for operator control via MS-DOS-PC,
connection to internal IMoCom interface (equipment bus)
Full-scale range
Flowrate for Q = 100%
6 Liter/h to 86 860 m³/h or 0.03 to 401 080 US Gal/min,
corresponding to flow velocity v = 0.3 – 12 m/s or v = 1 to 40 ft/s
Units
m³/h, liter/s, US Gal/min or user-defined unit, e. g. liter/day or US Gal/day
Input / output circuits
Nominal voltages
≤ 25 V AC / ≤ 50 V DC (safety value Um = 253 V)
Active / passive/ mode
connection to protective extra-low voltage (PELV)
Current output
Function
– all operating data configurable
– galvanically isolated from all input and output circuits
Current:
fixed ranges
0 – 20 mA and 4 – 20 mA
variable ranges
for Q = 0%
I
0%
= 0 – 16 mA
for Q = 100%
I
100%
= 4 – 20 mA
}
adjustable in 1mA increments
for Q > 100%
I
> 20 – 22 mA (maximum)
Load
– active operation
min. 15
Ω
– passive operation
22 V DC
≤ U ≤ 32 V DC: R
L
≤ 800 Ω
15 V DC
≤ U ≤ 22 V DC: R
L
≤ 500 Ω
Error identification
0 / 22 mA and variable
Forward/reverse flow measurement
direction identified via status output
Pulse outputs (passive)
P A1 (can also be operated as status output)
Function
– for electronic totalizers
– for electromechanical totalizers
– all operating data settable
– all operating data configurable
Terminals
P / P
A1 / A
⊥
Pulse rate
0 – 10 000 pulses per
0 – 50 pulses per
s [= Hz], min, h, m³, liter, etc.,
s [= Hz], min, h, m³, liter, etc.,
any scaling
any scaling
Electrical data
galvanically isolated
galvanically isolated, but not from A2
U
≤ 32 V DC / ≤ 24 V AC
U
≤ 32 V DC / ≤ 24 V AC
I
≤ 30 mA, any polarity
I
≤ 100 mA, any polarity
or U
≤ 32 V DC, I ≤ 200 mA
note
polarity
Pulse width
automatic: pulse duty cycle 1:1, max. 10 000 pulses/s = 10 kHz
1
variable: 10 ms – 1 s, P
100%
[pulses/s] = f
max
[Hz] =
2 x pulse width
digital pulse division, interpulse period non-uniform, therefore if frequency
and cycle meters connected allow for minimum counting interval:
1000
gate time, totalizer
≥
P
100%
[Hz]
Forward/reverse flow measurement
direction identified via status output