KROHNE CORIMASS G-MFM 4085 EN User Manual
Page 8
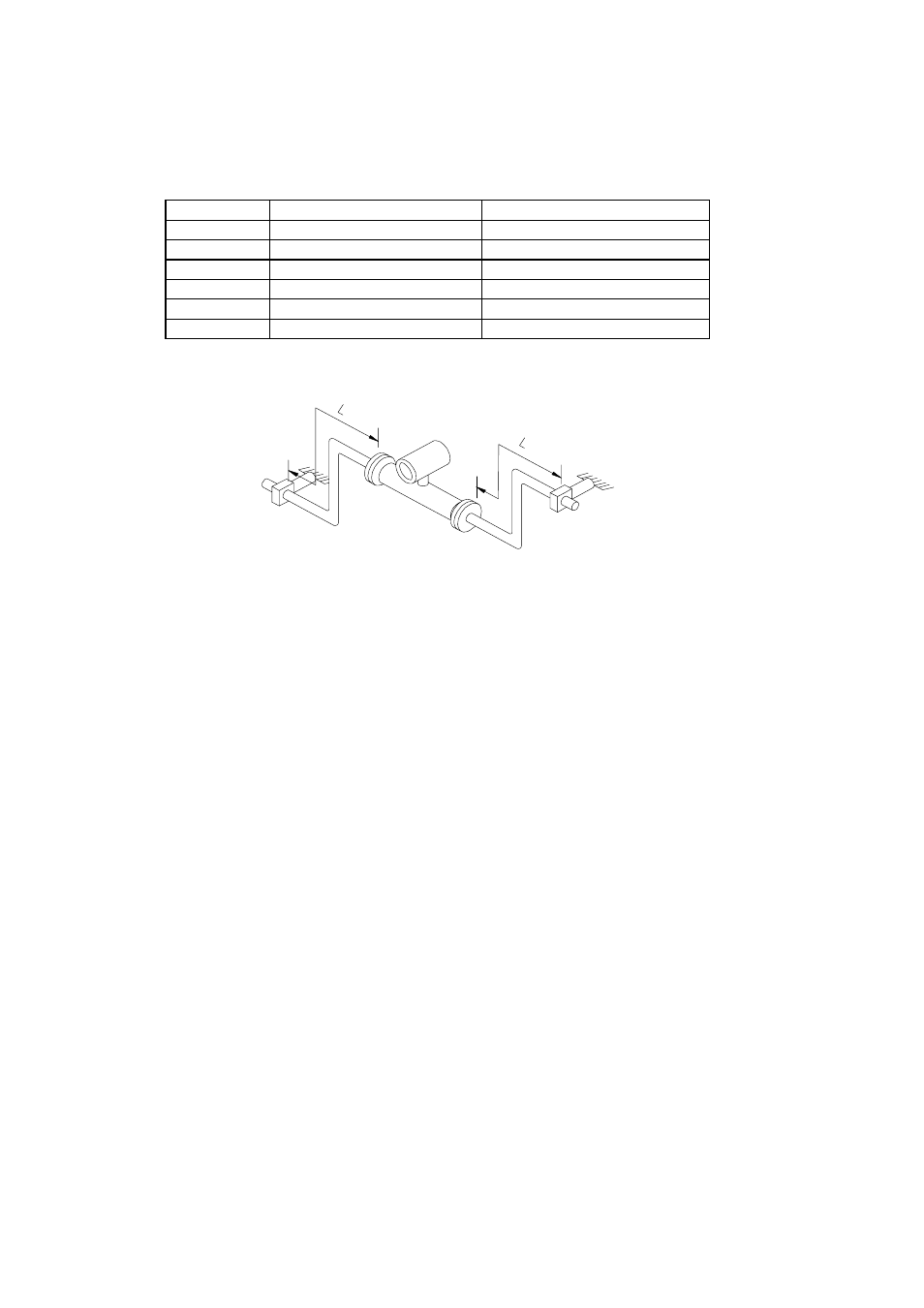
8
¾
Should it become necessary to support the pipework, the following guidelines should be
followed. Do not clamp the meter body or the process pipework closer than distance L, as
shown in the table below. Due to the weight of the 800 to 3000 G, the pipework should be
supported. Please note minimum support distances as per table.
Meter Size
L (cm)
L (inch)
10 G+
21
8,8
100 G+
35
13,8
300 G+
48
18,9
800 G+
48
18,9
1500 G+
48 (DN 50) 70 (DN 80)
18,9 (2”N.B.) 27,6 (3”N.B.)
3000 G+
48 (DN 80) 60 (DN 100)
18,9 (2”N.B.) 23,7 (3”N.B.)
¾
Connecting pipes may have bends between the meter and supports
Figure 9
¾
Fit valves, sensors, sight glasses, etc. outside the supports if possible.
1.2.3 Mounting fixtures
¾
The connecting pipework must be in a stress free condition.
¾
The meter should fit between the connecting pipe with perhaps 2 - 3 mm (
1
/
8
inch) to spare.
It should not be necessary to force the pipes apart to fit meter. Flanges should be correctly
aligned.
¾
Tighten flange bolts evenly.
¾
Do not fit rigid electrical conduit to the converter housing.
¾
Do not fit supports or any fixtures to any part of the meter or connecting pipework between
meter and supports.
1.2.4 Installation factor
The installation factor feature is unique to the G-Series. This factor (found in menu 2.7.4) is a
dimensionless number between 0 and 999 which is an indication of how well the instrument is
installed and whether the product contained gas bubbles. This is a function of the amount of
energy required to excite the measuring tube to its natural resonant frequency. The auto zero
value (menu 1.1.1 or 3.1.1) should be as low as possible, typically less than 1% for normal
installations and less than 2% for extreme conditions.