Errors, System errors, Alarm silencing – Watlow Series 96 User Manual
Page 29: Open loop detect
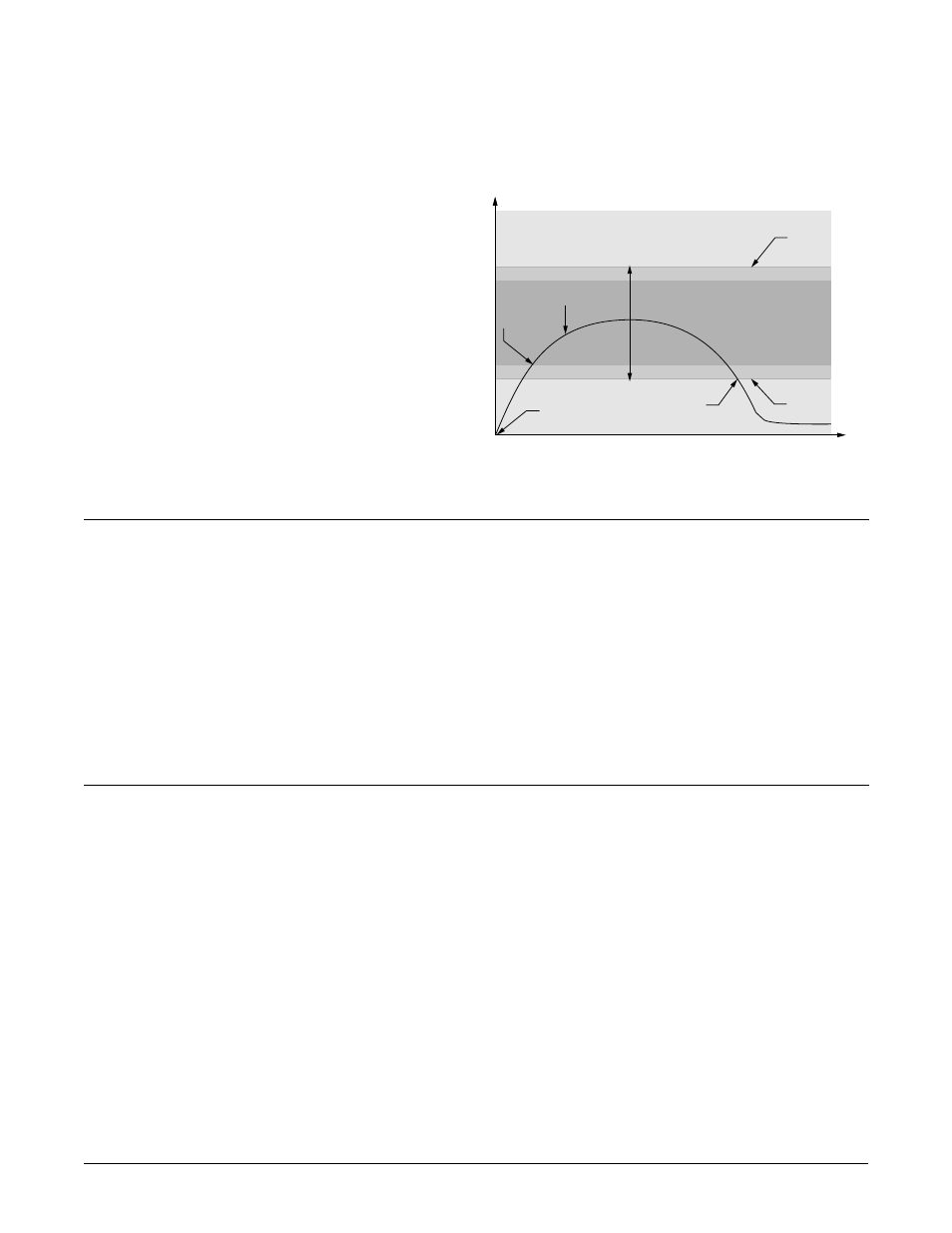
System Errors
(error number in top display, error message in bottom display)
Modbus Register #209 r; (values in parenthesis below).
Refer to appendix, page A.2, in back of manual for troubleshooting tips about error codes.
Wa t l o w S e r i e s 9 6
F e a t u r e s
■
5 . 1 0
Alarm Silencing
Modbus Register #722 r/w; values: No (0), Yes (1).
Alarm silencing has two uses:
1. It is often used to allow a system to warm up
after it has been started up. With alarm silencing
on, an alarm is not triggered when the process tem-
perature is initially lower that the alarm low set
point. The process temperature has to enter the nor-
mal operating range beyond the hysteresis zone to
activate the alarm function.
2. Alarm silencing also allows the operator to dis-
able the alarm output while the controller is in an
alarm state. The process temperature has to enter
the normal operating range beyond the hysteresis
zone to activate the alarm output function.
If a Series 96 output is functioning as a deviation
alarm, the alarm is silenced when the set point is
changed, until the process value re-enters the nor-
mal operating range. Alarm Silencing 2 [SIL2]
(Output 2 Menu) allows you to view or change
whether alarm silencing is on.
If Alarm Annunciation 2 [Anu2] (Output 2 Menu) is
set to [`YES], the Output 2 indicator light will
remain on and an alarm message will appear in the
display, even though the alarm output is silenced.
Figure 5.10 – Alarm silencing.
Normal Operating Range
Alarm
enabled
here
Alarm
triggered
here
Startup,
Alarm
disabled
Time
Tempera
ture
Alarm High
Set Point
Alarm Low
Set Point
Process
Temperature
Hysteresis
Hysteresis
Errors
Open Loop Detect
Modbus Register #210 r; values: Clear (0), Error (1).
Open loop detect can alert the user of trouble on the
input or output side of the control loop. It only works
when the controller is operating with PID control.
An open loop error is triggered when 100 percent
power is applied at the control output for a period of
time equal to the setting of integral (or the inverse
of the reset value) without the input registering a 5°
(°F or °C) change.
The open loop detect feature can be turned on or off
with Open Loop Detect [OPLP] (Global Menu).
If an open loop error occurs, the controller outputs
will shut off and [OPLP] will flash in the upper dis-
play of the controller. Shut down the system, check
the input and control output wiring and check the
input and output devices.
[Er`4] (4) Error 4 indicates there is a RAM
[raM]
malfunction.
[Er`5] (5) Error 5 indicates nonvolatile memory
[eecs]
checksum error.
[Er`6] (6) Error 6 indicates a ROM malfunction.
[rom]
[Er`7] (7) Error 7 indicates a hardware failure.
[hard]
[Er`8] (8) Error 8 indicates a module error.
[plug]
[Er`9] (9) Error 9 indicates a configuration error.
[cnfg]
[Er10] (10) Error 10 indicates a module has been
[chng]
changed.
[Er11] (11) Error 11 indicates new software has
[soft]
been installed.
[er12] (12) Error 12 indicates that calibration data
[Cal`]
is corrupted.
[er13] (13) Error 13 indicates an analog-to-digital
[Atod]
timeout.
[Er14] (14) Error 14 indicates a serial EEPROM
[EEhd
] time-out.
[Er15] (15) Error 15 indicates a new unit.
[new]
[er16] (16) Error 16 indicates an EEPROM invalid
[Addr]
address.
Errors continued on next page.