Troubleshooting guide (cont.) – Ransburg Evolver 303 Dual Purge Solvent Robotic Applicator A12374-XXX User Manual
Page 57
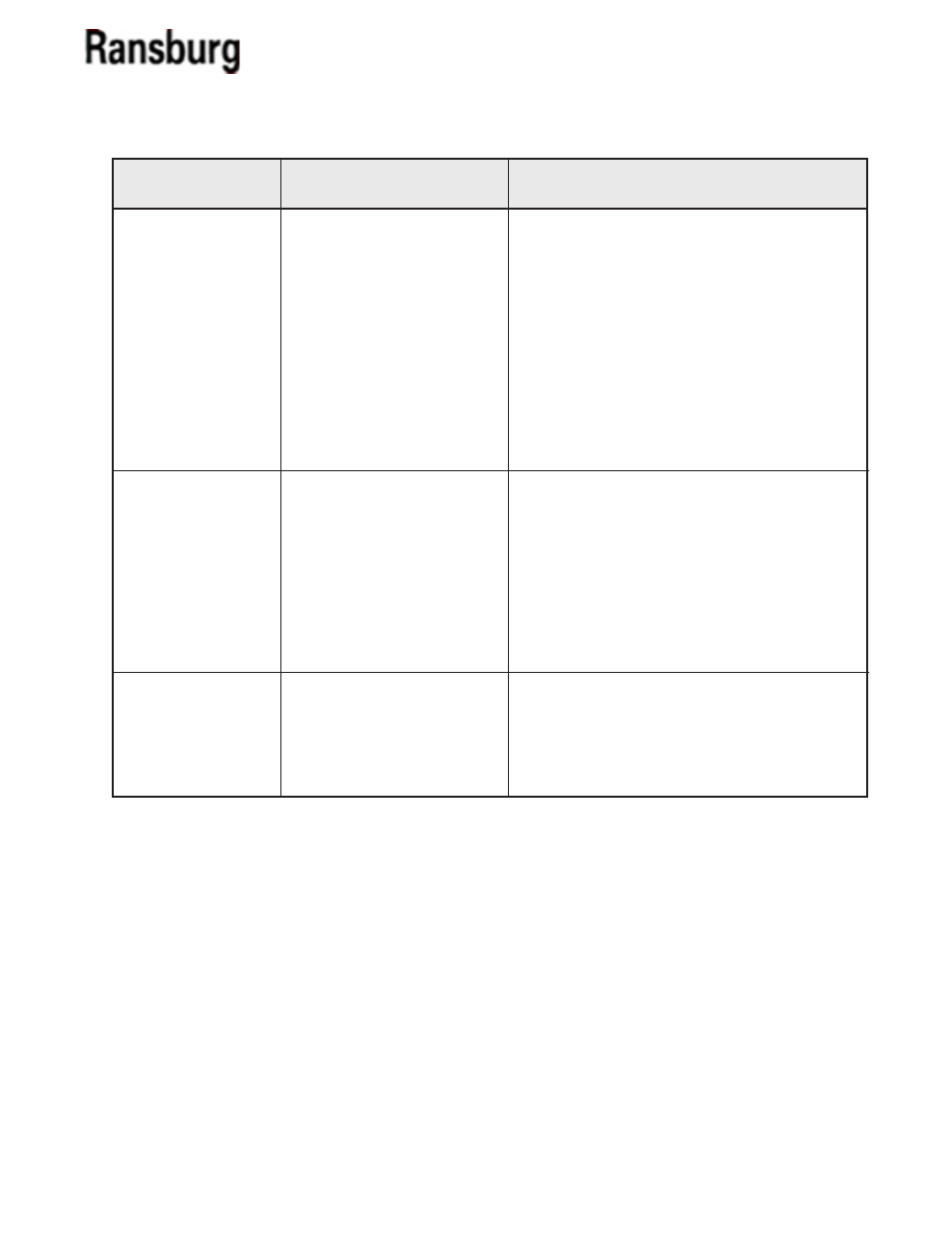
52
Evolver 303 Dual Purge Robotic Atomizers - Maintenance
TROUBLESHOOTING GUIDE (Cont.)
Note: To check for fluid leaks, it is easiest to first remove the applicator from the test station and remove the
shroud from the applicator. Then the applicator can be remounted to the test station. Leak detector may be
used at all appropriate sources. Be certain to wipe off all residual solution using a non-conductive solvent
such as Naphtha.
General Problem
Possible Causes
Corrective Action
5. Faulty low voltage connec-
tions (usually indicated by
MicroPak feedback fault
light)
6. Faulty high voltage connec-
tion
7. MicroPak or cascade failure
8. Improper color change (i.e.
paint or solvent in dump
line)
1. Low or no high voltage
2. Poor grounding of parts be-
ing coated
3. Excessive target distance
1. Applicator mounting nut is
loose
2. O-ring is missing
3. O-ring is damaged
5. a. Make sure quick disconnection electrical
connection is aligned and clean.
b.Check low voltage connection at cascade.
6. Remove cascade and check continuity between
cascade connection and turbine shaft.
7. Refer to "MicroPak" service manual for detailed
"Troubleshooting Guide".
8. Optimize color change.
1. Verify high voltage at bell cup edge. Normally,
a high voltage setting of 70 -100 kV is appropri-
ate for most applications.
2. Verify that parts being coated are properly
grounded (the electrical resistance between the
part and ground must not exceed 1 megohm).
3. The recommended target distance is between
10-14-inches (.25m-.36m) (see "Target Dis-
tance" in the "Operation" section of this
manual).
1. Tighten mounting ring.
2. Install o-ring.
3. Visually inspect for damage and replace.
Low or No High
Voltage (Cont.)
Low Transfer
Efficiency (or light
coverage)
Fluid and/or Air
Leakage Between the
Robot and Rear
Manifold Plates
AA-08-01.1