Maintenance, Routine maintenance schedule – Ransburg Evolver 303 Dual Purge Solvent Robotic Applicator A12374-XXX User Manual
Page 34
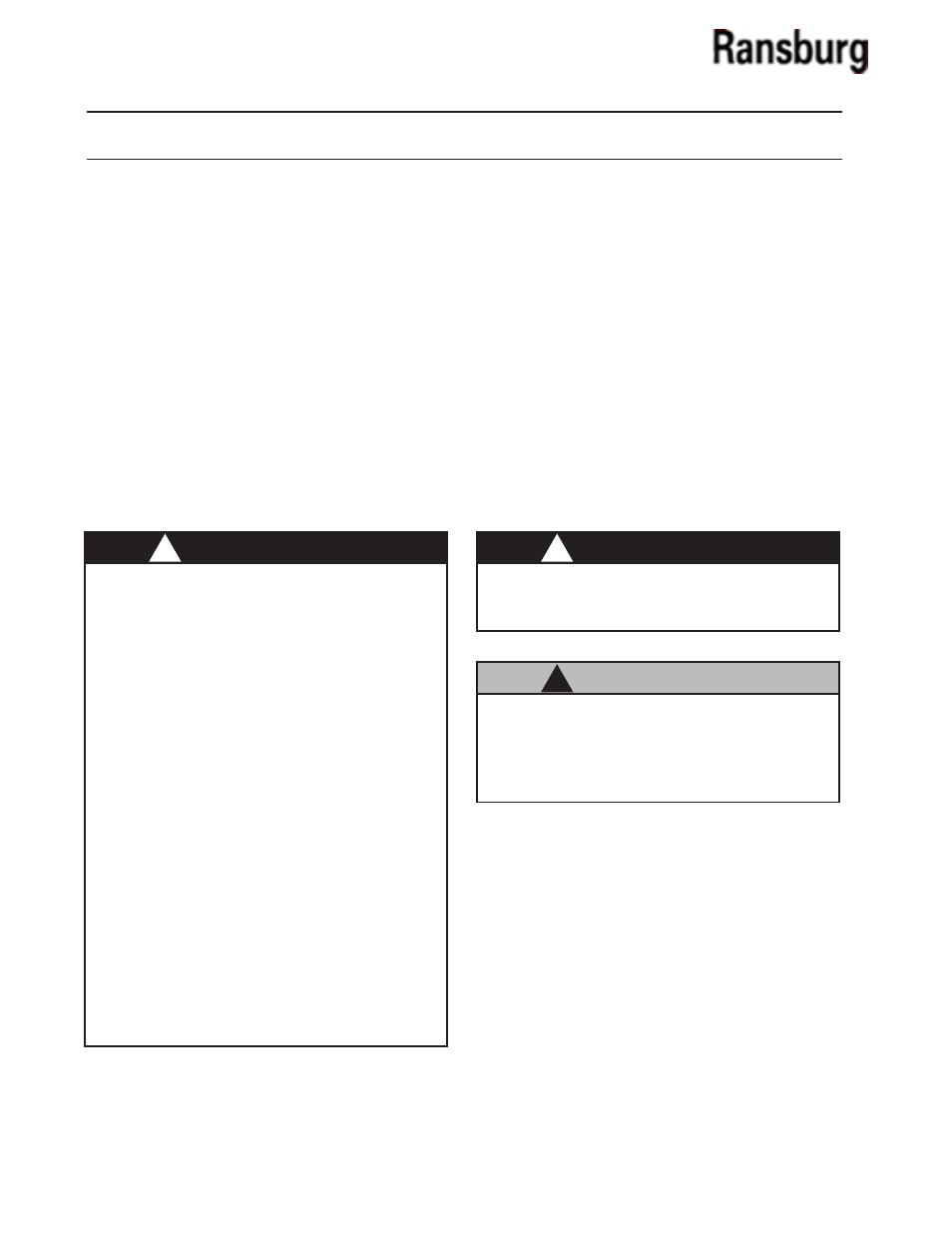
29
Evolver 303 Dual Purge Robotic Atomizers - Maintenance
MAINTENANCE
Good maintenance is essential to safe and productive
operation. Schedules should be established by the
user, based on the following general information and
observations of the initial production requirements.
The Ransburg maintenance and safety information
should be made available to each operator.
Normal fire protection measures are necessary, includ-
ing proper storage of paints and solvents and the
proper disposal of waste. Ready access to appropriate
fire extinguishing equipment is required. For details,
consult the appropriate NFPA safety information
and/or applicable country safety standard.
ROUTINE MAINTENANCE
SCHEDULE
Follow these maintenance steps to extend the life of
the spray applicator and ensure efficient operation:
Several Times Daily
1. Turn the MicroPak control unit OFF! Follow
"Lockout/Tagout Procedures".
2. Inspect the fluid nozzle, air cap, and elec-trode
wire for paint accumulation. Clean as frequently as
necessary. See "Procedures" in the "Maintenance"
section.
>
Do not bend the applicator electrode while
wiping. Never immerse the applicator in sol-
vents. This will cause damage to the electrical
components.
C A U T I O N
!
>
Take precautions to see that skin is not
punctured by sharp electrode.
W A R N I N G
!
>
An electrical discharge or spark may create an
electrical and/or fire hazard during maintenance.
Do not clean or service the spray applicator with
the power supply on. Verify that the power supply
has been locked out and tagged out per OSHA
and/or your applicable country safety codes.
>
Unexpected robot movement can be hazard-
ous. Do not adjust or repair the spray applicator
when the robot is operating or waiting to start.
The robot must be locked out and tagged out
per OSHA and/or your applicable country safety
codes.
>
Solvents used for equipment flushing must
have flash point ratings equal to or greater than
the flash point rating of the coating material.
Solvents used for general cleaning must have
flash point ratings higher than 100
°
F (37.8
°
C).
>
Never remove spray applicator head from
assembly while under pressure.
W A R N I N G
!
Daily (Or at Shift Start)
1. Turn the MicroPak control unit OFF and:
• Check within 20-ft. (6.1 meters) of the point of
operation (of the applicator) and remove or
ground ALL loose or ungrounded containers.
• Inspect workholders for accumulated coating
materials (remove such accumulations if
present). Ensure resistance to ground from
work holder is less than 1 megohm.
• Check that the nozzle assembly is clean and
undamaged. Ensure air caps are clean and
undamaged.
AA-08-01.1