Applicator and manifold assembly – Ransburg Evolver 303 Dual Purge Solvent Robotic Applicator A12374-XXX User Manual
Page 21
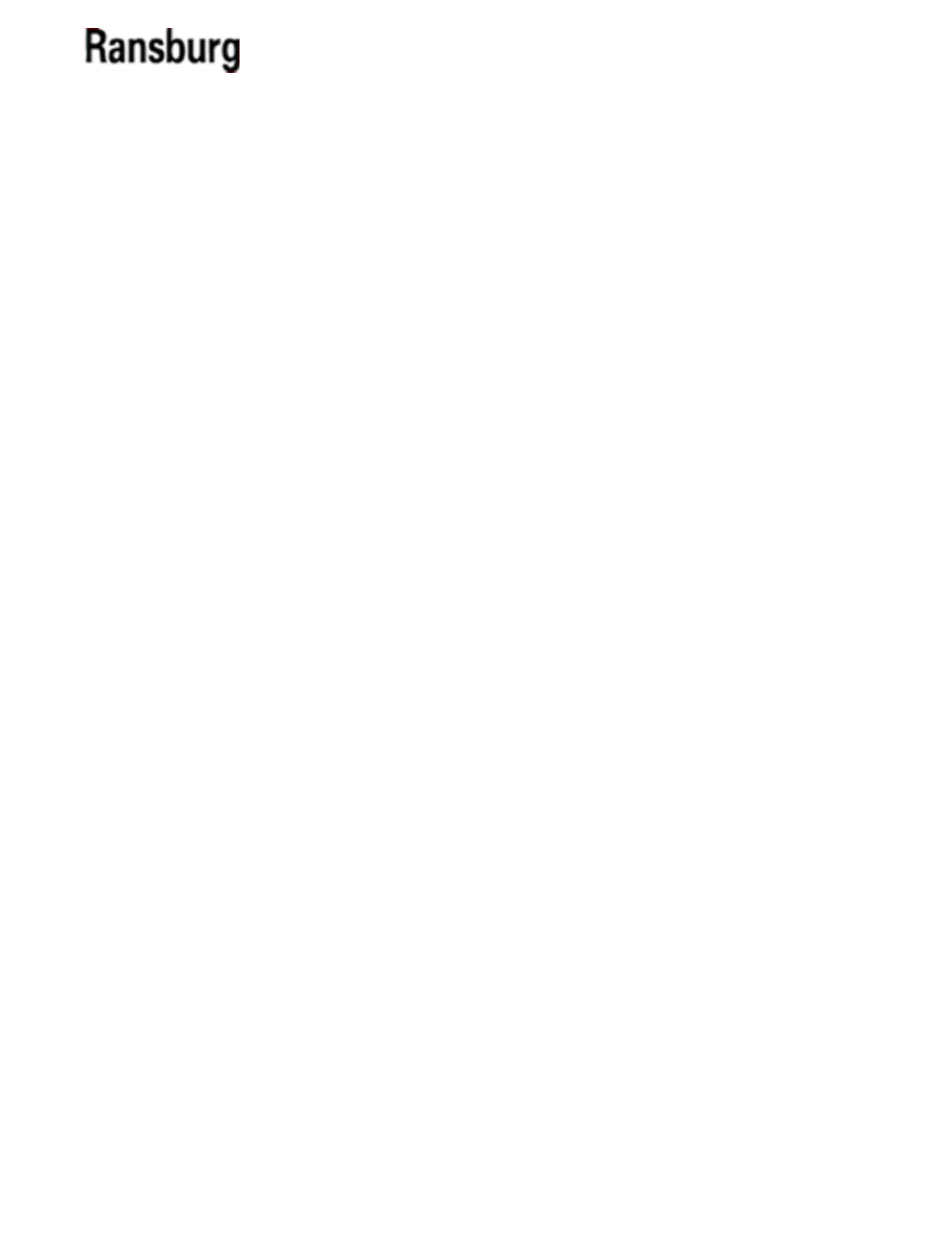
16
Evolver 303 Dual Purge Robotic Atomizers - Installation
APPLICATOR AND MANIFOLD
ASSEMBLY
(See Figures 4 and 5)
The tubing, hose, and low voltage cable come
bundled from the factory. Pull the bundle through
the robot spacer plate and robot wrist carefully to
prevent any cuts on the cable or hoses. Use the six
(6) socket head cap screws (76566-24C) included
with the rear manifold tubing assembly to attach
the rear manifold assembly ( A12283) to the robot
spacer plate (see Table 1).
Connect each signal line as required per "Signal
Identification Tables (Metric) Tubing Bundles" in the
"Installation" section.
Rear Plate Assembly
The rear plate assembly is designed to be at ground
potential when mounted to the robot plate compo-
nent within the tubing bundle assembly. The air and
fluid ports are compactly oriented for use in robotic
applications. The interior air supplies are ported
through the five (5) support rods and also directly
tubed to the upper manifold assembly. On the ex-
terior side of the rear plate, the ports are provided
with o-ring seals so that the applicator can be quickly
mated and secured to the robot plate
Robot Plate
The robot plate is a component of the tubing bundle
assembly and intended to be permanently mounted
to the robot. A wrist adapter is also available, which
matches the robot's mounting configuration. The
incoming air lines, fluid lines, low voltage cable, and
fiber optic cable are connected to the fittings provided
on the back of the robot plate. The rear plate of the
applicator assembly is secured to the robot plate with
a threaded retaining ring.
Break-Away Feature (Optional)
The Evolver 303 dual purge can be converted to
have a break-away feature, by replacing the five (5)
stainless steel screws with five (5) special designed
plastic screws (77524-00). This feature is meant to
reduce the damage to the applicator, robot, etc. If a
collision occurs, the five (5) plastic break-away screws
fail and the applicator will break free. This will leave
the break-away ring and the mounting ring attached
to the robot.
Power Supply and Controls
The high voltage cascade located inside the Evolver
303 dual purge is controlled by the MicroPak control
unit. The low voltage ouput of the MicroPak is multi-
plied by the internal cascade to the high voltage level
required. This eliminates the need for a high voltage
cable. A low voltage cable interconnects the cascade
and the MicroPak control. The MicroPak Eurocard
format is designed to fit in a conventional 19-inch
or 1-inch rack and requires a 24V power input at a
maximum 3 amps. The MicroPak and the internal
cascade will produce voltages up to 100,000VDC.
The MicroPak is designed to electronically limit cur-
rent to provide safe operation in a spray booth. The
voltage and current draw of the applicator are con-
tinuously displayed on the MicroPak control panel.
Voltage and over-current limits are adjust-able on
the front of the MicroPak. MicroPak internal safety
circuits will shut down the system on over-current
and cable faults.
With additional control modules, all of the functions
of the Evolver 303 dual purge and MicroPak can be
controlled by a programmable controller. A Serial
Digital Module pneumatically controls the paint and
dump valves located on the applicator. An I/O module
provides communication between these modules
and the PLC.
The above modules are mounted in one 19-inch rack
and interconnected through a common mother-
board.
AA-08-01.1