Burkert Type SE56 User Manual
Page 4
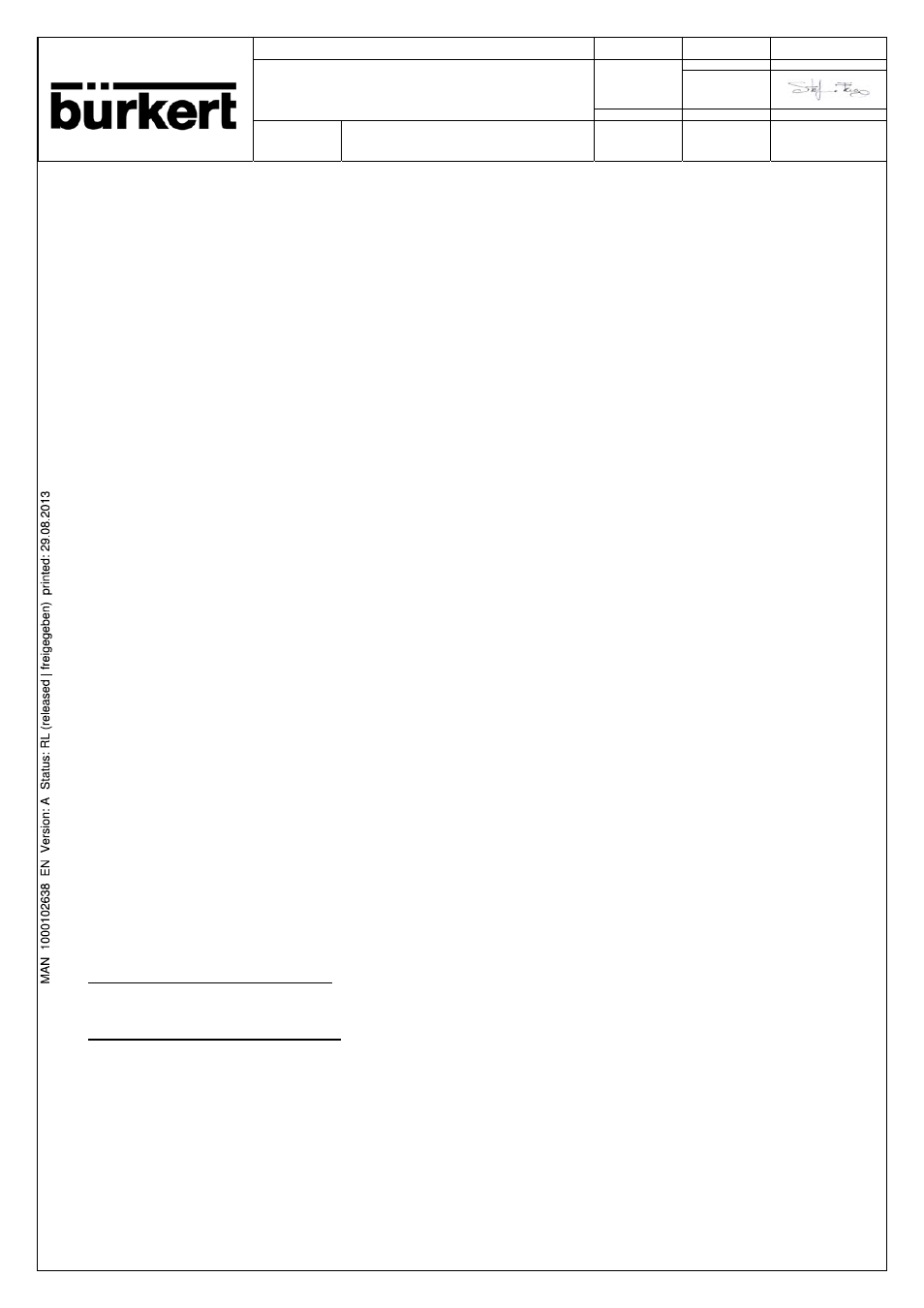
TECHNICAL MANUAL
Rev.
Pagine
4/52
Filling By
Checked By
03
PROFIBUS DP MODULE- DATA LINK
DESCRIPTION
Document Data
Date
Date
File name
ProfibusDP_emanual_Burkert_04.doc
19/03/08 19/03/08 19/03/08
4
The Profibus-DP module mounted in the Electromagnetic Flow Meter is used for to connect the converter of
the Flow meter to the Profibus DP fieldbus in accordance with the DIN 19245 Standard as a passive
instrument (slave).
When this option is installed it is possible to read the process data from the Flow meter.
The process data consists of Dynamic Data and Static Data.
With the keyword Dynamic Data it is indicated measurement values which are continuously changing e.g.
Flow rate, Totalizers, etc..
With the keyword Static Data it is indicated parameters value of the Flow meter which do not change
during operation for example unit Flow rate, unit Totalizers etc. and other parameters that can be
individually written to using the Acyclic Service or an offset to INDEX Output (see Fourth Configuration
with 16 byte Input/Output or Fifth Configuration with 24 byte Input/Output).
The software of the slave module implement the DP standard/DPV1 functionality for the communication of
the slave with a Class 1 (parameterization Master) and a Class 2 Master.
With the data exchange with the Acyclic Service and with the Slot and Acyclic Index it is possible to
send and return configuration parameters of the Flow meter with a Class 1 or Class 2 Master.
For the communication with a Class C1 Master the Slot is ignored.
Only Slot 0 is used for the service of acyclic data exchange for the communication with a Class 2 master.
The module support four type of configurations with is possible sets the better combination of type of
information of the Flow meter.
It is possible select a configuration with only 8 byte or 16 or 24 byte Input and insert or return Static Data
with the Acyclic Service and Class 1 or Class 2 Master.
If the Master doesn't support Acyclic Service it is possible select the fourth configuration with 16 byte
Input/Output or the fifth configuration with 24 byte Input/Output. With these last configuration and
with two bytes, with the function of indexes, and the Output data, it is possible to insert or return Static
Data in the Flow meter.
With the Acyclic Service and with the Slot and Acyclic Index it is possible to read the data stored in the
Internal Data Logger of the Fow Meter.
The Profibus address of the instrument can be set with the converter keypad in the menu Comunication.
Baudrates range supported are from 9.6 kBaud up to 12 MBaud.
The slave module support the Diagnostic and Process Alarms for monitoring Flow rate with four thresholds.
NOTE: After the power supply of the Flow meter is switch on, there is an interval time of 5 seconds during
that the slave module remain in a Reset Phase necessary for the initialization of the Flow meter.
The reading of the data stored in the Internal Data Logger and the settings for the thresholds of the Flow
rate Control are possible only with the Acyclic Service and with the Slot and Acyclic Index.
1.2. PROFIBUS IDENT NUMBER
The Profibus Identification Number is 0008hex ( 8dec ).
1.3. SLAVE PARAMETERIZATION
The parameters specified in this respect reach the slave via the parameterization message of the
parameterization Master.
The parameterization data consists of the following:
- DP standard parameters with a length of 7 bytes according to EN 50170
- DPV1 status bytes with a length of 3 bytes according to extensions of EN 50170 which immediately follow
the specified DP standard parameters