Ds1862 xfp laser control and digital diagnostic ic, Table 10. right-shifting selection – Rainbow Electronics DS1862 User Manual
Page 20
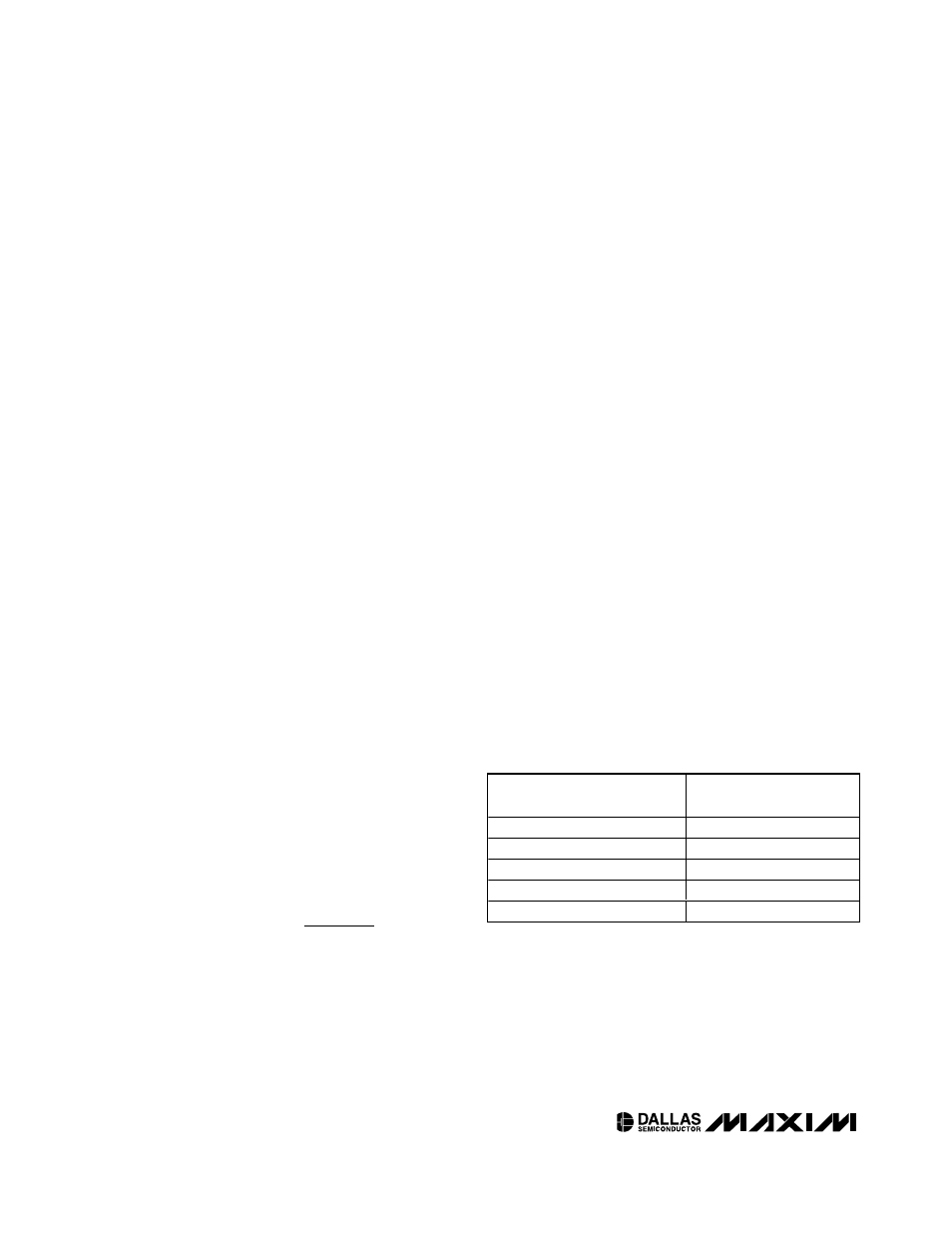
DS1862
XFP Laser Control and Digital Diagnostic IC
20
____________________________________________________________________
/* Assume that the Null input is 0.5V. */
/* In addition, the requirement for LSB is 50µV. */
FS = 65536 * 50e-6;
/* 3.2768 */
CNT1 = 0.5 / 50e-6;
/* 10000 */
CNT2 = 0.90*FS / 50e-6;
/* 58982 */
/* Thus the NULL input of 0.5V and the 90% of FS input
is 2.94912V. */
set the trim-offset-register to zero;
set Right-Shift register to zero (Typically zero.
See the Right-Shifting section);
gain_result = 0h;
CLAMP = FFF8h/2^(Right_Shift_Register);
For n = 15 down to 0
begin
gain_result = gain_result + 2^n;
Force the 90% FS input (2.94912V);
Meas2 = read the digital result from the part;
If Meas2 >= CLAMP then
gain_result = gain_result - 2^n;
Else
Force the NULL input (0.5V);
Meas1 = read the digital result from the part;
if (Meas2 - Meas1) > (CNT2 - CNT1) then
gain_result = gain_result - 2^n;
end;
Set the gain register to gain_result;
The gain register is now set and the resolution of the
conversion will best match the expected LSB. The next
step is to calibrate the offset of the DS1862. With the
correct gain value written to the gain register, again
force the NULL input to the monitor pin. Read the digi-
tal result from the part (Meas1). The offset value is
equal to negative value of Meas1.
The calculated offset is now written to the DS1862 and
the gain-and offset-scaling procedure is complete.
Right-Shifting A/D Conversion Result
(Scalable Dynamic Ranging)
Right-shifting is a digital method used to regain some
of the lost ADC range of a calibrated system. If right-
shifting is enabled, by simply loading a non-zero value
into the appropriate Right-Shifting Register, then the
DS1862 shifts the calibrated result just before it is
stored into the monitor channels’ register. If a system is
calibrated so the maximum expected input results in a
digital output value of less than 7FFFh (50% of FS),
then it is a candidate for using the right-shifting
method.
If the maximum desired digital output is less than
7FFFh, then the calibrated system is using less than 1/2
the ADC’s range. Similarly, if the maximum desired dig-
ital output is less than 1FFFh, then the calibrated sys-
tem is only using 1/8th the ADC’s range. For example, if
an applied maximum analog signal yields a maximum
digital output less than 1FFCh, then only 1/8th of the
ADC’s range is used. Right-shifting improves the reso-
lution of the measured signal as part of internal calibra-
tion. Without right-shifting, the 3 MS bits of the ADC will
never be used. In this example, a value of 3 for the
right-shifting maximizes the ADC range and a larger
gain setting must be loaded to achieve optimal conver-
sion. No resolution is lost since this is a 13-bit converter
that is left justified. The value can be right-shifted 3
times without losing any resolution. The following table
describes when the right-shifting method can be effec-
tively used.
OFFSET REGISTER
MEAS
_
(
)
=
−
⎡
⎣⎢
⎤
⎦⎥
1
1
4
Table 10. Right-Shifting Selection
OUTPUT RANGE USED WITH
ZERO RIGHT-SHIFTS
NUMBER OF RIGHT-
SHIFTS NEEDED
0h .. FFFFh
0
0h .. 7FFFh
1
0h .. 3FFFh
2
0h .. 1FFFh
3
0h .. 0FFFh
4