HEIDENHAIN iTNC 530 (340 420) ISO programming User Manual
Page 230
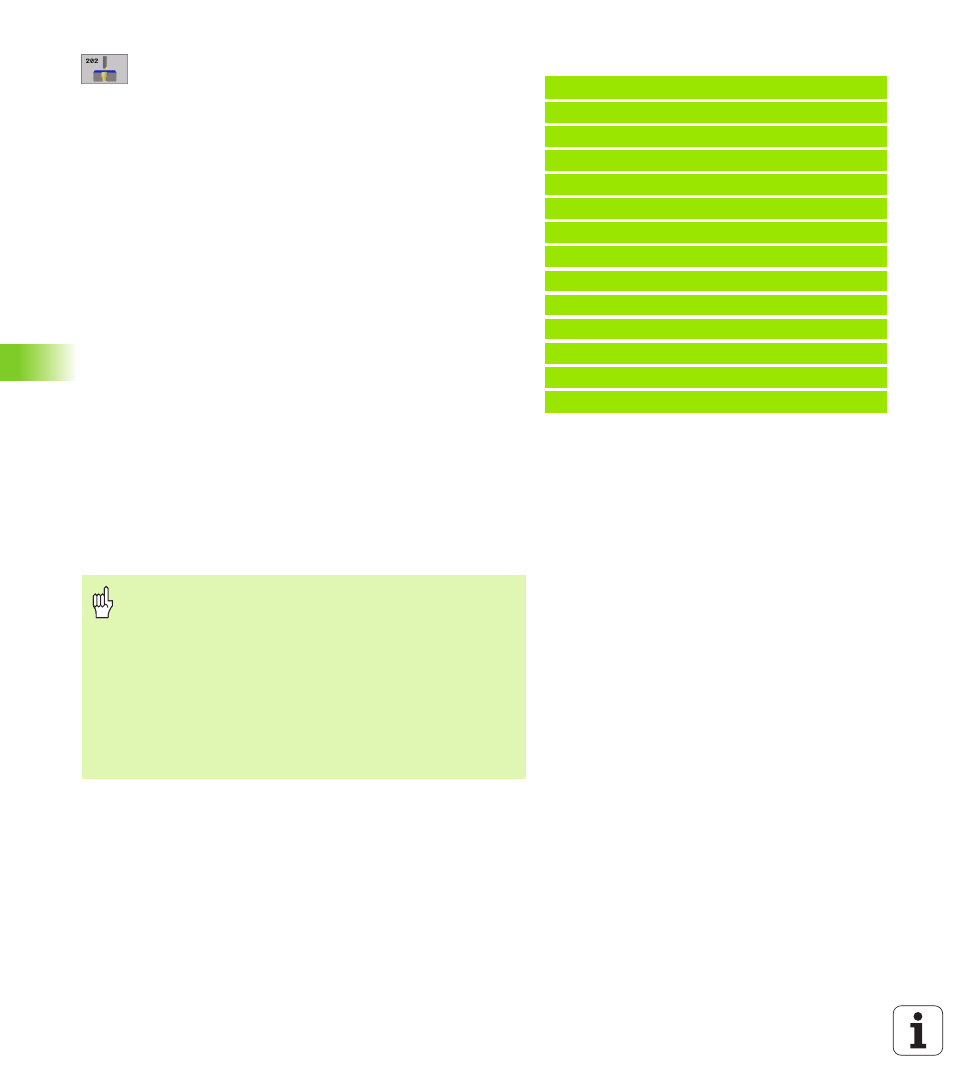
230
8 Programming: Cycles
8.3 Cy
cles f
o
r Dr
illing, T
a
pping and Thr
ead Milling
U
U
U
U
Set-up clearance
Q200 (incremental value): Distance
between tool tip and workpiece surface.
U
U
U
U
Depth
Q201 (incremental value): Distance between
workpiece surface and bottom of hole.
U
U
U
U
Feed rate for plunging
Q206: Traversing speed of
the tool during boring in mm/min.
U
U
U
U
Dwell time at depth
Q211: Time in seconds that the
tool remains at the hole bottom.
U
U
U
U
Retraction feed rate
Q208: Traversing speed of the
tool in mm/min when retracting from the hole. If you
enter Q208 = 0, the tool retracts at feed rate for
plunging.
U
U
U
U
Workpiece surface coordinate
Q203 (absolute
value): Coordinate of the workpiece surface.
U
U
U
U
2nd set-up clearance
Q204 (incremental value):
Coordinate in the tool axis at which no collision
between tool and workpiece (clamping devices) can
occur.
U
U
U
U
Disengaging direction
(0/1/2/3/4) Q214: Determine
the direction in which the TNC retracts the tool at the
hole bottom (after spindle orientation).
0: Do not retract tool
1: Retract tool in the negative reference axis direction
2: Retract tool in the negative secondary axis direction
3: Retract tool in the positive reference axis direction
4: Retract tool in the positive secondary axis direction
U
U
U
U
Angle for spindle orientation
Q336 (absolute
value): Angle at which the TNC positions the tool
before retracting it.
Example:
N100 G00 Z+100 G40
N110 G202 BORING
Q200=2
;SET-UP CLEARANCE
Q201=-15
;DEPTH
Q206=100
;FEED RATE FOR PLUNGING
Q211=0.5
;DWELL TIME AT DEPTH
Q208=250
;RETRACTION FEED RATE
Q203=+20
;SURFACE COORDINATE
Q204=100
;2ND SET-UP CLEARANCE
Q214=1
;DISENGAGING DIRECTN
Q336=0
;ANGLE OF SPINDLE
N120 X+30 Y+20 M3
N130 G79
N140 L X+80 Y+50 FMAX M99
Danger of collision
Select a disengaging direction in which the tool moves
away from the edge of the hole.
Check the position of the tool tip when you program a
spindle orientation to the angle that you enter in Q336 (for
example, in the Positioning with Manual Data Input mode
of operation). Set the angle so that the tool tip is parallel to
a coordinate axis.
During retraction the TNC automatically takes an active
rotation of the coordinate system into account.