Introduction, 1 features, 1 introduction – LINK Systems 5100-8 Tonnage & Analog Signal Monitor User Manual
Page 7
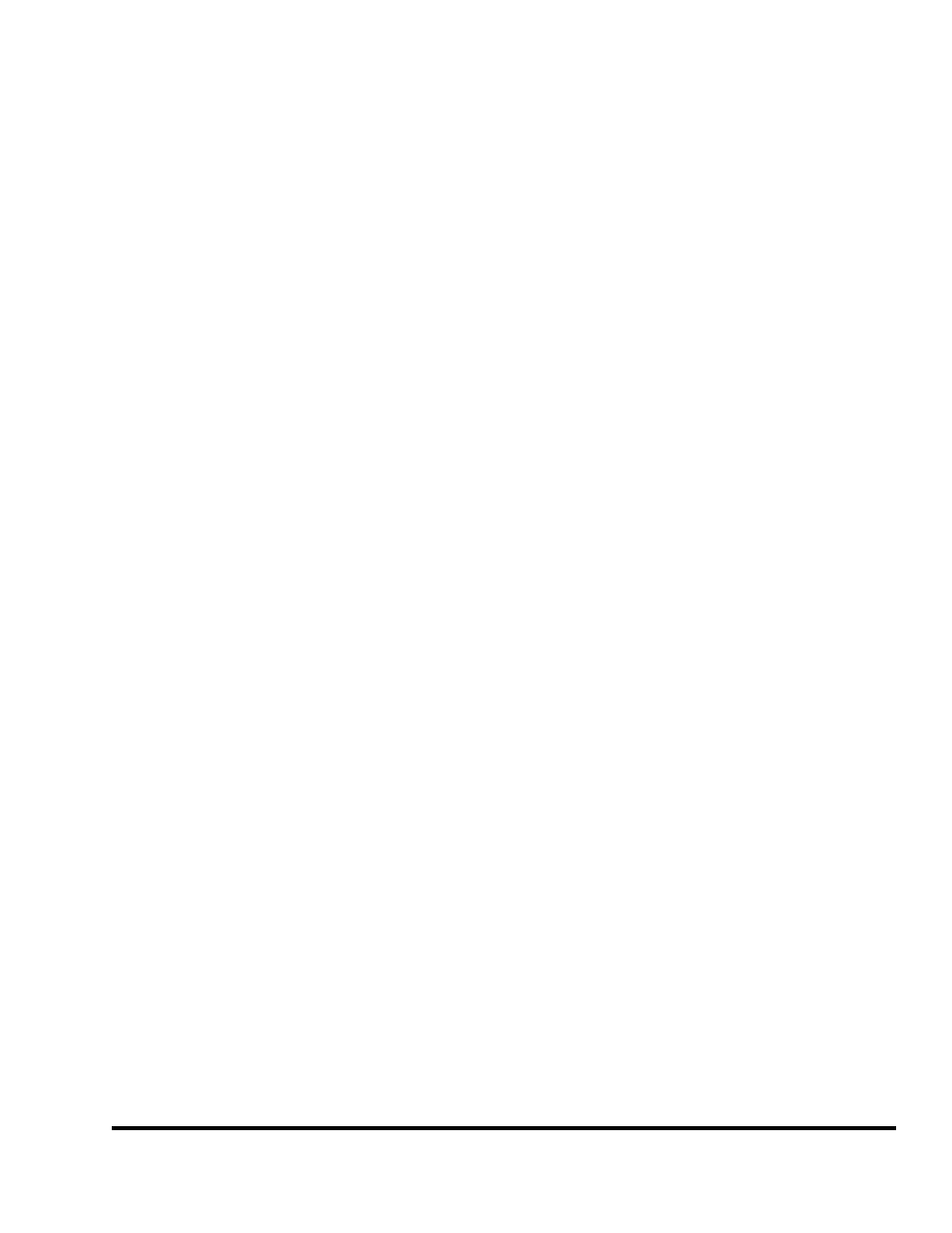
Doc
#:
L-802-1110 Page
5
Rev.
02
1 INTRODUCTION
The Tonnage and Analog Signal Monitor module is available as optional module with both the
OmniLink II Press Automation Control and the System 5000 Press Control. Its primary purpose is to
measure and display the force being applied to the frame of a mechanical power press. The force
applied during the working portion of the stroke is compared with allowable limits based on the capacity
of the machine and correct operation of the die and material being used. Tonnages beyond these limits
cause various types of stop signals to be sent to the press control depending upon the importance of the
overload. Present tonnage readings, status messages, present tonnage limits, and detailed tonnage versus
angle graphs (signatures) can be examined or programmed through the same Operator Terminal as all
other OmniLink II or System 5000 settings. Additional options (detailed below) can be added to
provide even more capabilities.
1.1 Features
• The base Tonnage and Analog Signal Monitor module provides four strain link connections for use
on two or four channel machines.
• The 5100-8A option adds an additional four channels that work with strain gages, 4-20 milliamp
output sensors, and voltage output sensors. This option enables in-die on-the-fly analog part
measurement.
• In conjunction with the 5100-8A option, certain servo controllers can be tied in to the tonnage
monitor to allow in-die process adjustment based on the measurement of parts.
• The 5100-8C option adds four standard die protection inputs and four programmable limit switch
outputs.
• The crankshaft angle is supplied to the module via internal communication with the OmniLink II
Press Automation Control or the System 5000 Press Control. Position dependent parameters such as
the working portion of the stroke or data window settings are entered directly into the Tonnage and
Analog Signal Monitor module requiring no external cam switches.
• The same internal communication allows the module to instruct the control to Top Stop or Cycle
Stop depending on the type of tonnage alarm that has occurred.
• A graph of tonnage versus crankshaft angle (tonnage signature) can be displayed for each channel or
the total. This graph also shows the active areas of the data windows, if used.
• One reference signature per job can be stored and overlaid with the current signature for comparison.
• For each job, limits can be set for the maximum allowable forward tonnage (High Limit), minimum
required forward tonnage (Low Limit), and maximum allowable reverse tonnage (Reverse Limit) on
a channel by channel basis.