4 supply air discharge, 0 mechanical (cont'd), 3 unit inlet air (cont'd) – Reznor RPB Unit Installation Manual User Manual
Page 20
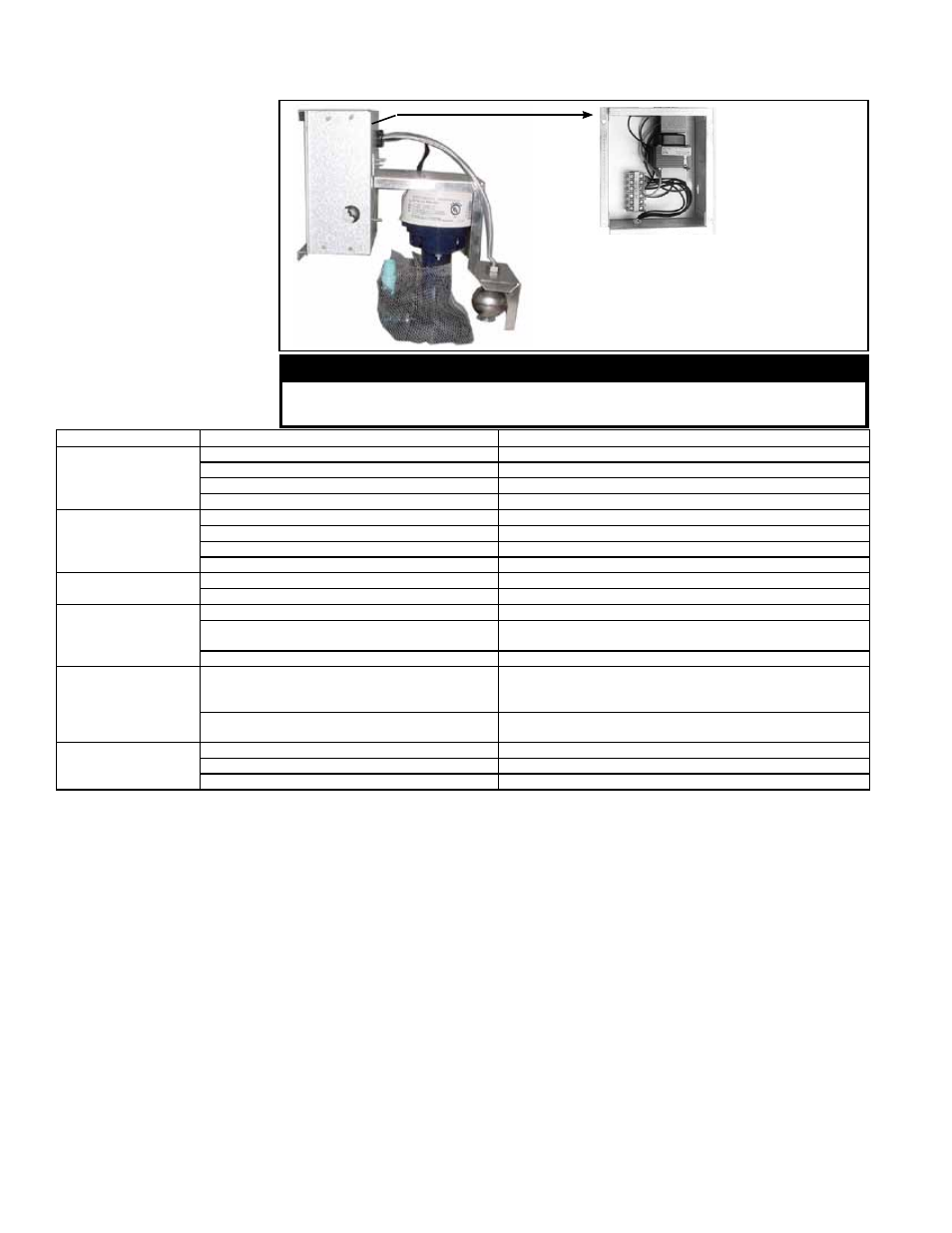
Form I-RPB, P/N 131782 R11, Page 20
6.3.4 Evaporative Cooling Module, Option AS 3, 4, 5, 8 (cont'd)
6.3 Unit Inlet Air (cont'd)
6.0 Mechanical
(cont'd)
WARNING
Disconnect the power before servicing the cooling module. Failure to
do so can cause electrical shock, personal injury or death.
Troubleshooting
Evap Cooler
Problem
Probable Cause
Remedy
Pump does not run.
Unit is calling for cooling
(control switch is in cooling
position) and reservoir is full.
1. Electrical connections
1. Verify all electrical connections. See Wiring Diagram.
2. Electric float switch on pump
2. Check position of the actuators on the electric float switch.
3. Dirty pump
3. Clean pump. See
FIGURE 22.
4. Defective pump
4. Replace pump.
Required water level (3")
not maintained (pump
and float control system)
1. Float valve
1. Adjust float valve. See Filling and Adjusting Water Level.
2. Optional drain and fill valves
2. Check valve for proper operation. See
FIGURE 16.
3. Incorrect overflow pipe nipple - should be 3-1/2"
3. Replace pipe nipple.
4. Drain leaking
4. Tighten drain plug.
Water running off of
media pads
1. Excessive water flow
1. See adjust water flow instructions.
2. Media needs cleaned or replaced.
2. Clean or replace media pads.
Water not distributing
evenly
1. Distribution line clogged
1. Flush distribution line. See Evap Cooling Module Maintenance.
2. Holes in distribution line turned
2. Check position of distribution line. Holes should be spraying
upward. If not positioned with holes up, adjust position of line.
3. Incorrect voltage to pump
3. Check voltage at pump terminal in cooling module junction box.
Media pads becoming
clogged & discolored
(scale/salt deposits) and/
or rapid deterioration of
the float switch
1. Bleed off line clogged or inadequate bleed off
(pump and float control system)
1. Clean bleed line (See
FIGURE 17). A uniform build-up of
minerals on the entering air face of the media indicates insufficient
bleed off. Increase the rate until the mineral deposits dissipate.
2. Excessive water flow
2. See Adjusting Water Flow.
Water blowoff from
media pads
1. Media pads installed incorrectly
1. Install media pads correctly. See Cooling Module Maintenance.
2. Requires moisture elimination pad (over 600 FPM) 2. Install moisture elimination pad. Consult factory.
3. Water level not 3 inches (pump and float control ) 3. See second problem listed above (Required water level)
6.4 Supply Air
Discharge
6.4.1. Duct
Connections
Requirements & Suggestions for Connecting and Installing Ducts
•
Type of Ductwork - The type of duct installation to be used depends in part on the
type of construction of the roof (whether wood joist, steelbar joist, steel truss, pre-
cast concrete) and the ceiling (whether hung, flush, etc.).
•
Ductwork Material - Rectangular duct should be constructed of not lighter than
No. 26 U.S. gauge galvanized iron or No. 24 B & S gauge aluminum.
•
Ductwork Structure - All duct sections 24 inches or wider, and over 48 inches
in length, should be cross broken on top and bottom and should have standing
seams or angle-iron braces. Joints should be S and drive strip, or locked.
•
Through Masonry Walls - No warm air duct should come in contact with masonry
walls. Insulate around all air duct through masonry walls with not less than 1/2" (1"
is recommended) of insulation.
•
Through Unheated Space - Insulate all exposed warm air ducts passing through
an unheated space with at least 1/2" (1" is recommended) of insulation.
•
Duct Supports - Suspend all ducts securely from adjacent buildings members. Do
not support ducts from unit duct connections.
System has either a horizontal or vertical discharge air opening with a duct flange.
If the discharge outlet is vertical, the system was ordered with either a factory-installed
downturn plenum (AQ Option).
Pump
Inside View of the
Junction Box
(Note: Only 208V
unit will have a
transformer in the
junction box.)
Float
Switch
Pump
Motor
To clean the pump, carefully
remove the mesh screening
(or basket) and the snap-on
cover plate.
FIGURE 22 - Remove
Junction Box, Pump
and Float Switch as an
Assembly
(
NOTE: Applies to
evaporative cooling
module with float and
pump control system
only. Depending on date
of manufacture, actual
assembly may not appear
exactly as in the photo.)