2 venting, 0 mechanical (cont'd), 1 gas piping and pressures (cont'd) – Reznor RPB Unit Installation Manual User Manual
Page 10
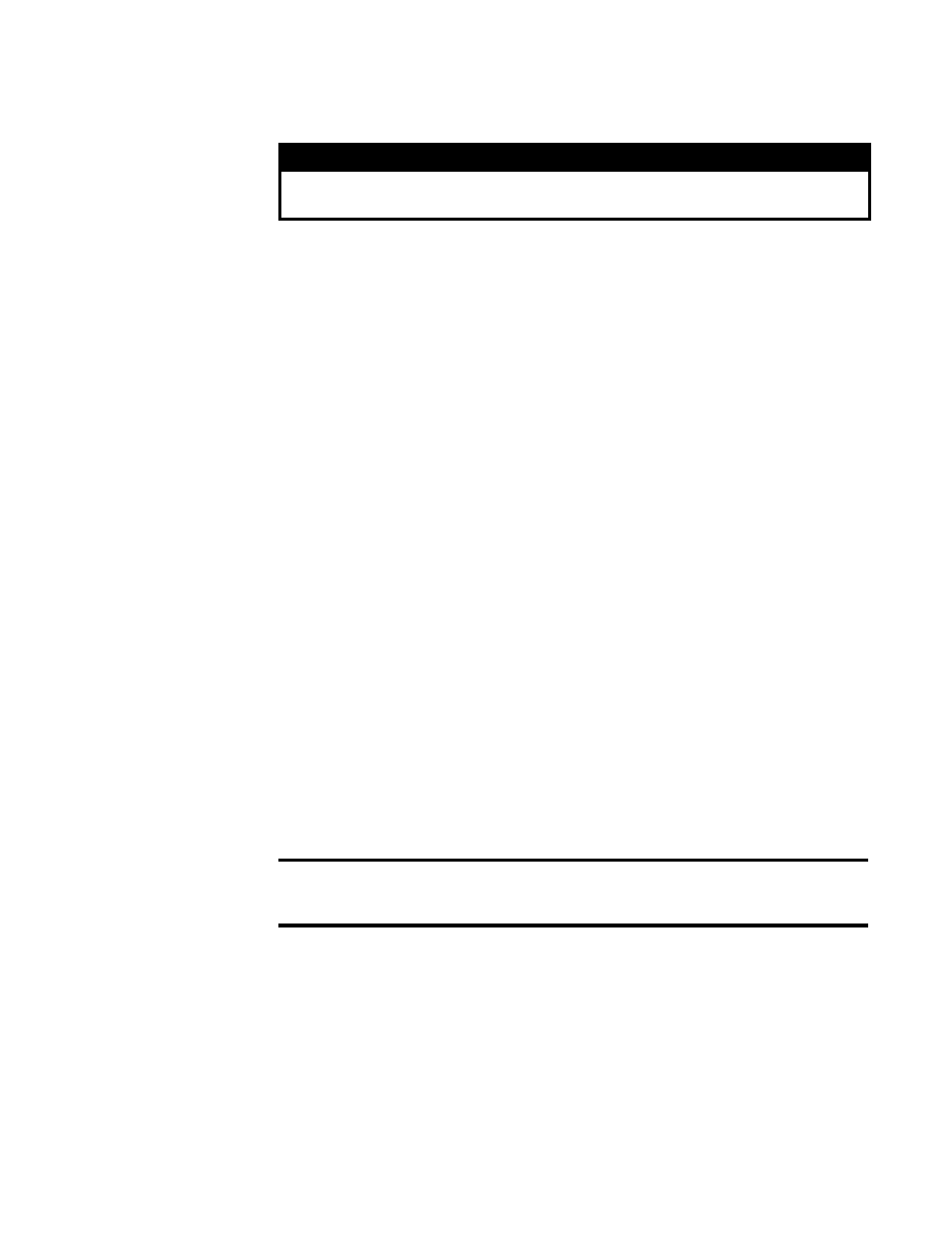
Form I-RPB, P/N 131782 R11, Page 10
6.0 Mechanical
(cont'd)
6.1 Gas Piping
and Pressures
(cont'd)
Measuring manifold gas pressure cannot be done until the heater is in operation. It is
included in the steps of the "Check-Test-Start" procedure in Paragraph 9.0. The follow-
ing warnings and instructions apply.
WARNING
Manifold gas pressure must never exceed 3.5" w.c. for natural gas
and 10" w.c. for propane gas.
For Natural Gas: When the heater leaves the factory, the combination valve is set so
that the outlet gas pressure of a single-stage valve or high fire of a two-stage valve is
regulated to 3.5" w.c. Low fire on a two-stage valve is set to 1.8" w.c. Inlet supply pres-
sure to the valve must be a minimum of 5" w.c. or
as noted on the rating plate and a
maximum of 14" w.c.
NOTE: Always check the rating plate for minimum gas sup-
ply pressure. Minimum supply pressure requirements vary based on size of burner
and the gas control option. Most units require a minimum of 5" w.c. of natural gas as
stated above, but Sizes 350 and 400 with electronic modulation require a minimum of
6" w.c. natural gas supply pressure. Sizes 300 and 350 with mechanical modulation
require 7" w.c.
For Propane: When the heater leaves the factory, the combination valve is set so that
the outlet gas pressure of a single-stage valve or high fire of a two-stage valve is 10"
w.c. Low fire on a two-stage valve is set to 5" w.c. Inlet pressure to the valve must be a
minimum of 11" w.c. and a maximum of 14" w.c.
Before attempting to measure or adjust manifold gas pressure, the inlet (supply) pres-
sure must be within the specified range for the gas being used both when the heater is
in operation and on standby. Incorrect inlet pressure could cause excessive manifold
gas pressure immediately or at some future time.
Manifold or Orifice (Valve Outlet) Pressure Settings
6.2 Venting
Locate power-vented furnaces so that flue discharge is not directed at fresh air inlets.
The flue discharge openings are located on the side of the furnace just above the con-
trol access panel. The position of this opening discourages recirculation of combustion
products and provides for furnace operation in all normal weather conditions.
Optional Vertical Flue
Discharge (Option CC3)
These power vented furnaces are certified with four feet of vertical pipe attached as
shown in
FIGURES 6A and 6B. The distance is measured from the top of the unit to
the bottom of the vent cap. The option package includes the 5" vent cap, the adapter
assembly and the seal plate. The vent pipe and supports are field supplied.
Optional vertical vent piping provides compliance with local codes that require either
10-ft horizontal or 4-ft vertical clearance between the flue outlet and fresh air intake of
the heating system and/or the building.
Instructions to Check Valve Outlet (Manifold) Pressure:
1) With the manual valve (on the combination valve) positioned to prevent flow to the
main burners, connect a manometer to the 1/8" pipe outlet pressure tap in the valve.
NOTE: A manometer (fluid-filled gauge) is recommended rather than a spring type
gauge due to the difficulty of maintaining calibration of a spring type gauge.
2) Open the valve and operate the heater. Measure the gas pressure to the manifold.
To measure the low stage pressure on units equipped with a two-stage valve, discon-
nect the wire from the "HI" terminal on the valve. (Be sure to reconnect the wire.)
Normally adjustments should not be necessary to the factory preset regulator. If adjust-
ment is necessary, set pressure to correct settings by turning the regulator screw IN
(clockwise) to increase pressure. Turn regulator screw OUT (counterclockwise) to
decrease pressure. Consult the valve manufacturer's literature provided with the fur-
nace for more detailed information.
CAUTION: DO NOT bottom out the gas valve regulator adjusting screw.
This can result in unregulated manifold pressure causing overfire and
heat exchanger failure.