Carrier 39L User Manual
Page 49
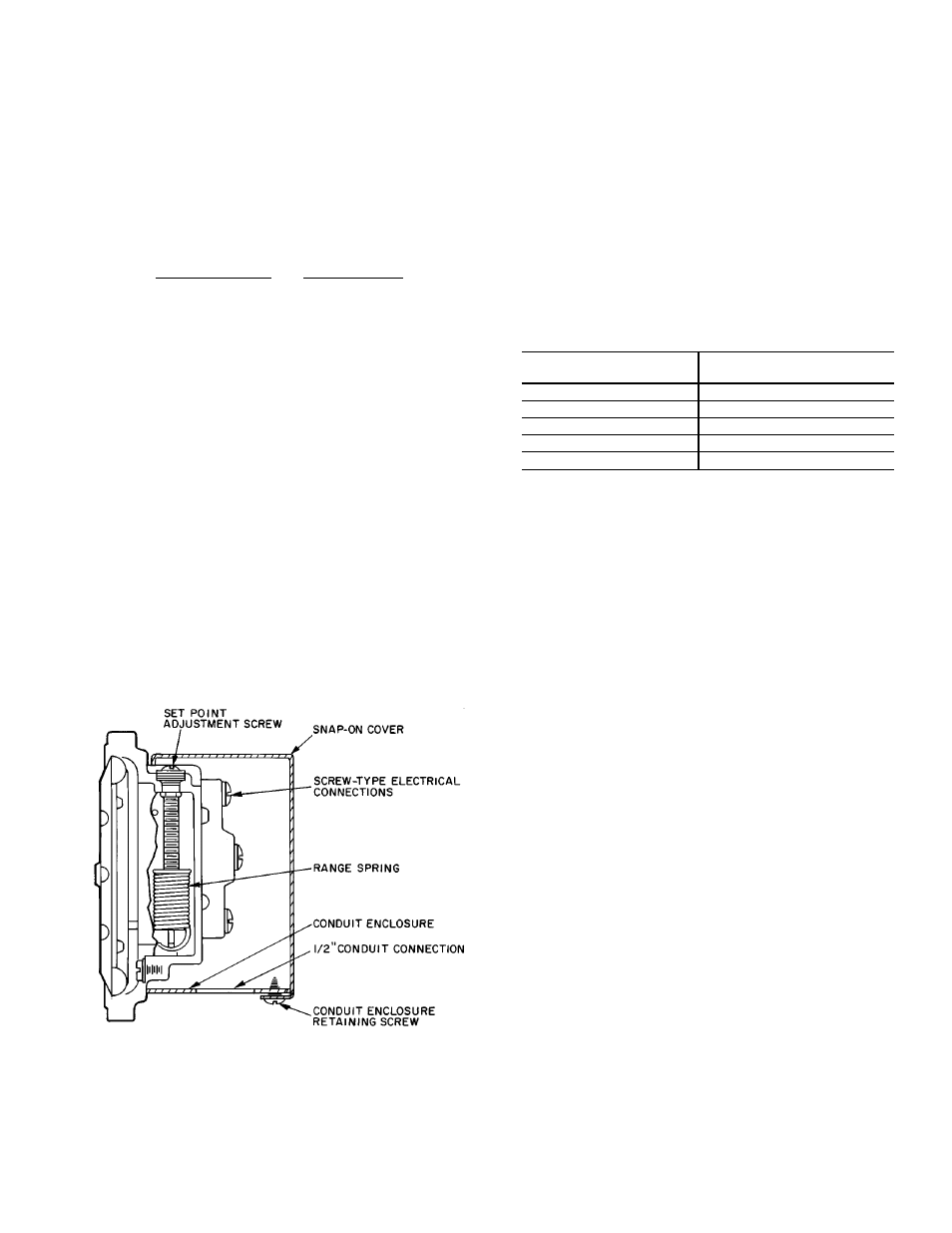
Filter Status Switch —
The filter status switch (FLTS)
is factory-installed in the filter section on all PIC-equipped
units. The switch is a snap-acting SPDT switch. When dirty
filter elements cause the pressure drop across the filter me-
dia to exceed the switch setting, the switch closes and sends
an alarm signal to the PIC.
The 39L units use a single switch. In 39NX units, up to
3 switches can be connected in parallel. When the switches
are wired in parallel, it is not possible to isolate an alarm
signal to a single switch.
The FLTS has an operating range of 0.05 to 2.0 in. wg.
Factory settings for the switch are as follows:
Filter Type
Setting (in. wg)
Flat
0.5
Bag/Cartridge
1.0
Final
1.5
The FLTS electrical ratings are as follows:
300 va pilot duty at 115 to 277 vac
10 amps non-inductive to 277 vac
Rated for NO (normally open) and NC (normally closed)
contacts.
High-Pressure Switch (Fig. 38) —
The high-
pressure switch (HPS) is factory installed in the PIC control
box on VAV units only. It is a snap-acting SPDT switch with
manual reset that is used to shut down the supply fan when-
ever the duct pressure reaches the switch setting. The manual
reset is used to restart the fan after the problem has been
corrected.
The switch is factory set at 3.0 in. wg. It has a range of
1.4 to 5.5 in. wg and can be field adjusted for specific
applications.
Adjust the high-pressure switch setting as follows:
1. Loosen conduit enclosure retaining screw, pull firmly on
the bottom end and snap off cover.
2. Raise set point by turning slotted adjustment screw
(located at top of range spring housing) clockwise. Turn
adjustment screw counterclockwise to lower set point.
3. To change or check calibration, use a T assembly with
3 rubber tubing leads. Attach one lead to the HPS and
another to an accurate manometer with the appropriate
range. Apply pressure through the third lead and ap-
proach set point slowly.
4. Adjust set point to at least 0.5 in. wg greater than con-
figured static pressure set point.
Air Quality Sensors (Fig. 39) —
The air quality (AQ)
sensors are shipped inside the fan section for field installa-
tion. Two types of sensors are supplied; one sensor monitors
the conditioned air space, and the other sensor monitors the
return air duct. Both sensors use infrared technology to de-
tect the levels of CO
2
present in the air.
Sensor descriptions and part numbers are shown in
Table 6. To mount the sensor, refer to the installation in-
structions shipped with the sensor.
Table 6 — CO
2
Sensor Accessories
CO
2
SENSOR ACCESSORY
PART NUMBERS
DESCRIPTION
CGCDXSEN001A00
Wall Mount Sensor (No Display)
CGCDXSEN002A00
Wall Mount Sensor with Display
CGCDXSEN003A00
Duct Mount Sensor (No Display)
CGCDXGAS001A00
Sensor Calibration Service Kit
CGCDXPRM001A00
User Interface Program (UIP)
The CO
2
sensors listed in Table 6 are all factory set for a
range of 0 to 2000 ppm and a linear voltage output of 2 to
10 vdc. Fig. 40 shows ventilation rates for various CO
2
set
points when outside air with a typical CO
2
level of 350 ppm
is used to dilute the indoor air. Refer to the instructions sup-
plied with the CO
2
sensor for electrical requirements and
terminal locations.
Any changes to the sensor’s factory configuration require
the purchase of the User Interface Program (UIP) or Sensor
Calibration Service Kit, which also contains the UIP.
To accurately monitor the quality of the air in the condi-
tioned air space, locate the sensor near the return air grille
so it senses the concentration of CO
2
leaving the space. The
sensor should be mounted at least 1 ft above or 1 ft below
the thermostat to avoid direct breath contact.
Do not mount the space sensor in drafty areas such as near
supply ducts, open windows, fans, or over heat sources. Al-
low at least 3 ft between the sensor and any corner. Avoid
mounting the sensor where it is influenced by the supply air;
the sensor gives inaccurate readings if the supply air is blown
directly onto the sensor or if the supply air does not have a
chance to mix with the room air before it is drawn into the
return air stream.
To accurately monitor the quality of the air in the return
air duct, locate the sensor at least 6 in. upstream or 15 in.
downstream of a 90 degree turn in the duct. The downstream
location is preferred. Mount the sensor in the center of the
duct.
If the sensor is mounted in the return air duct, readjust the
mixed-air dampers to allow a small amount of air to flow
past the return air damper whenever the mixing box is fully
open to the outside air. If the damper is not properly ad-
justed to provide this minimum airflow, the sensor may not
detect the indoor-air quality during the economizer cycle.
Fig. 38 — High-Pressure Switch (P/N HH02WC001)
49