Carrier 39L User Manual
Page 100
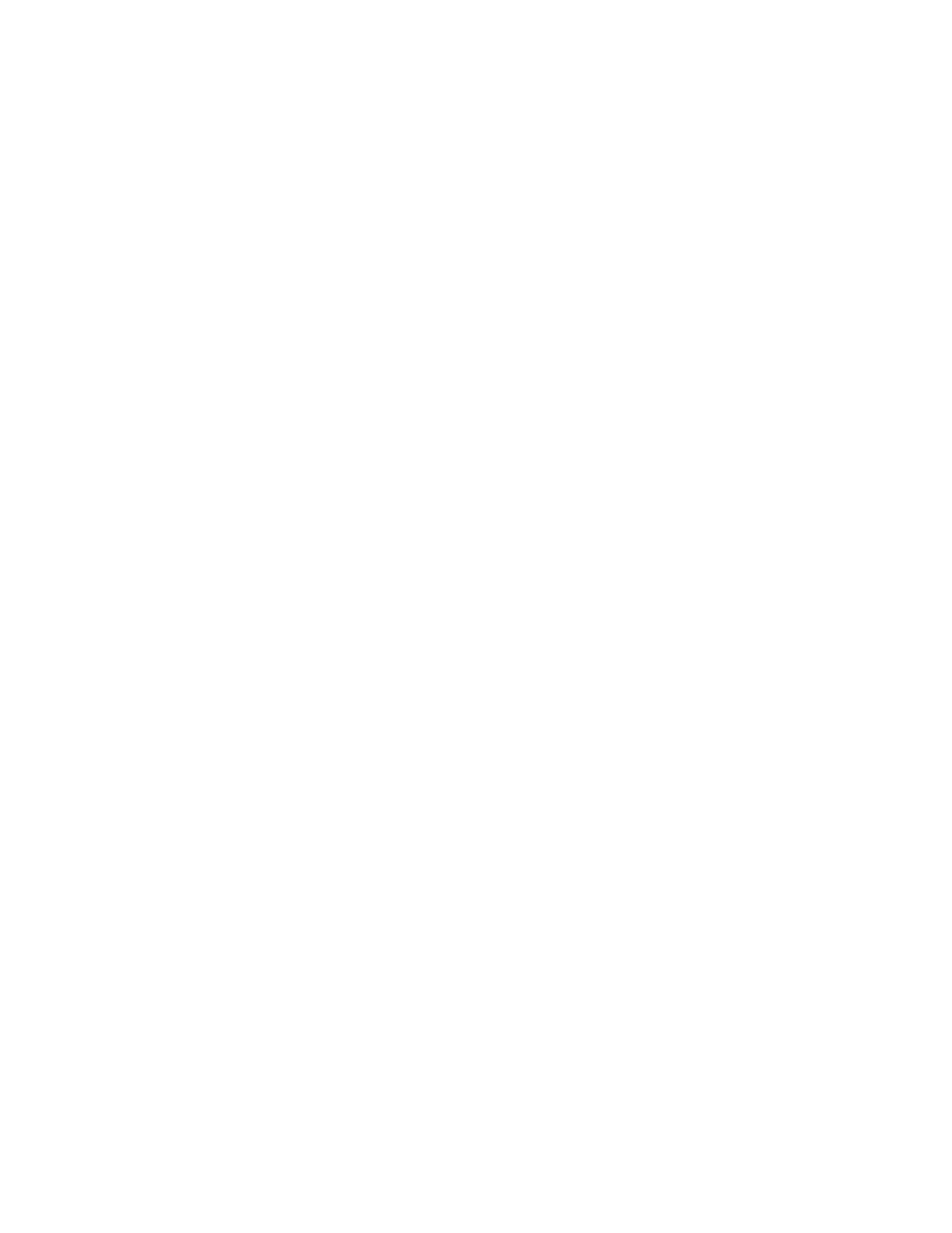
HEATING COIL CONTROL — The heating coil control ad-
justs the steam or hot water valve. Heat is primarily used for
morning warm-up or Occupied Heating with the valve modu-
lated to maintain desired return-air temperature.
If the supply fan is OFF, the heating valve is modulated
to maintain a desired minimum duct temperature (fan off value).
If the fan is ON, the system determines if it is in the morn-
ing warm-up mode. If it is, the return-air sensor is read and
compared to the Occupied Heating set point. If heating is
required, the control calculates the supply-air temperature
required to satisfy conditions.
Once the required supply-air temperature has been cal-
culated, it is compared to the actual supply-air temperature
and the heating coil valve modulates to the required
position.
The heat interlock relay is energized whenever there is a
need for heat.
Once morning warm-up is completed, heat is activated again
unless Occupied Heat has been selected.
During cooling or fan-only operation, heat can also be pro-
vided to maintain the supply-air temperature when the amount
of cold outside air admitted by the IAQ or OAC controls
causes the temperature to fall below the supply-air set point.
CHILLED WATER COIL COOLING CONTROL — The
cooling coil control adjusts the chilled water valve. The valve
is modulated to maintain desired supply-air temperature set
point. The valve is held in its normal position whenever the
system is in Nighttime Free Cooling or whenever the supply
fan is OFF.
If the fan is ON, the control reads the humidity sensor and
compares the value to the high humidity limit.
If the humidity is higher than the humidity limit, the chilled
water valve fully opens.
If the humidity is below the high humidity limit, or if no
humidity sensor is supplied, the control reads the supply-air
sensor and computes the supply-air temperature required to
satisfy conditions, provided that return-air temperature is greater
than the Occupied Cooling set point.
Once the required supply-air temperature has been cal-
culated, it is compared to the current supply-air temperature
and the chilled water valve modulates to the position re-
quired to maintain desired conditions.
See Fig. 77 for cooling operation flowchart.
STATIC PRESSURE CONTROL — The static pressure con-
trol adjusts the inlet guide vanes (IGVs) or the supply-fan
motor inverter in a variable air volume system in order to
maintain the duct static pressure set point.
If the supply fan is OFF, the IGVs remain closed or the
minimum signal is sent to the inverter.
If the fan is ON, the system reads the duct static pressure
sensor and computes the static pressure required to satisfy
conditions. The system compares the duct static pressure to
the computed value and calculates the required signal that is
output to the IGV actuator or the inverter.
FAN VOLUME CONTROL — Fan volume control adjusts
the inlet guide vanes or inverter in a VAV system. The return
fan IGVs or inverters are modulated to maintain a constant
differential cfm value between the supply and return fans in
the system.
If the supply fan is OFF, the return fan inlet guide vanes
are closed and no signal is sent to the return fan inverter.
If the supply fan is ON, the control reads the supply fan
differential pressure transmitter and computes the supply cfm.
The desired return cfm is calculated by subtracting the dif-
ferential cfm set point from the calculated supply cfm. The
return cfm is read and the return fan differential pressure re-
quired to satisfy conditions is calculated.
The calculated return fan differential pressure is com-
pared to the current differential pressure. The signal required
to satisfy conditions is sent to the return fan inlet guide vane
actuator or return fan inverter.
DIRECT EXPANSION COOLING CONTROL — The di-
rect expansion (DX) cooling control regulates the DX cool-
ing system. The DX cooling stages are energized and deen-
ergized to maintain the desired supply-air temperature set
point. Whenever the system is in Nighttime Free Cooling
mode or whenever the supply fan is off, the DX cooling stages
remain off.
If the supply fan is on, the control reads the humidity sen-
sor (if supplied) and compares the value to the high humid-
ity limit. If the humidity is higher than the high humidity
limit, the DX cooling stages are energized to maintain a mini-
mum supply-air temperature. If the humidity is below the
limit, the control reads the space temperature sensor and com-
putes the supply-air temperature required to satisfy
conditions.
Once the required supply-air temperature has been cal-
culated, it is compared to the actual supply-air temperature
and the required DX cooling stages are energized to main-
tain the desired conditions.
See Fig. 77 for cooling operation and Fig. 78 for DX sub-
master gain operation. For more complete information, refer
to the Application Data book for Product Integrated
Controls with DX Cooling
ELECTRIC HEATER CONTROL — Electric heater stag-
ing regulates the electric heater. The heater is primarily used
for morning warm-up or Occupied Heating, with the heater
staged to maintain desired return air temperature. (The num-
ber of heat stages is factory set for each unit heater.)
If the supply fan is OFF, all stages of electric heat are
turned off.
If the fan is ON, the control determines if the system is in
morning warm-up. If it is, the return-air sensor is read and
compared to the Occupied Heating set point. If heat is re-
quired, the control calculates the supply-air temperature re-
quired to satisfy conditions.
Once the required supply-air temperature has been cal-
culated, it is compared to the supply-air temperature to de-
termine the number of heat stages required to satisfy con-
ditions. The required stages are energized sequentially with
2-second intervals between stages and the heat interlock re-
lay is energized. For VAV units, the number of stages turned
on is limited by the PIC IGV output.
Once the morning warm-up is completed, heat is not ac-
tivated again unless OCCUPIED HEAT has been selected.
100