Welch Allyn Duet CO2 Module - User Manual User Manual
Page 14
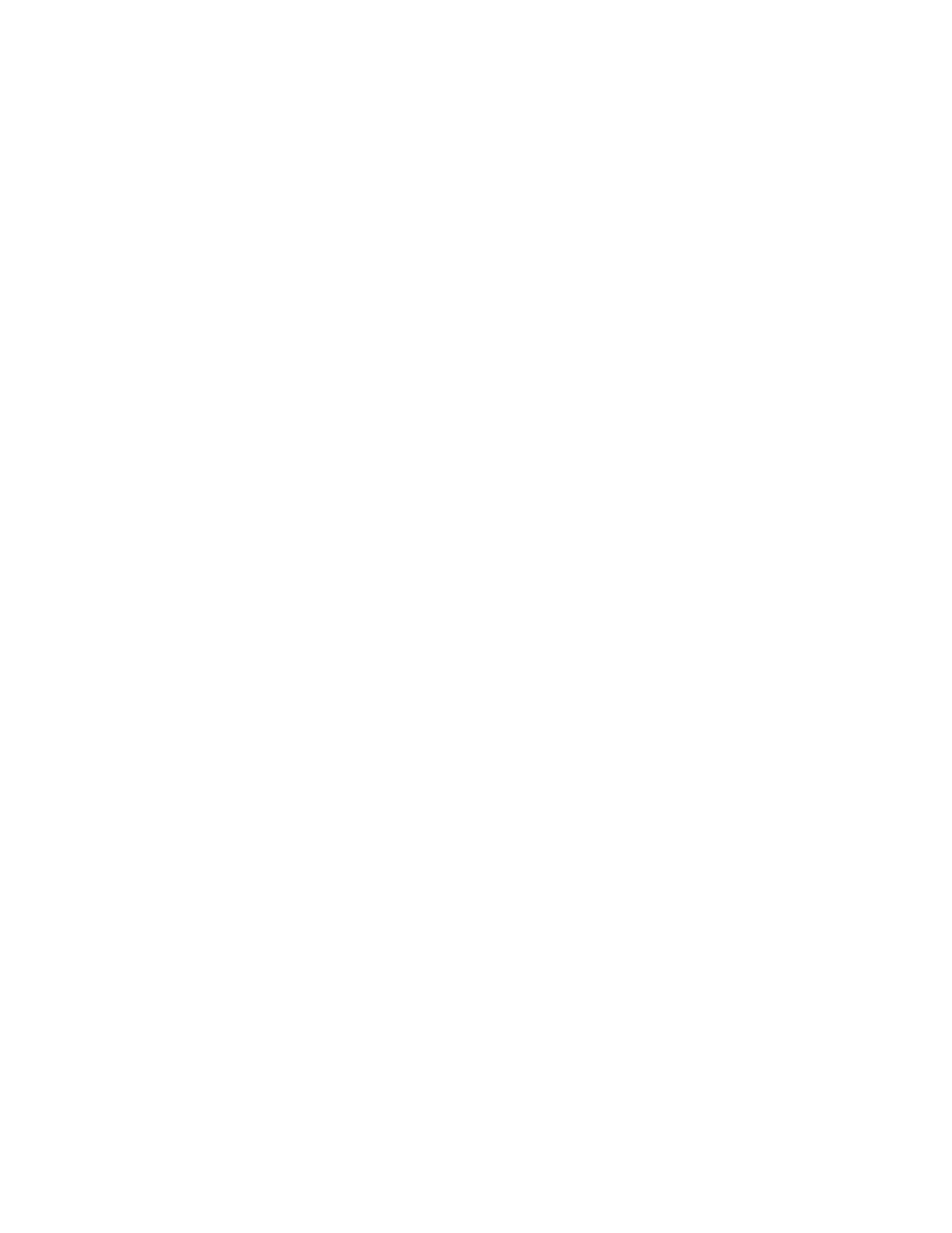
Duet CO
2
Module OEM Implementation Manual
Page 14
Confidential
Welch Allyn OEM Technologies
68HC11 Microprocessor
The microprocessor controls feedback to the temperature and pressure transducers, heater output in
mainstream applications and pump flow in sidestream applications. The microprocessor also provides
the communication interface to the host system and the interfaces to the external A/D and D/A
converters and sensor EEPROM memory. An internal multiplexed A/D converter is used for digital
conversion and for monitoring some of the power supplies for fault determinations.
All address decoding is done by the microprocessor. The software code is stored in FLASH memory
and is supplemented by an external static RAM chip. The boot mode of the microprocessor is used to
install new software into the FLASH device.
Reset Circuit
The first section of a 556 timer is connected to a serial receive data line such that the microprocessor is
forced into reset if the data line is held in a break condition for greater than 10 msec. A second timer
section is used to ascertain if the break condition is maintained for more than 500 msec.
Holding the receive data line in a break condition for a period of time greater than 10 msec and less
than 500 msec is referred to as a reset.
A hard reset occurs when the break condition is held longer than 500msec. This condition forces the
microprocessor to enter the boot mode after the break is released.
A reset controller performs power ON, reset and low voltage lockouts. Under voltage lockout is set to
approximately 4.5 V. On power up, the microprocessor is held in reset for about 100 msec after the
supply rises above 4.5 V.
Primary Power Supplies
All primary power supplies run off a single voltage power source and are converted on the main board
to various levels. With the Duet CO
2
Module, the power source is derived from the +8.00 - +12.00 VDC
V
IN
power supplied by the host system.
The +8.00 VDC minimum requirement may be reduced if longer mainstream sensor warm up times are
acceptable or if only sidestream operation is intended.
A/D Converter
The 8 channel 12 bit serial A/D converter converts the following analog signals into a binary data
stream for the microprocessor: analog waveform from the optical bench, temperature of the optical
bench, barometric pressure, pneumatic flow rate (sidestream).
D/A Converter
The 12 bit serial interface D/A converter provides bench motor speed control, source current selection
and detector bias circuit control.
Source Hybrid
The optical benches require that the IR sources be current regulated. The current sensing circuitry is
located on a ceramic hybrid module, or source hybrid. A regulator is used that adjusts its output voltage
to maintain a constant current. The output of the regulator is then fed to a switch that can route the
output to either the mainstream or sidestream board.