System installation, Warning, 3 ossd output connections – Banner MMD-TA-11B Muting Modules User Manual
Page 35: 4 fsd interfacing connections
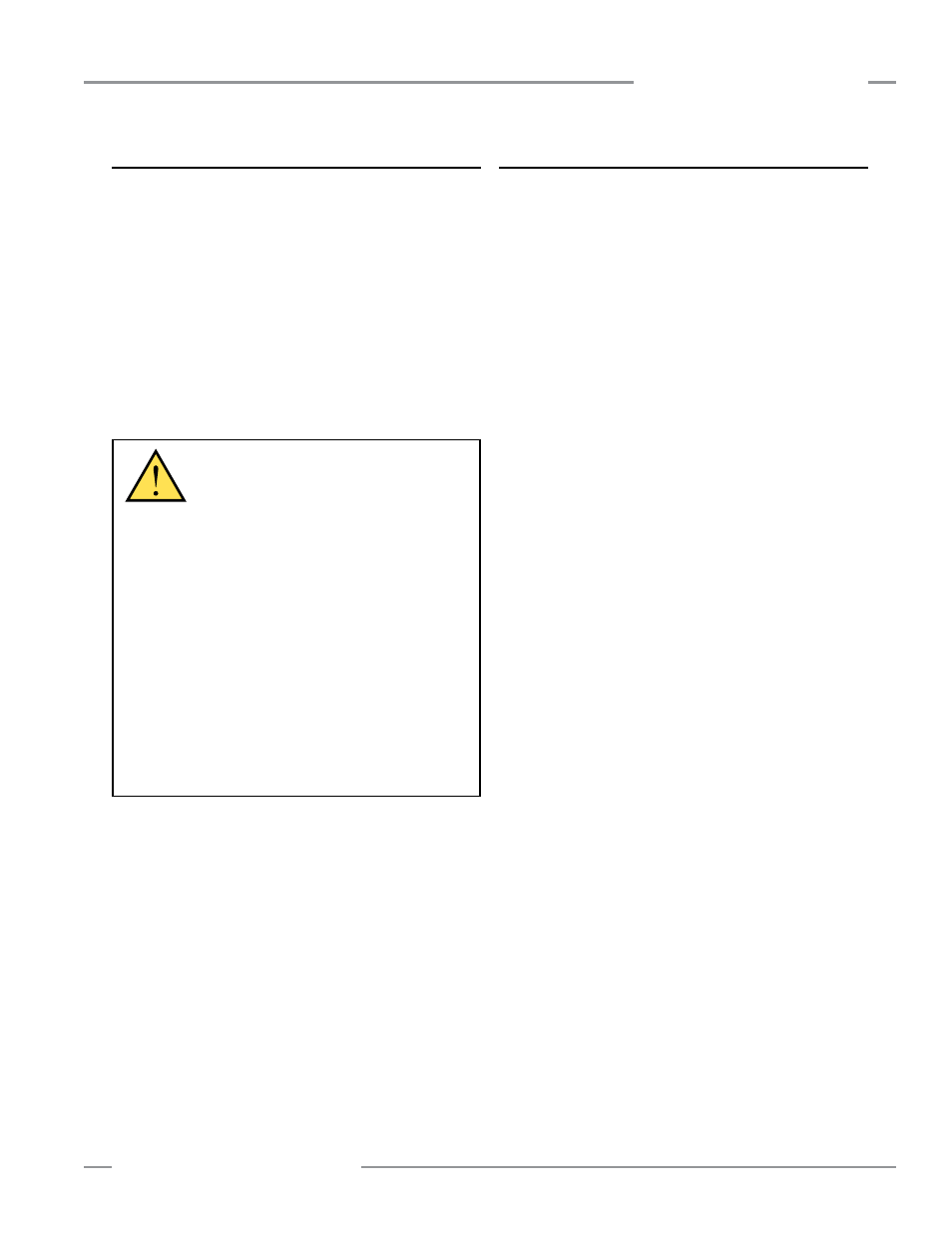
P/N 116390 rev. C
33
Banner Engineering Corp.
•
Minneapolis, U.S.A.
www.bannerengineering.com • Tel: 763.544.3164
MMD-TA-11B / MMD-TA-12B Muting Module
Instruction Manual
System Installation
WARNING . . .
OSSD Interfacing
To ensure proper operation, the Muting Module
output parameters and machine input parameters
must be considered when interfacing the Muting Module solid-
state OSSD outputs to the machine inputs.
Machine control circuitry must be designed so that:
• The maximum cable resistance value between the Muting
Module solid-state safety outputs and the machine inputs is
not exceeded,
• The Muting Module solid-state safety output maximum
OFF-state voltage does not result in an ON condition, and
• The Muting Module solid-state safety output maximum
leakage current, due to the loss of 0V, will not result in an
ON condition.
Failure to properly interface the OSSD outputs to the
guarded machine could result in serious bodily injury or
death.
3.7.3 OSSD Output Connections
Both the output signal switching device (OSSD) outputs must
be connected to the machine control such that the machine’s
safety related control system interrupts the circuit or power to the
machine primary control element(s) (MPCE), resulting in a non-
hazardous condition. This applies equally to the safety relays of
the model MMD-TA-11B and the solid-state output of the model
MMD-TA-12B.
Final switching devices (FSDs) typically accomplish this when
the OSSDs go to an OFF state. See Figure 3-24.
Refer to the output specifications (Section 2) and Warning below
before making OSSD connections and interfacing the Muting
Module to the machine.
3.7.4 FSD Interfacing Connections
Final switching devices (FSDs) can take many forms, though the
most common are forced-guided (mechanically linked) relays
or Interfacing Modules. The mechanical linkage between the
contacts allow the device to be monitored by the external device
monitoring circuit for certain failures.
Dependent on the application, the use of FSDs can facilitate
controlling voltage and current that differs from the OSSD
outputs of the Module. FSDs can also be used to control an
additional number of hazards by creating multiple safety stop
circuits.
Safety (Protective) Stop Circuits
A safety stop allows for an orderly cessation of motion or
hazardous situation for safeguarding purposes, which results
in a stop of motion and removal of power from the MPCEs
(assuming this does not create additional hazards). A safety stop
circuit typically comprises of a minimum of two normally open
contacts from forced-guided (mechanically linked) relays, which
are monitored to detect certain failures such that the loss of the
safety function does not occur (i.e. external device monitoring).
Such a circuit can be described as a “safe switching point.”
Typically, safety stop circuits are either single channel (a series
connection of at least two N.O. contacts); or dual channel (a
parallel connection of two N.O. contacts). In either method, the
safety function relies on the use of redundant contacts to control
a single hazard, so that if one contact fails ON, the second
contact will arrest the hazard and prevent the next cycle from
occurring.
Interfacing safety stop circuits must be wired so that the safety
function can not be suspended, overridden, or defeated, unless
accomplished in a manner at the same or greater degree of
safety as the machine’s safety-related control system that
includes the Module.
The normally open outputs from an IM-T-9A or -11A interfacing
module are a series connection of redundant contacts that form
safety stop circuits and can be used in either single-channel or
dual-channel control methods. (See Figures 3-25 and 3-26.)