1 resolver feedback precautions, 2 resolver calibration – Rockwell Automation SA3100 Power Module Interface (PMI) Regulator User Manual
Page 39
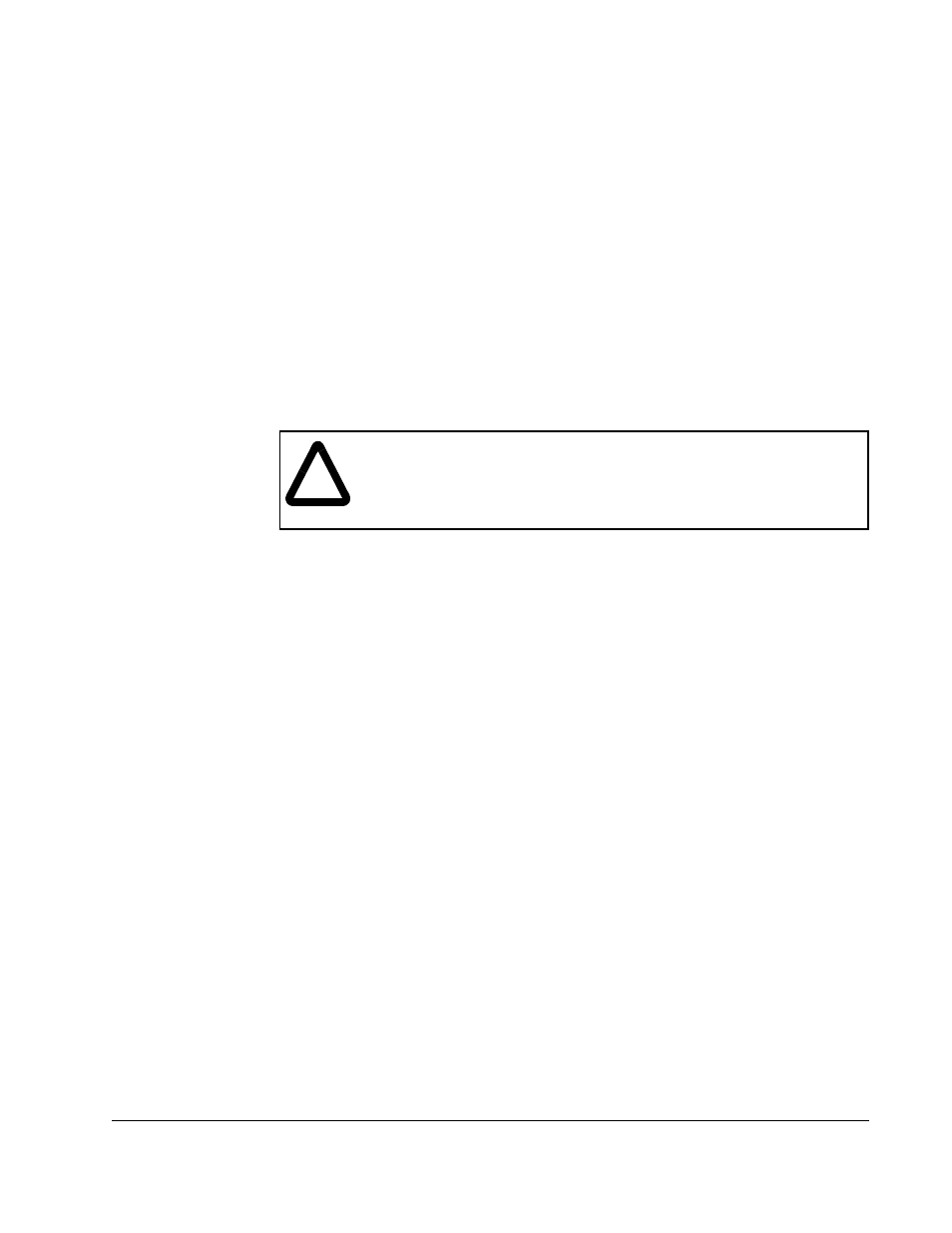
Resolver & Drive I/O Board
3-5
Strobe input detection is enabled by setting bits 8 and/or 9 in UDC register 101/1101.
The resolver position can be sampled on the strobe input’s rising edge, falling edge, or
both. Latched data is sent to the UDC module immediately before it is needed by the
UDC module for the next UDC task scan. Note that the PMI operating system detects
only one edge per UDC scan. If you choose to have the resolver position sampled on
both edges of the strobe’s input, the leading edge will be detected in one scan and the
falling edge in the next scan. Position data measured using this method is placed in
UDC register 216/1216 in the format shown in either figure 3.3 or 3.4.
Bit 8 of UDC register 201/1201 is set to indicate that the strobe signal has been
detected. This bit is set for only one scan to allow a strobe to be detected every scan.
The UDC task must check this bit each scan to ensure the validity of the strobe data in
register 216/1216. Bit 9 of register 201/1201 is set or cleared when the external
strobe is detected and indicates whether the strobe level was rising (1) or falling (0).
Both methods of sampling resolver position (i.e., time-driven and event-driven) may
be used simultaneously.
3.2.1.1 Resolver Feedback Precautions
The user must determine the maximum safe operating speed for the motor, connected
machinery, and material being processed. Then the user must either verify that the
system is incapable of reaching that speed, or ensure that the correct overspeed
parameter value has been entered during configuration.
Loss of Resolver Feedback
If resolver feedback is lost, induction motors will rotate close to their slip frequency.
But because the PMI Regulator is receiving no speed feedback, it will continue to
provide current to the motor, which will not appear to be responding. It is
recommended that the programmer use the THERMAL OVERLOAD control block in
the UDC task to provide additional protection against overheating of the motor that
can result from loss of resolver feedback. This block can also protect against
overheating of the Inverter’s Power Module due to sudden increases in current. Refer
to the Control Block Language instruction manual, J-3676, for more information.
Resolver Restrictions
The Resolver & Drive I/O board cannot discriminate between X1, X2, and X5
resolvers. It only detects electrical rotations. One mechanical rotation is equivalent to
one electrical rotation for an X1 resolver, two electrical rotations for an X2 resolver,
and five electrical rotations for an X5 resolver. The practical limit of electrical speed
that the board can detect is dependent both upon the resolver selected and upon the
resolution selected during drive parameter configuration. See Appendix B.
3.2.1.2 Resolver Calibration
The resolver input can be used with X1, X2, and X5 resolvers with cable distances as
shown in chapter 8 chapter 5 of this manual without having to externally tune the
cable. Cable recommendations are given in
chapter 5.
!
ATTENTION:The user is responsible for ensuring that driven machinery,
all drive train mechanisms, and the material in the machine are capable
of safe operation at maximum speeds. Failure to observe these
precautions could result in bodily injury and in damage to, or destruction
of, the equipment.