1 pmi processor operation – Rockwell Automation SA3100 Power Module Interface (PMI) Regulator User Manual
Page 24
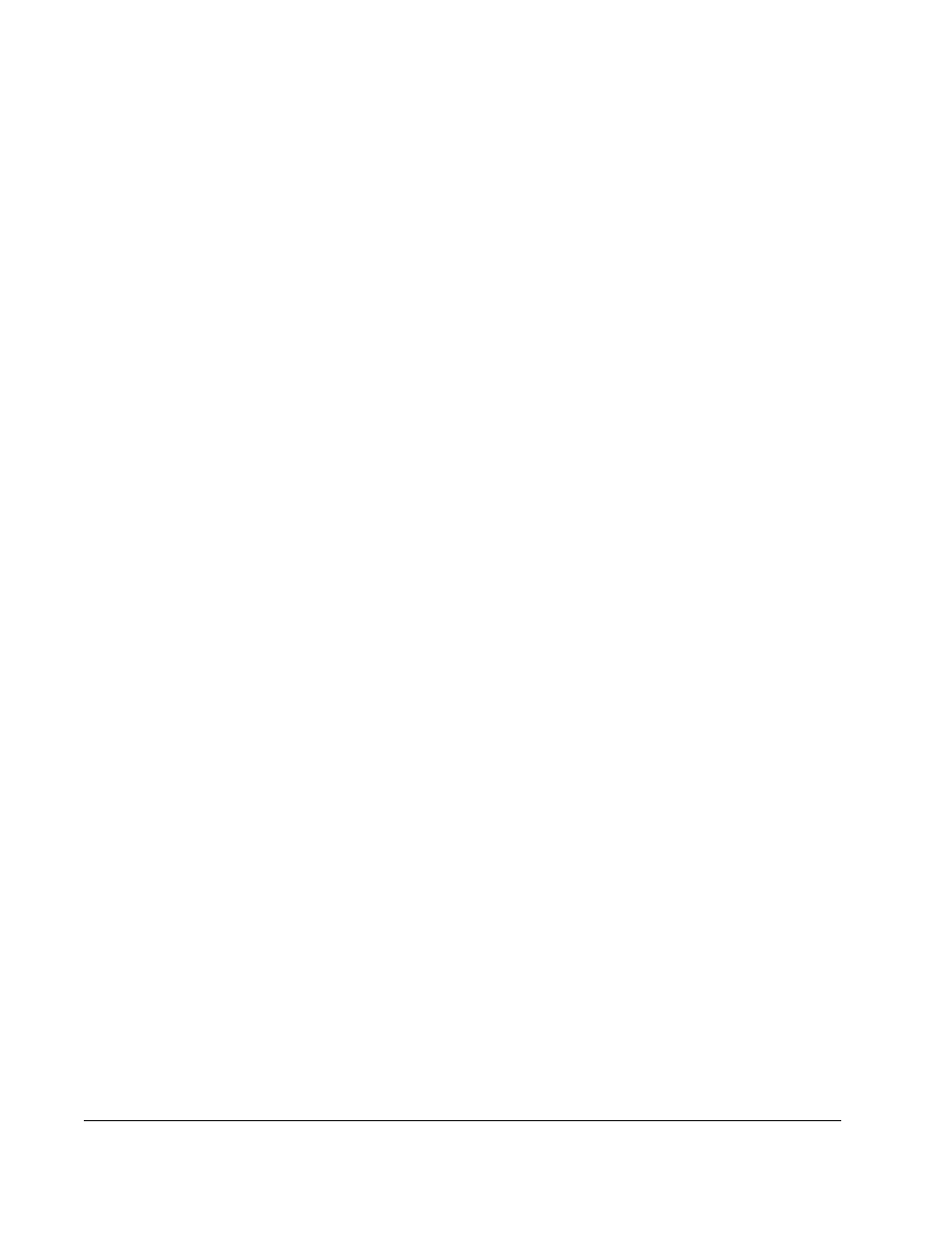
2-8
PMI Regulator
If any of these diagnostics fails, the DRV RDY LED will not turn on. If the diagnostics
pass, the PMI processor will send a feedback message to the UDC module. The UDC
module will respond with a command message and the configuration data. The
configuration data contains the synchronization information for the PMI Regulator.
The UDC module and the PMI processor are both synchronized to the system CCLK
signal so that a feedback message from the PMI processor arrives at the UDC module
just before it begins scanning the UDC tasks. The PMI Regulator provides resolver-
to-digital conversion for speed and position feedback. This data is sent to the UDC
module for use in the UDC task. Speed feedback sampling in the PMI Regulator is
synchronized to within 1
µ
sec of the UDC task scan.
The PMI Regulator also provides connections to digital drive I/O as well as digital and
analog Flex I/O. The PMI processor scans the I/O ports while the control algorithm is
running. This permits the I/O data to be integrated into the control algorithm as
required.
The operating system in the PMI processor continuously performs diagnostic checks,
displays the results on the LEDs, and stores them in memory locations in the UDC
module.
If power to the PMI Regulator is lost, all data as well as the processor’s operating
system will be lost. The PMI Regulator continuously monitors its power supply. When
the voltages are at the required levels, the DRV RDY LED is on. If the PMI
Regulator’s 5V line falls below 4.75V, an on-board monitor circuit generates a local
power loss signal. This signal will remain on for a minimum of 40 msec regardless of
the state of the 5V line. When this occurs, the processor shuts down, and the PMI
Regulator enters a safe power down state. The local power loss signal will turn off 40
msec after the 5V line rises above 4.75V.
2.2.1 PMI Processor Operation
The PMI processor controls all communication within the PMI Regulator and executes
the motor control algorithm (see appendices C and D in S-3056). The processor
receives drive parameter data, command data, and gain values from the UDC and
sends the flux and torque current reference values to the AC power technology circuit.
The AC power technology circuit, in turn, performs the calculations required to
generate the pulse-width modulated signals that fire the gates in the Power Module.
The PMI processor also transmits I/O values, speed feedback data, and the results of
diagnostic tests over the fiber-optic link to the UDC module. In addition, a fixed set of
variables can be output to the four ports provided on the motherboard for metering.
The processor contains an on-board watchdog timer that is enabled when power is
applied to the PMI Regulator. After the processor has performed its internal
diagnostics, the watchdog timer will become idle until it is activated again by the
processor's operating system. Once re-activated, the on-board CPU must reset the
watchdog timer within a specified time or the PMI processor will shut down. The MCR
output on the Resolver & Drive I/O board will then be turned off under hardware
control within 0.5 seconds. Power must be cycled to reset the watchdog timer.
Figure 2.4 shows a block diagram of the PMI processor.