Rockwell Automation 1771-QDC, D17716.5.85(Passport) MNL. PLASTIC MOLDING MODULE User Manual
Page 146
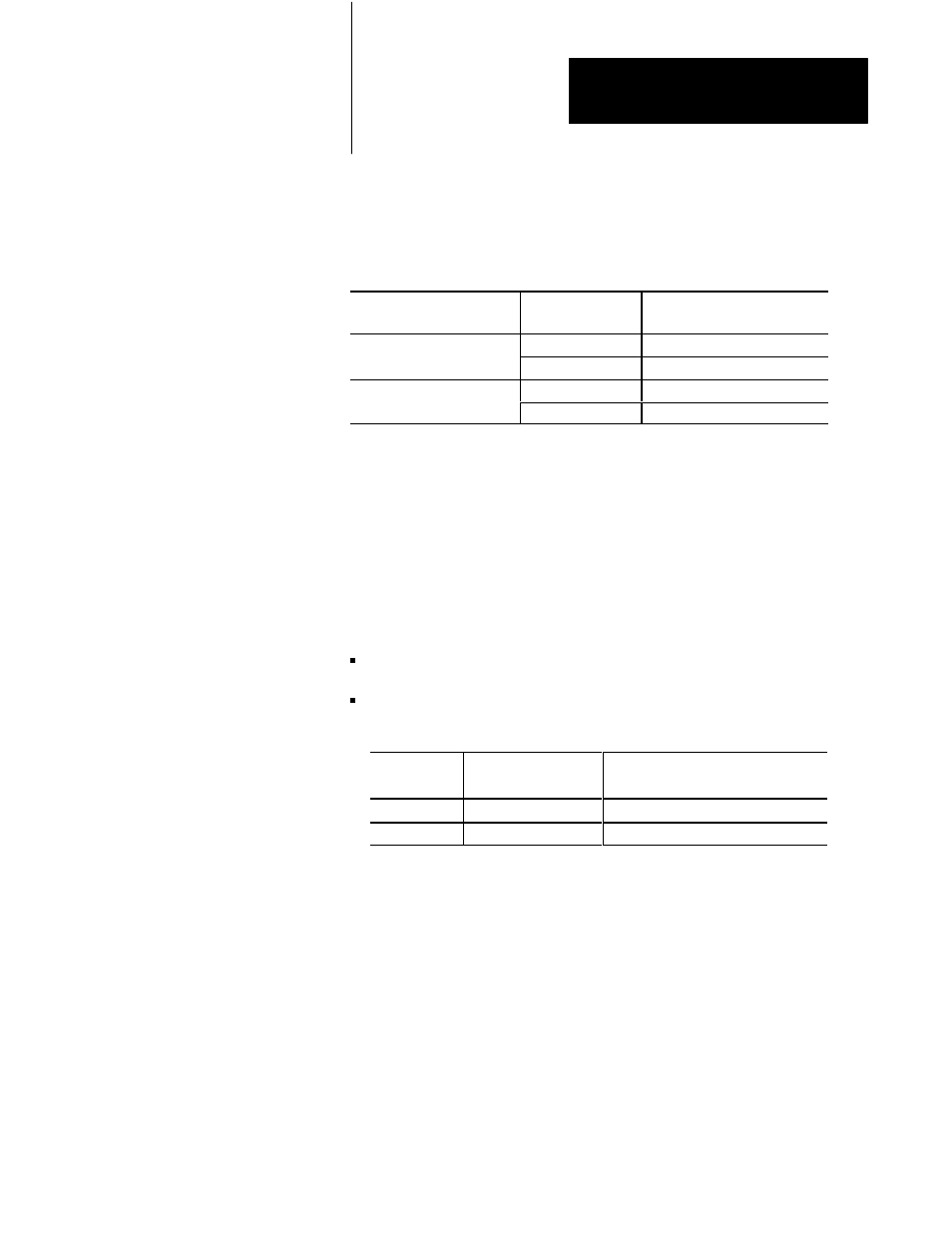
Span Your Valves
Chapter 9
9-29
4.
At completion of the profile, observe the RPM actuals reported for
the middle segments in PPS25, 29, and 33 (N44:729, 733, and 737).
If the observed RPMs are not within 20% of the setpoints entered in
PPC25, 29, and 33, then your RPM valve is not linear over the
desired range. Correct for a non-linear valve as follows:
If actuals are at least 20%:
And Your Selected
Valve is:
Then change PLC48 (N44:404)
as follows:
Less than setpoints
Direct Acting
Increase in 5% steps
Reverse Acting
Decrease in 5% steps
Greater than setpoints
Direct Acting
Decrease in 5% steps
Reverse Acting
Increase in 5% steps
To do this, change PLC48, download PLC followed by PPC with bits
B21/13 and 14, and repeat steps 3 and 4 as necessary.
Important: If downloading from your programming terminal, download
PLC followed by PPC with download bits B21/13 and 14 (chapter 4).
What You Have Accomplished
The open-loop tuning procedure you just completed has defined the:
range of screw RPM during plastication
end-of-range maximum and minimum signal levels for linear control of
the plastication RPM valve in open-loop control
For this
range limit
When trying to obtain
the RPM in:
The QDC module drives the selected
RPM valve to % output signal in:
Minimum
PLC45
PLC47
Maximum
PLC46
PLC48
Now, for all open-loop plastication RPM profiles, the QDC module
assumes a liner relationship between screw RPM and signal output.