Care and use manual – Waters Sugar-Pak I Column User Manual
Page 6
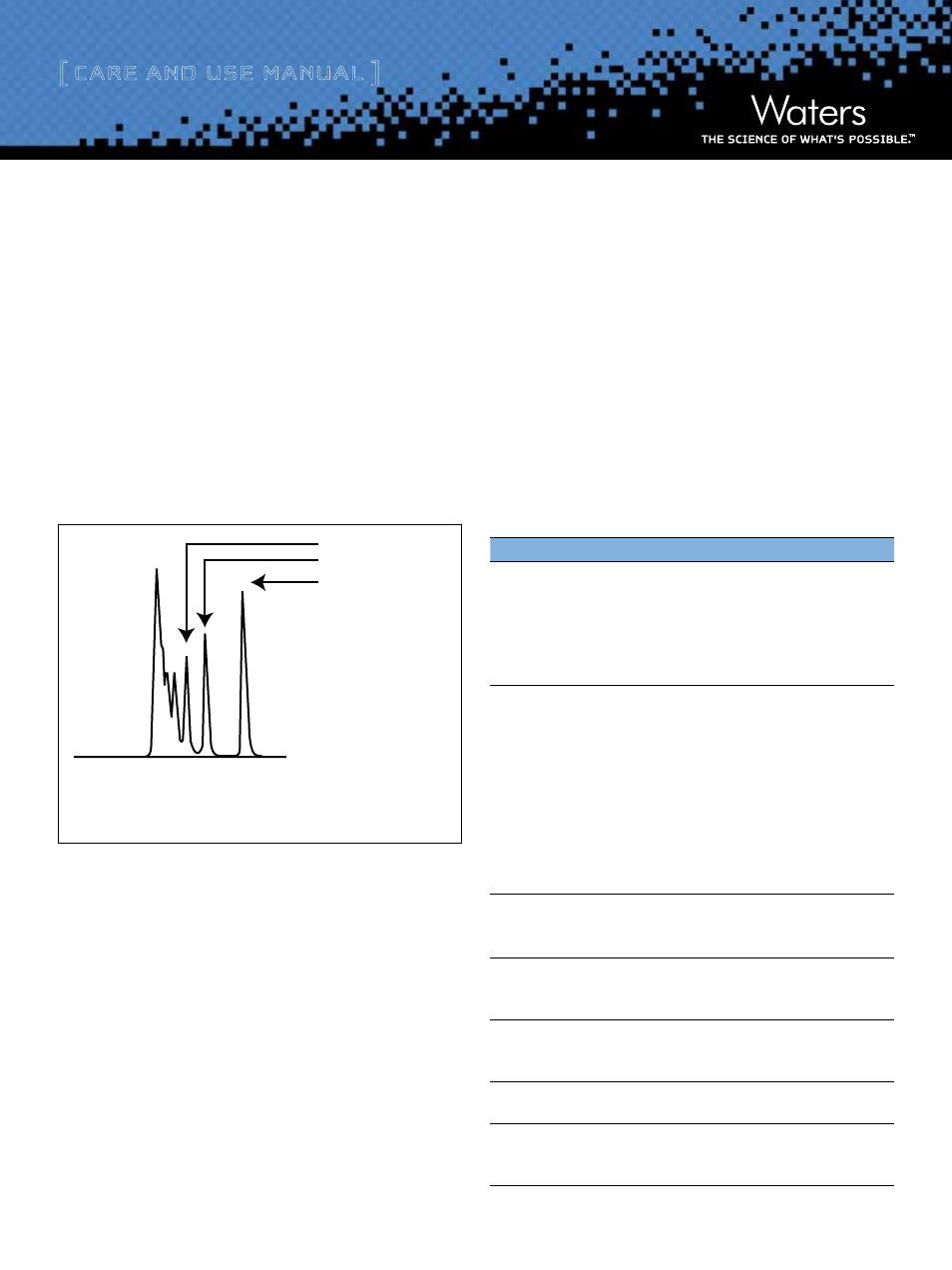
[ Care and Use ManUal ]
Sugar-Pak I Columns
6
When flow is reversed it is important to maintain solvent temperature
in order to ensure proper cleaning. Using cold solvent will slow the
cleaning process.
VI. test ConDItIons
Every column is thoroughly tested and passes strict manufacturing
specifications. It is recommended that you perform a test sample
injection, like the one below, prior to your first analysis. Record the
results along with all relevant instrument settings. These results
can then be used for comparison throughout the lifetime of the
column to monitor equipment performance, sample variation, and
column condition.
Figure 2: A typical chromatogram of sugar standards analyzed with a Sugar-Pak I Column.
Note the high resolution of glucose, maltose and maltotriose. Glucose should elute in less
than 10 minutes. Maximum backpressure should be less than 2000 psi.
VII. TROUBLESHOOTING
The Sugar-Pak I Column is tightly packed with a resin in a swollen
form. If good sample preparation is practiced, most problems that
arise will relate to the resin packing. The resin packing is delicate and
can be forced into the end frits of the column by pump pulsations due
to faulty check valves or by sudden or excessive pressure buildup.
Should pressure buildup occur, check for trapped particulates in the
in-line filter or guard column.
If this is not the problem, it is possible that the resin has partially
blocked the outlet frit. Should this occur, shut down the system.
Reverse the direction of flow through the column and begin pumping
the mobile phase at 0.1 mL/min. Allow 20 minutes after the column
has reached its working temperature before bringing the column up to
its working flow rate.
Refer to column regeneration and other cleanup methods explained in
this manual for actual procedures. Remember to switch your column
to its original flow direction and allow proper warm-up time before
continuing with further analyses.
Caution: The resin in Sugar-Pak I Columns is tightly packed and elastic.
If the column end frits are removed, the packing may expand out of the
column. Thus, opening the end fittings of the column to inspect or clean
the end frits (in an ultrasonic bath) should be done only as a last resort.
Table 1. Typical Column Problems and Solutions
Problem
Cause
Solution
Excess
pressure buildup
In-line filters
plugged with
particulates
Replace the in-line filter, or shut off the
pump. When inlet pressure has dropped to
zero, disconnect the in-line filter from the
column and backflush the prefilter ONLY
with mobile phase at 9 ml/min until the
particulates are backflushed out.
Fluctuating
backpressure
Column inlet
frit plugged with
particulates
Always use an in-line filter or guard
column to prevent this. Reverse column
to try to wash out particulates at normal
flow rate.
Exit frit plugged
with resin
Reverse flow of mobile phase. Check pump
and system operation before proceeding.
Gas in solvent
Check degassing procedure.
Faulty pump
operation
Inspect pump check valves and carry
out “Ramp Test” (consult the operator's
manual for your pump).
Peak “tailing”
on sucrose
H
+
ions or heavy
metals (e.g, Fe)
on column
Follow column regeneration procedure
using 500 mg calcium EDTA per liter as
described.
Band
broadening
Void in column
Reverse column flow direction. This may
allow the packing bed to reform, thus
improving peak shape.
“Spurious”
peaks, not
due to sugars
Elution of salts
and/or acids
Check sample cleanup procedures.
Leaking mobile
phase
Fittings in bad
state of repair
Tighten fittings properly. DO NOT
OVERTIGHTEN. Replace worn fittings.
Variable
elution times
Variations in
flow rate or
temperature
Check system for faults, leaks,
especially pulsations from pump.
4.22
5.80 DP3 Maltoriose
6.82 DP2 Maltose
9.80 Glucose
Test Sample:
Flow Rate:
Temp.:
Mobile Phase:
42 DE Corn Syrup
0.5 mL/min
90 ˚C
Deionized water