FUTEK VCal Sensor Verification User Manual
Page 42
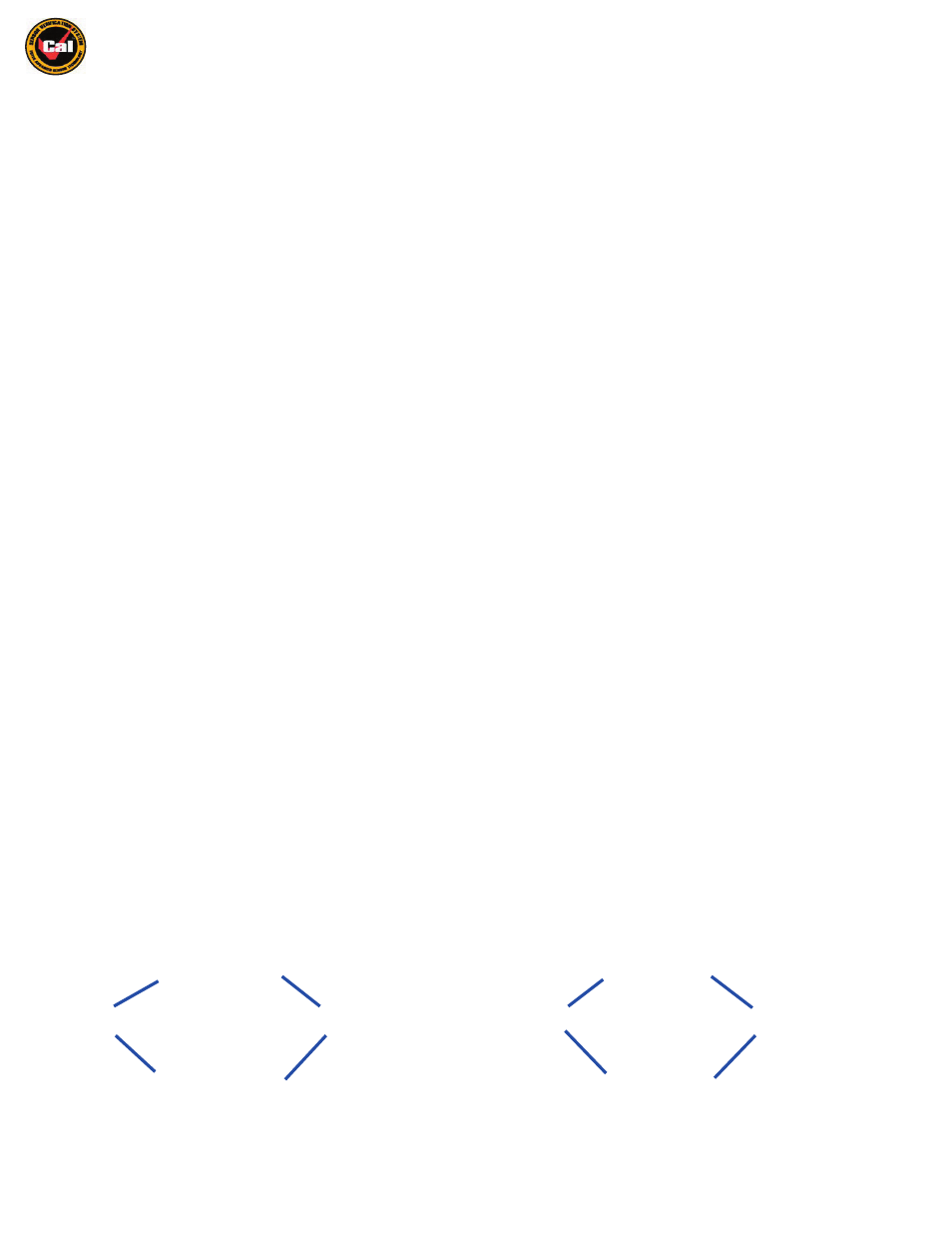
Futek Advanced Sensor Technology – Futek VCal™Documentation
Rev. 1.8.0
07/26/05
©Futek Advanced Sensor Technology 2005
42
Introduction To Performing A VCal™ Calibration / Verification
You are nearly ready to do some calibrating, however; before we step through some Calibration Examples, there are several items which require
some additional explanation. Testing Modes, Testing Options, Testing Parameters and Test Conditions are all items which really need
to be explained a little before we proceed. All of these can be found under the Setup tab. We will also talk some more about the three types of
testing you can do in the Calibration / Verification interface; the Main Test, the Time Test, and the Signature Test.
Testing Modes
Under the
Testing Modes
section of the Setup tab you have a choice of whether you wish to use Normal, Extrapolation, or Actual Modes,
when you perform your test. Let’s define what these calibration modes actually are.
Normal Mode Calibration: This is your default calibration mode. In this type of calibration you load your sensor to as close as possible to the
load points indicated in the Load column of the Test Grid window, pressing
Enter
at each load point. Each time you press
Enter
, VCal™ takes an
output reading and calculates the non-linearity (and hysteresis if selected), based on the deviation from the nominal or ideal value.
Extrapolation Mode Calibration: In this calibration mode you load your sensor to a point somewhat close to the indicated load point
(max+/-10% of load), and press
Enter
, and VCal™ takes a reading at the point you actually hit
Enter
at and extrapolates the output at the the
load value indicated in the Test Grid. It calculates the non-linearity (and hysteresis if selected) based on the deviation from the nominal. For
Example; If you pressed
Enter
at 79.3 lbs load, and your output was 0.5335 mV/V, but the load indicated in the Test Grid is 80 lbs, then; 80.0
lbs X (0.5335/79.3) = 0.5402 mV/V (this would be VCal™’s output reading in Extrapolation Mode under the test conditons described.
Note: Extrapapolation Mode only works when you have a calibrated reference cell connected as well as your test cell, and all
channels must be designated correctly for the calculations to work correctly.
Actual Mode Calibration: In this mode you take readings at any pattern of points you desire, pressing
Enter
at each point, and VCal™ takes
a reading at that point, and changes the indicated loads in the Test Grid to reflect the points at which you pressed
Enter
. VCal™ then gives
an output reading at that point, and calculates the non-linearity based on the deviation from the new nominal value. For Example; If the load
indicated on VCal™’s Test Grid is 80 lbs and you press
Enter
when there is only 79.3 lbs of load applied, then VCal™ will change the value
indicated in the Test Grid to 79.3 lbs and will display the output value that corresponds to 79.3 lbs of load.
Note: Because hysteresis requires exactly matching ascending as well as descending load points, it is not available in this mode of
calibration.
Testing Options
Manual Entry: Manual Entry allows you to enter data from a certificate or a different data acquisition system, through the keyboard, directly into
the Test Grid. The use of Manual Entry actually prevents the program from obtaining data from the VCal™ module. With Manual Entry you
can enter the Load and Output values from your test, and VCal™ will caluclate the non-linearity (and hysteresis if you selected it) as soon as
you press
Enter
in the final zero output box in the Test Grid.
Scaled testing: Scaled Testing is designed to be used when data is being entered from an outside source which has already been scaled to a
known unit, such as a pre-calibrated Sensor-Display system (Futek D500 series). If you are using a sensor that is giving you a raw output in Volts
or mV/V you cannot use Scaled Testing, because your scaling factor is unknown at this time. Using Scaled Testing changes the way in which errors
are calculated. Below are a couple of examples which illustrate the procedures used to calculate errors in both Scaled and Non-Scaled Testing:
Non-Scaled Example:
(Output in mV/V)
Scaled Testing:
(known output in lbs, kg, etc.)
0
0.0000
0
0.0
20
0.3995
20
19.8
LOAD
40
0.8000
OUTPUT
LOAD
40
39.9
OUTPUT
60
1.2000
60
60.0
80
.6000
80
79.7
100
2.0000
100
101.3
In this case the error is a percentage of full-scale, for example
the error at 20 lbs is ((0.4000 - 0.3995) / 2.0000) * 100
= 0.025% of full-scale. Note that 0.4000 is the ideal output
at a load of 20 lbs.
In this case the error is a percentage of load, for example; the error
at 20 lbs is ((20 - 19.8) / 20) * 100 = 1% of the Load.