Dead band, Power limiting and power scaling – Watlow Series SD31 PID with Optional Countdown Timer User Manual
Page 56
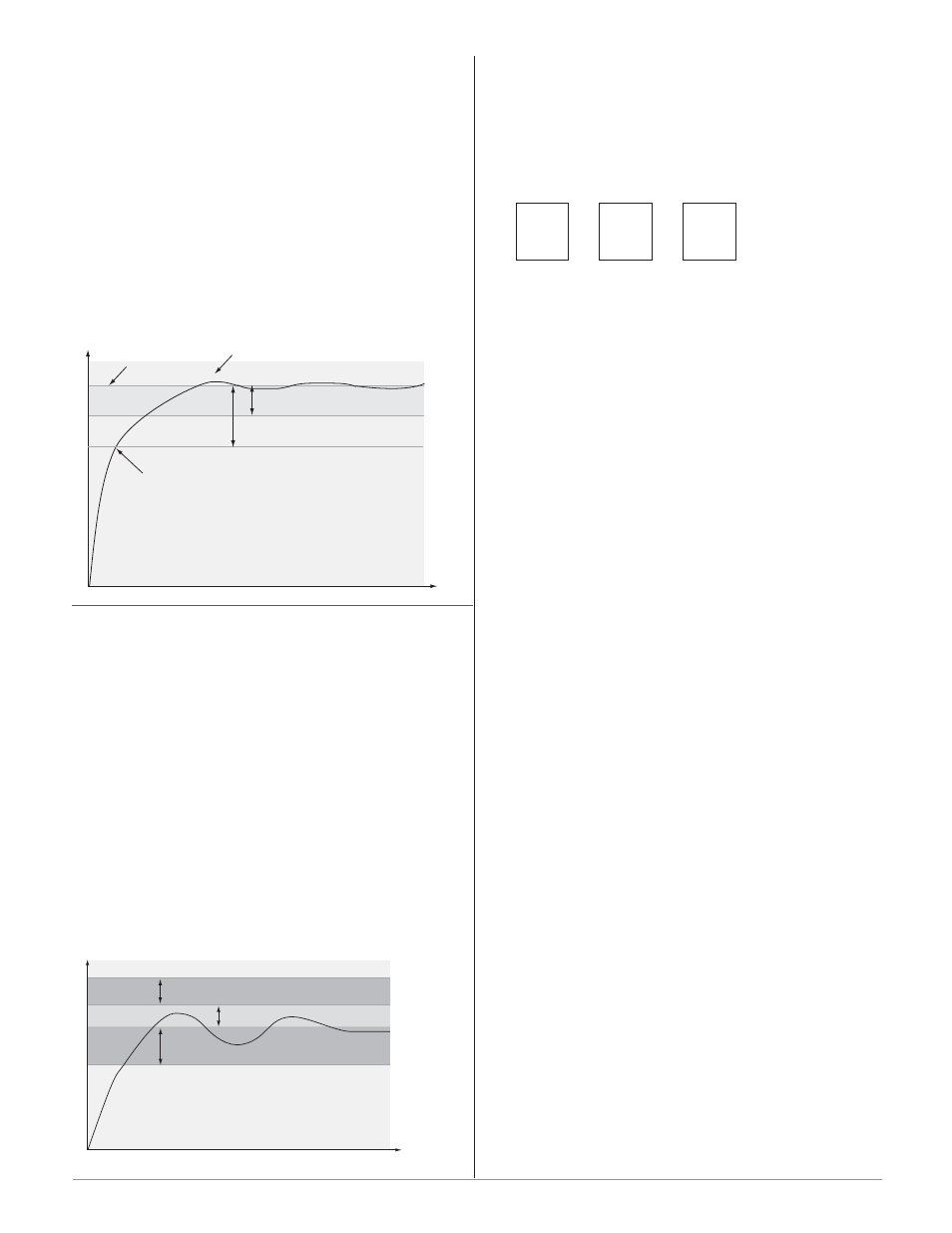
Proportional plus Integral plus Derivative
(PID) Control
Use derivative (rate) control to minimize the over-
shoot in a PI-controlled system. Derivative (rate) adjusts
the output based on the rate of change in the tempera-
ture or process value. Too much derivative (rate) will
make the system sluggish.
Rate action is active only when the process value is
within twice the proportional value from the set point.
Adjust the derivative with Derivative Heat
[dE;ht] or
Derivative Cool
[dE;Cl] (Operations parameters).
Adjust the rate with Rate Heat
[rA;ht] or Rate Cool
[rA;CL] (Operations parameters).
Dead Band
In a PID application the dead bands above and below
the set point can save an application's energy and wear
by maintaining process temperature within acceptable
ranges. Shifting the effective cooling set point and heat-
ing set point keeps the two systems from fighting each
other.
Proportional action ceases when the process value is
within the dead band. Integral action continues to bring
the process temperature to the set point. When the dead
band value is zero, the heating element activates when
the temperature drops below the set point, and the cool-
ing element switches on when the temperature exceeds
the set point.
Adjust the dead bands with Dead Band Heat
[db;ht]
and Dead Band Cool
[db;CL] (Operations
parameters).
Power limiting and power scaling
Power limiting and power scaling are two methods of
placing limitations on a control output. The functions can
be used independently or together. An output level calcu-
lated from the PID algorithm first has the power limit
applied, then the resulting value is processed using pow-
er scaling.
→
→
Using both power limiting and power scaling would
not usually be necessary. Power limiting provides a basic
static cap on power, while power scaling provides a more
dynamic range of power limitation.
Note:
When output power must be limited, in most cases power scaling will
provide better autotune performance than power limiting.
NOTE:
In on-off control set Power Limit 1 and 2 (
[PL`1] and [PL`2] ) and
Output Power Scale High 1 and 2 (
[PSH1] and [PSH2] ) to 100%.
Set Output Power Scale Low 1 and 2 (
[PSL1] and [PSL2] ) to 0%.
The power limit sets the maximum power for a heat
or cool control output. Each control output has its own
power limit. For heating outputs it determines the maxi-
mum level of heat power and for cool outputs it deter-
mines the maximum level of cooling power. A power limit
of 100% in effect disables the power limit. If the PID cal-
culations yield a power level that is greater than the
power limit setting, then the output power level will be
the power limit setting. For example, with a power limit
setting of 70%, a PID-calculated power output of 50%
would result in an actual output power level of 50%. But
if the PID calculated power output is 100%, then the
power level will be 70%.
Power scaling establishes the maximum power output
and the minimum power output. The output power is
then linearly scaled within that range. The default val-
ues of Output Power Scale Low of 0% and Output Power
Scale High of 100% in effect disable power scaling.
Linear scaling allows the controller to do calculations
over the full range of power (0 to 100%) and adjust that
calculation within the actual output span. For instance, if
scale low is set to 15% and scale high is set to 80%, the
output power will always be between 15 and 80%. If the
PID calculation is 100%, the output power will be 80%,
which is the same result you would get from a power
limit of 80%. However, if the PID calculation for heat is
50%, the output will be 50% of the allowable range,
which scales to an actual output of 47.5%.
Power limiting and power scaling affect the specified
output at all times, including in on-off control, manual
mode and during autotuning.
Output
Power
scaled
Output
power
capped at
Power
Limit
Output
power cal-
culated
using PID
Time
Temperature
Heating Set Point
Heating Proportional Band
Cooling Dead Band
Cooling Set Point
Cooling Proportional Band
Time
Temperature
Set Point
Reduced Overshoot
Proportional Band
Proportional Band x 2
Heating Slows
Wa t l o w S e r i e s S D 3 1
■
5 4
■
C h a p t e r 1 0 F e a t u r e s