Setting the home position – IAI America IF User Manual
Page 46
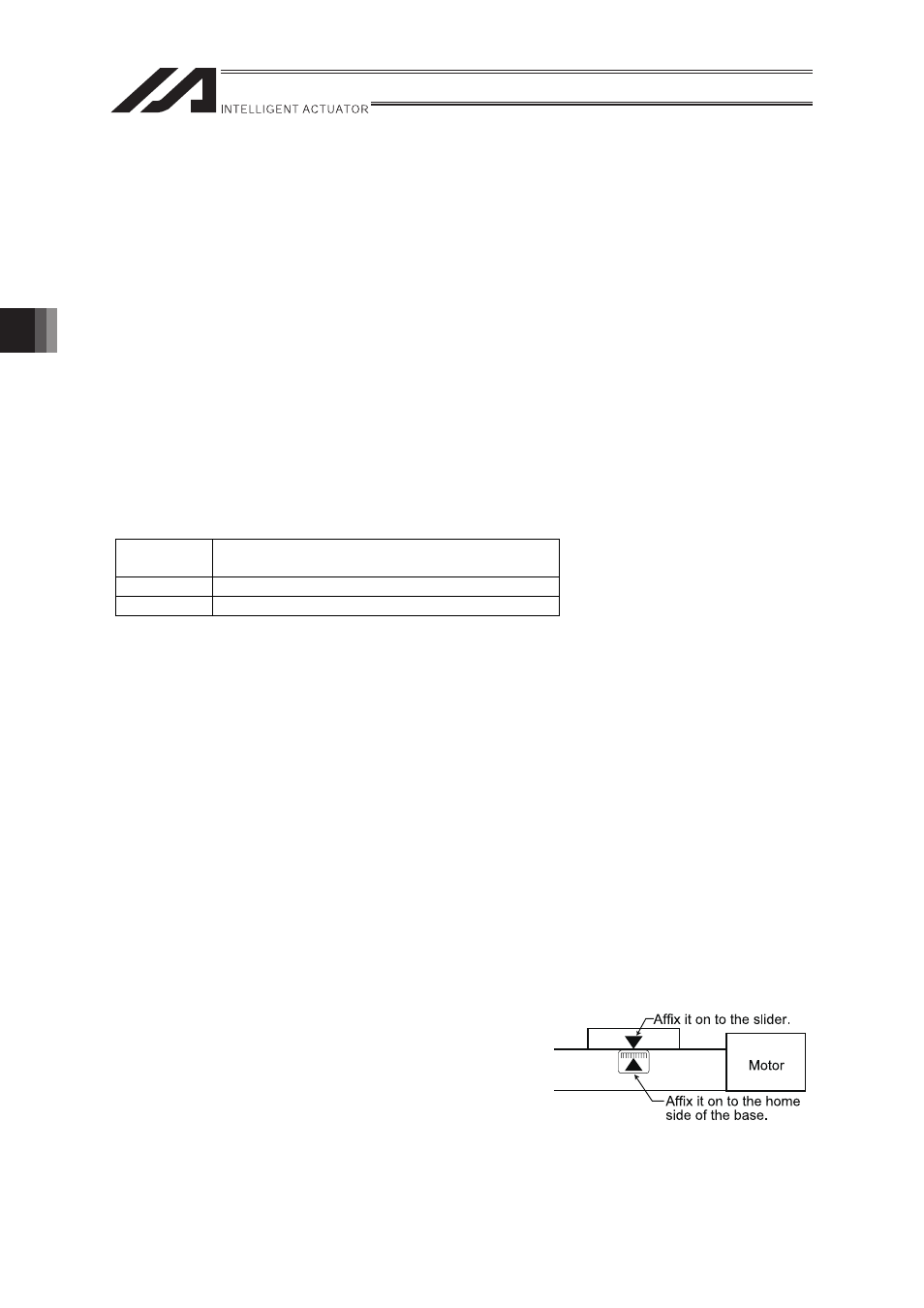
4. Setting the Home Position
40
4. Setting the Home Position
[1] The Principle of the Homing Operation
The Actuator performs homing in the following manner:
1) The moving direction is determined by the parameters set by the homing command.
2) It detects the mechanical end with the software in the home return operation.
3) The slider reverses direction when this end is reached and the place where the Z-phase
signal is detected becomes the reference point.
4) The slider travels further by an offset amount defined by the parameters and this position
becomes home.
[2] Fine Control of the Home Position
The number of motor revolutions from the time the slider hits the stopper to when the Z-phase
signal is generated is adjusted when the unit is shipped.
The standard value of the backing distance when the slider hits the stopper, reverses and then
stops at the home position is,
Model
Reverse distance from the mechanical end
[Approx. mm]
S Type
10
M Type
10
As long as the homing direction is the same, you can make fine adjustments to the home position
for each actuator by changing the parameters based on this value. Adjustments are made as
follows:
1) Initiate the homing operation and confirm home.
2) After that, move to the desired home position, check the difference and adjust the
parameters (For the E/G controller, any negative value is not acceptable).
3) If you allow for ample offset amount the movement range is that much more limited.
If the offset is greater than 1mm, you will have to reset the stroke soft limit.
[3] Changing the Home Direction
If you need to change the home direction after the unit is delivered, the move direction parameter
must be changed and you may need to adjust the encoder Z-phase so please contact IAI.
Also, the homing direction can not be changed by your company when it has the double slider.
[4] Alignment Marks Affixation
Make sure to affix the alignment marks on the slider and
base so that the home position can be confirmed.
It is necessary as the reference position when the positional
deviation is confirmed because of the timing belt tooth
missing or in the case of the motor change.