Brooks, Mf series – Brooks Instrument Mfi Series User Manual
Page 61
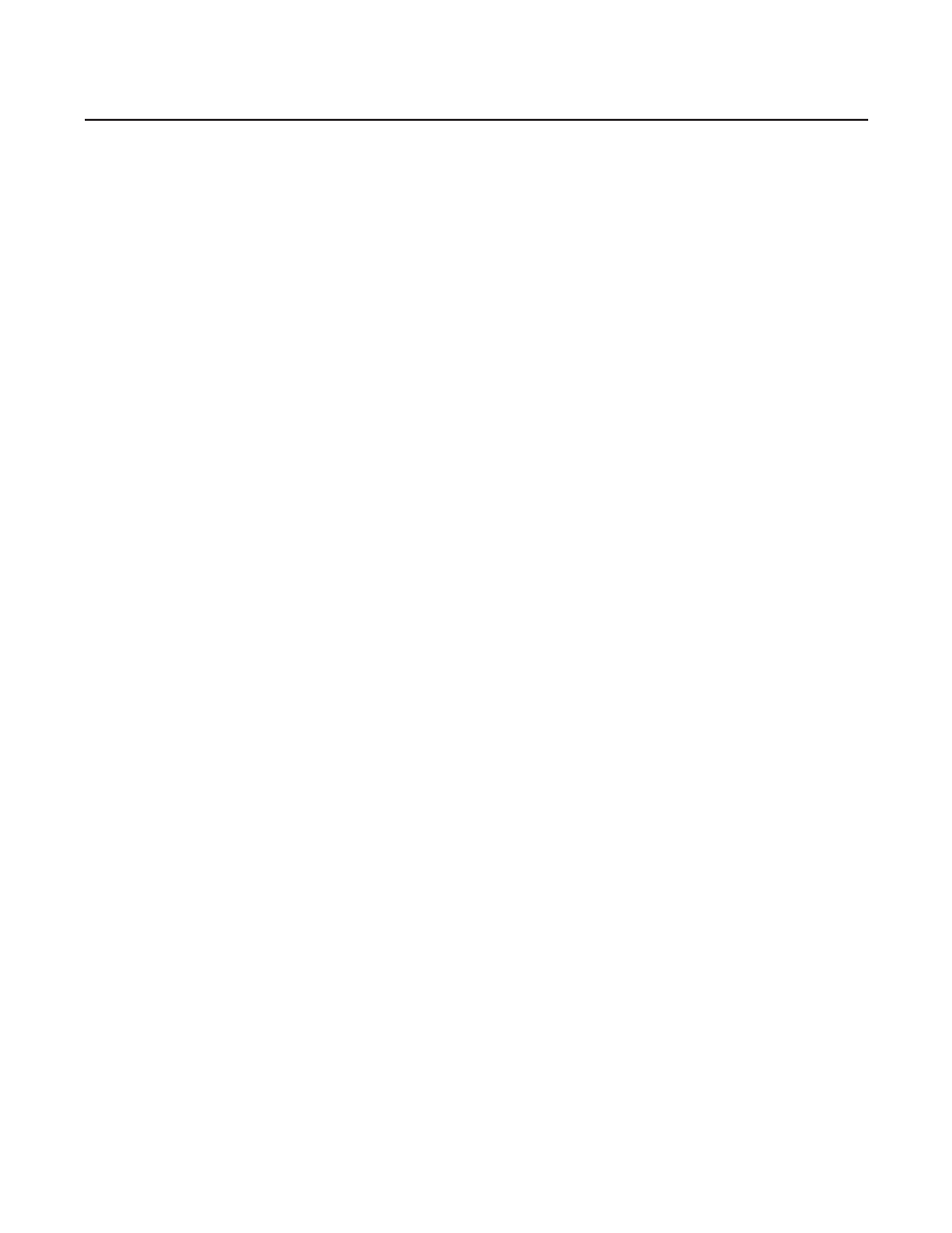
4-23
Brooks
®
Mf Series
Section 4 Maintenance &
Troubleshooting
Installation and Operation Manual
X-TMF-Mfi-Mfx-MFC-eng
Part Number: 541B074AAG
August, 2009
Restrictor assembly replacement should be performed only by trained
personnel. The tools required for the removal/replacement procedure are
as follows:
1. Appropriate size wrench for the removal of the inlet process connection.
2. Restrictor removal tool (contained service tool kit P/N S778D017AAA)
3. Restrictor O-ring, Refer to Section 5, Spare Parts, for the correct kit part
number.
Mf50/60 Restrictors
The model Mf51/Mf61 mass flow controller/meter utilizes porous metal
restrictor assemblies depending upon full scale flow rates.
1. Anti-Clog Laminar Flow Element (ACLFE). This type of restrictor
assembly is used for air equivalent flow rates less than 3.4 slpm.
2. Sintered wire mesh for air equivalent flow rates above 3.5 slpm. These
restrictor assemblies are made from a cylinder of sintered wire mesh and
are easily cleaned if they become contaminated in service.
Mf51/61 Restrictors
The model Mf51/Mf61 mass flow controller/meter utilies porous metal
restrictor assembliesfor all full scale flow rates. Restrictor elements eith
porosities of 40 and 60 microns are used in different combinations. Up to
three restrictor elements can be placed in one assembly. These restrictors
are assembled by pressing the porous metal elements into the header
plate, Figure 4-4.
If a restrictor assembly is being replaced because the original has become
contaminated, the original may be used as a guide to select the
replacement assembly. the porosity of the original element or elements is
marked on the calibration sheet which was shipped with the flow controller.
The replacement assembly should be replaced in the same orientation as
the original restrictor.
Mf53/63
Due to the complexity of the Mf53 restrictor assemblies it is recommended
that these assemblie be sized at the factory.
Assembly Procedures
1. Select the proper restrictor element combination.
2. When handling restrictor elements, use care to ensure they are not
contaminated with dirt, grease, oil, etc. The use of rubber gloves is
recommended.
3. Put a lightly lubricated O-ring on the header plate. The restrictor
assembly can then be installed in the mass flow controller body
(restrictor element(S) go in first). It is important that the restrictor
assembly is put into the body in the correct orientation (Refer to Figure
4-5). Push this assembly in with your fingers. Do not use an arbor press
or hammer to install the restrictor assembly. The restrictor assembly
should be pushed in until it bottoms out. Do not force it beyond this
point.
4. Place the end block O-ring in position and install end block with the four
hex socket screws. Tighten these screws to 30 inch/lbs. Do not
overtighten.