Brooks, Mf series – Brooks Instrument Mfi Series User Manual
Page 53
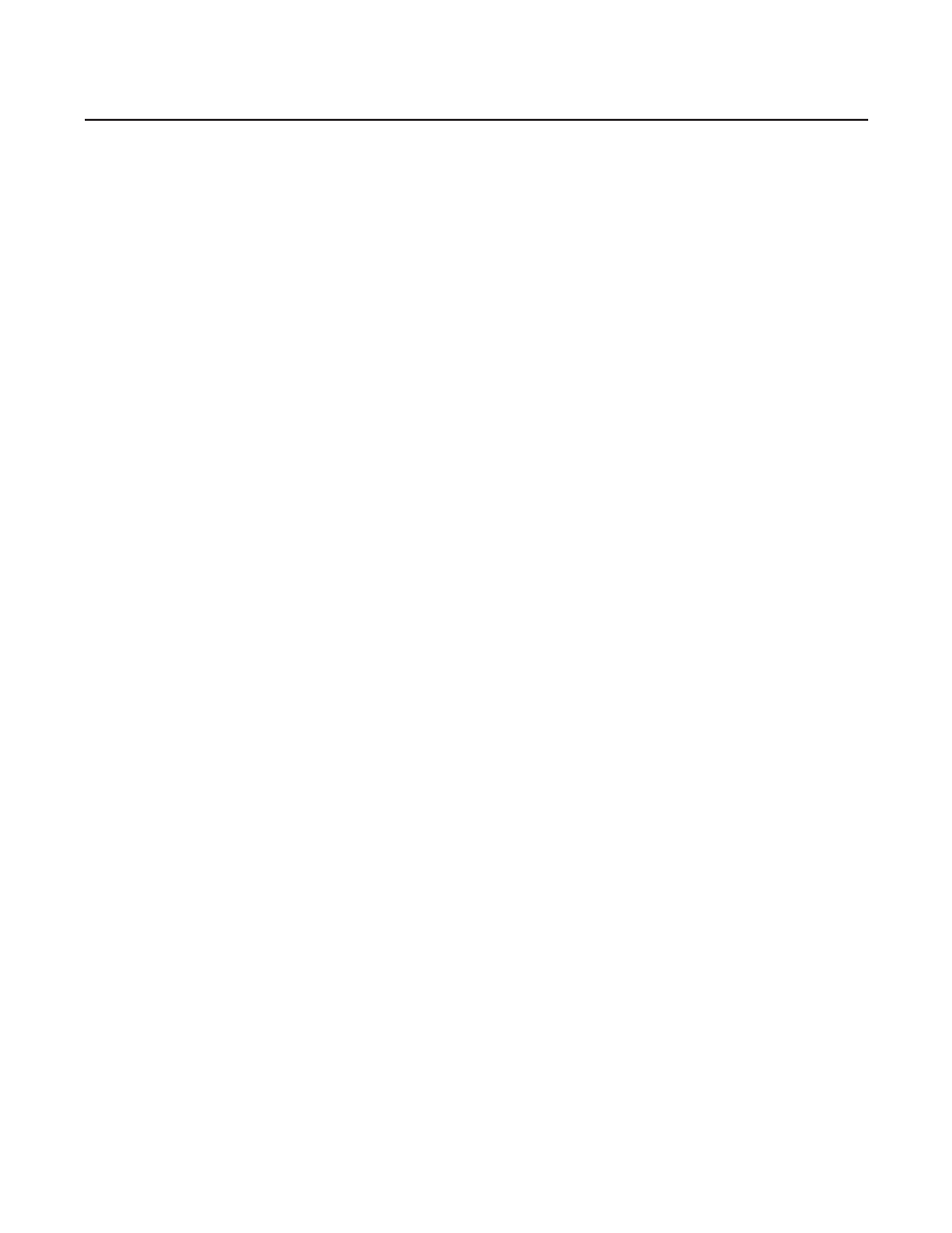
4-15
Brooks
®
Mf Series
Section 4 Maintenance &
Troubleshooting
Installation and Operation Manual
X-TMF-Mfi-Mfx-MFC-eng
Part Number: 541B074AAG
August, 2009
i. Measure the valve voltage by connecting a voltmeter between Test
Point 3 (TP3) and Test Point 4 (TP4). Refer to Figure 4-3.
j1. If the flow controller output signal is 100% and the valve voltage is less
than 11.5 V, the valve adjustment is complete.
j2. If the flow controller output signal is 100% and the valve voltage is
greater than 11.5 V, decrease the air gap with a small 0.005 inch air
gap spacer. Refer to Figure 4-2. Repeat Steps h and i.
j3. If the flow controller output signal is less than 100% and the valve
voltage is greater than 11.5 V, this condition indicates that the inlet
pressure is too small.
k. Refer to Section 3-4, Calibration Procedure, if required.
Normally Open Valve Adjustment (Refer to Figure 4-3b)
Flow clearance determines the position of the valve in respect to orifice
when valve coil is unpowered or under the valve override open condition.
If the flow clearance is insufficient, the resistance to flow between orifice
and valve seat will be great and full scale flow may not be able to obtain
If the flow clearance is to large, the valve will not be able to close fully and
will leak through excessively.
The air gap is the space between the top of insert and the bottom of
plunger. The air gap determines the force between the plunger and insert
at a given voltage and the total travel of the valve. If the air gap is too
small, the plunger travel may be insufficient to close the valve. In addition
the the control range of the valve decreases which may cause flow
instablity. If the air gap is too large, the magnetic force may not be able to
lower thr plunger and the valve may not close.
Adjustment Procedure (Normally Open Valve)
Note: This procedure applies to the Mf50 and Mf51. Adjustments to the
Mf53 should be done by the factory.
1. Install the flow controller in the test flow circuit.
2. Disconnect the valve connector from the customer terminal PC board.
Connect the valve (nonpolarized) to power supply. It is not necessary to
power the electronics.
3. Using clean dry Nitrogen, apply 10 psig to the controller inlet.
Note: the outlet of the controller must be kept below 10 inches of
watercoloumn (0.4psi).
4. Apply 0 volts to the valve and measure and record flow rate. The
measured flow rate must be greater than the flow given in Table 4-4 for the
respective orifice.