Brooks, Mf series – Brooks Instrument Mfi Series User Manual
Page 44
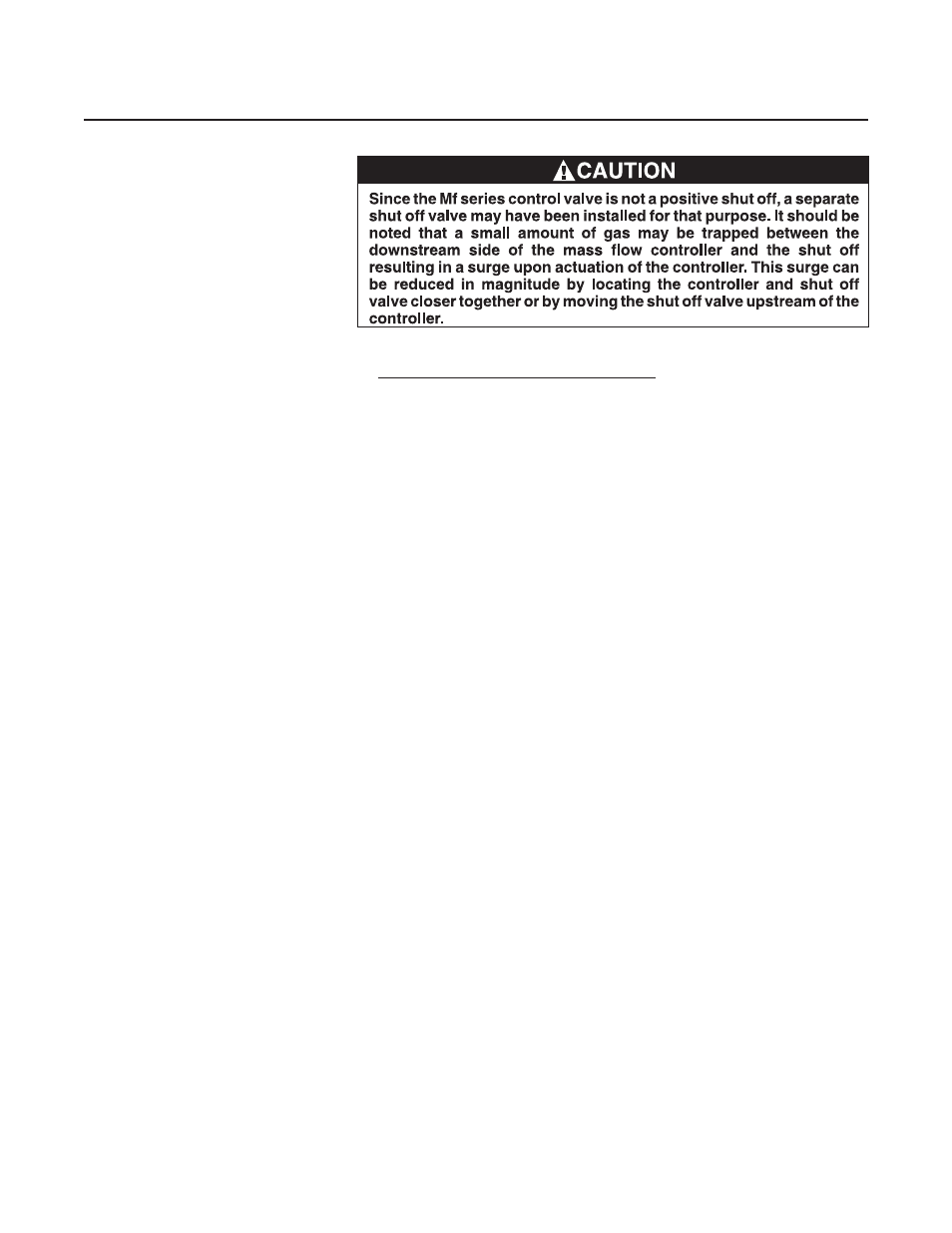
4-6
Brooks
®
Mf Series
Section 4 Maintenance &
Troubleshooting
Installation and Operation Manual
X-TMF-Mfi-Mfx-MFC-eng
Part Number: 541B074AAG
August, 2009
3. The Mfx Series sensor is not removable. The controller and meter
should be disassembled following the instructions in Section 4-4. The
sensor/body assembly can then be inspected for contamination and
purged with clean, dry Nitrogen. The remaining component parts may
be immersed in a deionized water bath using ultrasonic agitation to
enhance cleaning.
If it is determined the sensor is clogged, or the sensor/body assembly
can not be cleaned using compressed Nitrogen, all parts should be
returned to Brooks Instrument for service.
4. Use a hemostat or tweezers to push a 0.007" diameter piano wire
through the flow sensor tube to remove any contamination. For best
results, push the wire into the downstream opening of the sensor tube
(end closest to the control valve). The sensor tube can be flushed with
a non-residuous solvent (Freon TF
TM
recommended). A hypodermic
needle filled with solvent is a convenient means to accomplish this.
An alternate method for flushing out the sensor is to replace the
restrictor element with a low flow plug restrictor. This plug forces all the
flow through the sensor and may dislodge any obstructions. With the
valve orifice removed, subject the flow controller to a high differential
pressure. Pressurizing the outlet of the MFC higher than the inlet may
help force the obstruction upstream and out of the sensor tube.
5. Inspect the orifice for clogging by holding it in front of a light source and
looking for light through the bore. Clean by soaking in a suitable non-
residuous solvent and directing a stream of compressed dry nitrogen
through the bore.
6. Deposits of silicon dioxide may be removed by soaking the internal
parts in a solution of 5 parts hydrofluoric acid (HF) and 95 parts water
(H
2
O) followed by Freon TF.
7. Restrictor elements can be cleaned in an ultrasonic bath. Refer to
Section 4-5 for the correct restrictor to use.
8. Blow all parts dry with dry nitrogen and reassemble. Refer to Section
4-4B, assembly.
9. Purge the assembled instrument with dry nitrogen.
10.Perform the calibration procedure in Section 3-4.
11.When the instrument is reinstalled in the system, the connections
should be leak-tested and the system should be purged with dry
nitrogen for 30 minutes prior to start-up to prevent the formation of
deposits.