Kipp&Zonen BSRN Scientific Solar Monitoring System User Manual
Page 58
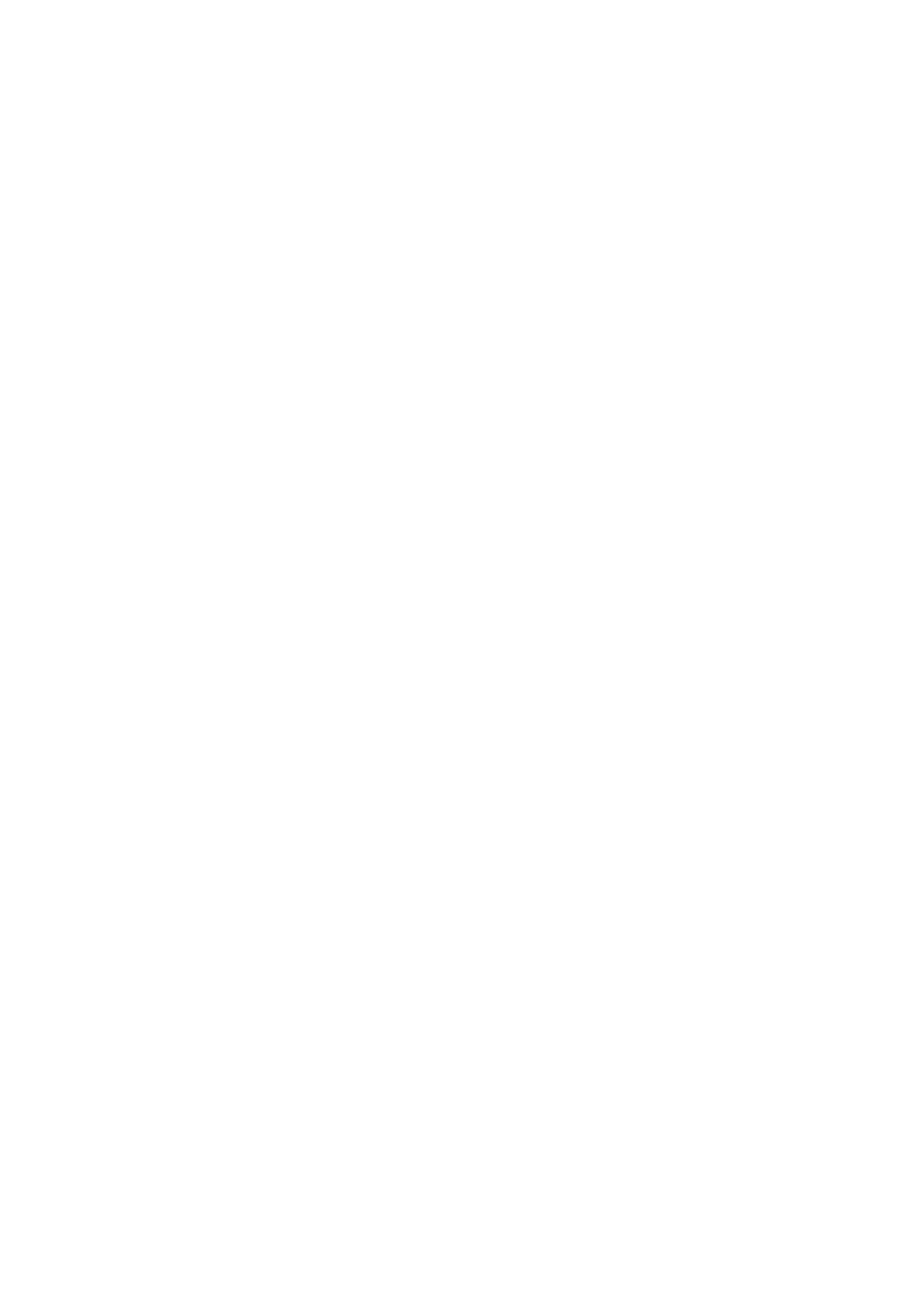
46
to a fault in the system by perform ing the sam e zero test with the resistor attached
directly to the input term inal of the unit. Servicing by authorized personnel is required
if the data acquisition unit fails. If the unit does require servicing it is also a good
opportunity to have the unit calibrated, a procedure that should be repeated every two
years. If the problem is not found in the data acquisition unit, it m ust be assum ed that
local conditions are causing electrical interference. The cabling should be rerouted
and the test repeated. Interference can be reduced by keeping signal cables away
from power cables. It is good practice to avoid parallel routing and to intersect all cables
at 90 degrees whenever possible.
(ii)
Measure the lead resistance. Short the resistor and m easure the resistance of the leads
as seen by the data acquisition system (a bridge circuit m ay have to be built for this
test depending upon the capabilities of the system ). The resistance should be less
than 10 ohm s. If the resistance is satisfactory, the resistor (and bridge) can be rem oved
from the circuit and the pyranom eter returned. If the value is excessive, determ ine if
this is a result of the length of the cabling. This can be accom plished by calculating
the overall resistance of the cable by either m easuring a short length of sim ilar cable
or obtaining the specification of resistance per unit length from the m anufacturer. Once
the unit length is obtained, an approxim ate value of the entire length can be calculated.
If the resistance can be attributed to the length of the cable one can account for the
com m ensurate loss in voltage when the m easurem ent is converted into engineering
units. If the resistance is greater than indicated by the length of the cable, it is caused
by a fault within the cable. This m ust then be repaired or replaced.
(iii)
Test the com plete system . Measure the resistance of the pyranom eter as installed
with the data acquisition system and check that it is approxim ately within the
m anufacturer's specification. This has to be done at night or with the dom e covered
unless the resistance m easurem ent is in the offset com pensation m ode in which case
it would be unaffected by the pyranom eter signal voltage.
(2)
Installation of constant signals
For greater assurance in the reliability of the data, channels should be set aside to be used
with known signals in the sam e range as those signals being m easured. For exam ple, on
a system where both resistance and voltages are being m easured, a fixed resistor and a
known voltage should be included as part of the sam pling sequence. These provide a m eans
of rapidly flagging any changes in the quality of the m easurem ents. Obviously, in a m ultiplexed
system , the potential exists for scanning problem s being m issed.
(3)
Instrum ent resistance checks
An easy m eans of determ ining a fault in cabling or a sensor which outputs a voltage is testing
for changes in the resistance. On programm able system s, it is encouraged to test the resistance
of each sensor on a daily basis to determ ine if any significant changes have occurred in the
overall resistance of each channel. W hile a trained operator m ay observe changes in a signal
associated with a broken wire or instrum ent, floating channels are not necessarily easy to
detect im m ediately if they are not well defined (e.g., pyrgeom eter voltages) or adjacent to
a channel with a sim ilar signal.
(4)
Program m able flagging
If the system is capable of autom atic data quality checks, it should be program m ed to set
flags when:
(i)
any irradiance values fall outside the range -10 -2 not be designed to delete any data autom atically. (ii) any air tem perature value (air, case, dom e, etc.) is outside the norm al clim atological
range of the station by greater than ± 10 °C. The program should not be designed to
delete any data autom atically.