Burnham Series 5B User Manual
Page 61
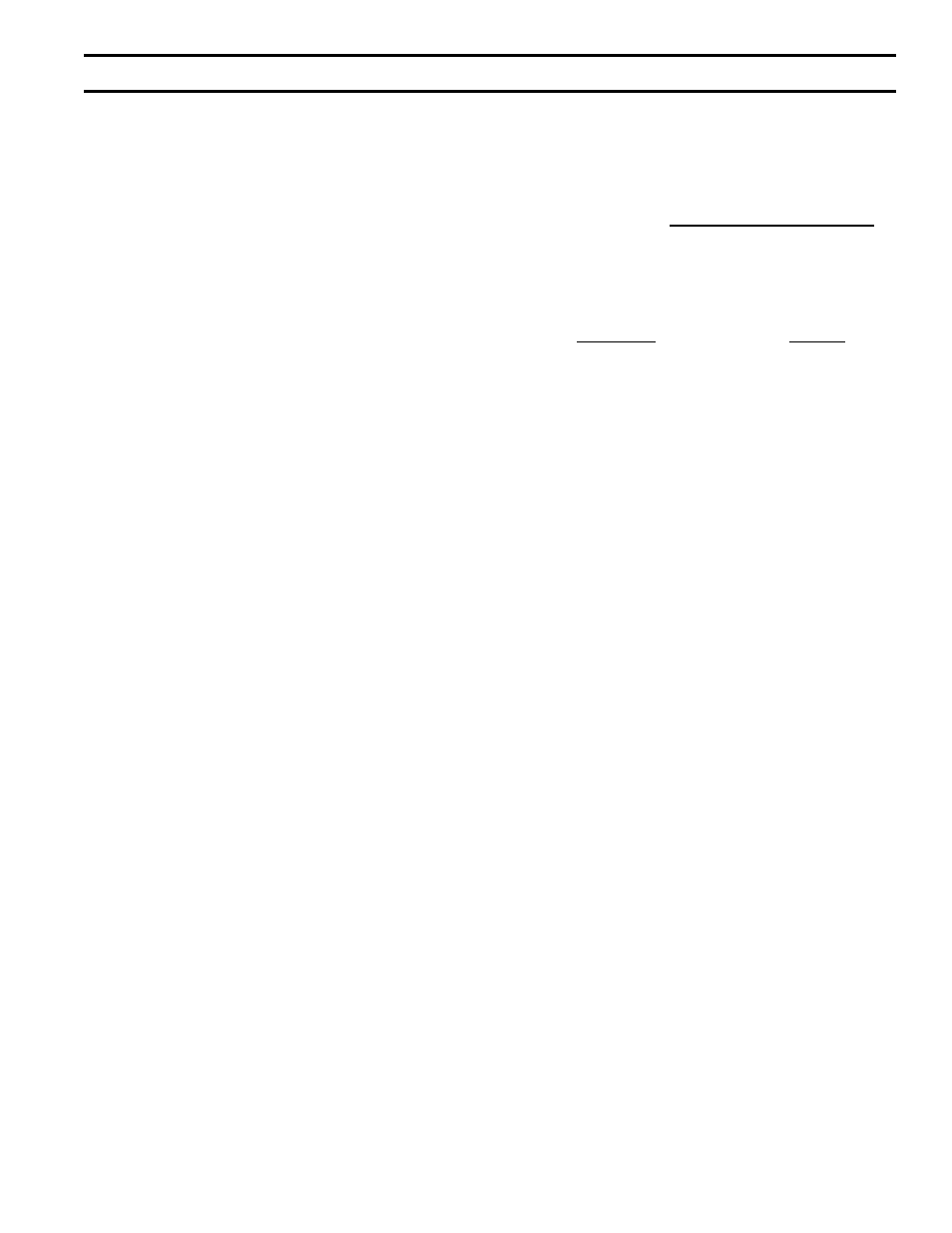
61
14.
CHECK GAS INPUT RATE TO BOILER
(1) Input Rate and Maximum Inlet Pressure shown on
Rating Plate must not be exceeded. Inlet pressure
must not be lower than minimum inlet pressure
shown on Rating Plate.
(2) All Rate checks and all adjustments are to be
made while boiler is firing – all other appliances
connected to the same meter as the boiler must be
off.
(3) Water Manometer or water column gauge should
be connected to a shut-off valve installed in the
1/8” pipe tapping in each manifold – boiler off. By
installing gas valve upstream of manometer, gas
pressure can be introduced gradually – without
shut-off valve, surge of pressure when boiler is
turned on, could blow liquid out of manometer.
(4) LP Gas Input
(a) Adjust Gas Train Regulator(s) so that manifold
pressure is ten (10) inches water column.
Turning Regulator Adjusting Screw Clockwise
increases pressure, Counterclockwise rotation
decreases pressure. If boiler is equipped with
two manifolds (5015B thru 5026B), pressure
in each must be equal.
(5) Natural Gas Input
(a) Approximate Input – Adjust Gas Train
Regulator(s) so that manifold pressure is three
and a half (3½) inches from water column.
Turning Regulator Adjusting Screw Clockwise
increases pressure, Counterclockwise rotation
decreases pressure. If boiler is equipped with
two manifolds, pressure in each must be equal.
If more accurate check on input is necessary,
see (b) below.
For minor input changes readjust Gas Train
Regulator(s) to increase or decrease manifold
pressure to obtain corresponding increase or
decrease in gas input. If it is necessary to
increase manifold pressure more than 0.3” of
water to obtain rated input, remove orifices
and drill one size larger. Reinstall and recheck
input rate.
(b) Additional Check on Input – Since input is
a function of heating value, specific gravity
and volume of gas flow contact your utility
for the first two items in order to utilize the
formula below. The gas meter should then be
clocked for three (3) minutes with stop watch
and substituting the appropriate values in the
formula below, determine what the gas flow
should be in this 3 minute period to give the
input shown on the Rating Plate:
(c) ADJUST AIR SHUTTERS – See Section V
Burners are normally shipped with the air
shutters in the wide open position. Loosen air
shutter securing screws and close air shutters
until yellow tips appear on flames, then open
shutters slowly until defined inner cones may
be seen. Lock shutters in this position.
(d) ADJUST BLEED LINE REGULATOR
(V88A’s)
All gas boilers for the USA and Canada are
normally equipped with two diaphragm gas
valves per manifold. The gas valve(s) nearest
the manifold on all boilers, is equipped with an
adjustable bleed. This bleed regulator should
be adjusted so that the burners reach full fire
in approximately 10-12 seconds after the main
gas valves have been energized.
(e) ADJUST PILOT LINE PRESSURE – See
Section V - Service; 7. Pilot Flame
Shut down boiler and remove gas valve and
manometer from 1/8” pipe tapping in each
manifold. Plug tappings with square head pipe
plugs. Install gas valve in tee in each pilot line.
Connect manometer to each gas valve and, with
boiler in operation, set pilot line pressure at
5.5” water – natural gas boilers and 6.5” water
– propane gas boilers.
Shut boiler down, remove gas valves and
manometers and plug tees with square head
pipe plugs. Restart boiler.
cu. ft. per =
3 min.
Btuh Input
Heating x 20 x multiplier
Value
of gas
(from
table
below)
(Btu/cu.ft.)
spec. gravity
multiplier
.50
1.10
.55
1.04
.60
1.00
.65
0.96
.70
0.93
SecTiON iV - OPeRATiON (continued)