AW Gear Meters EMO-3000 User Manual
Page 8
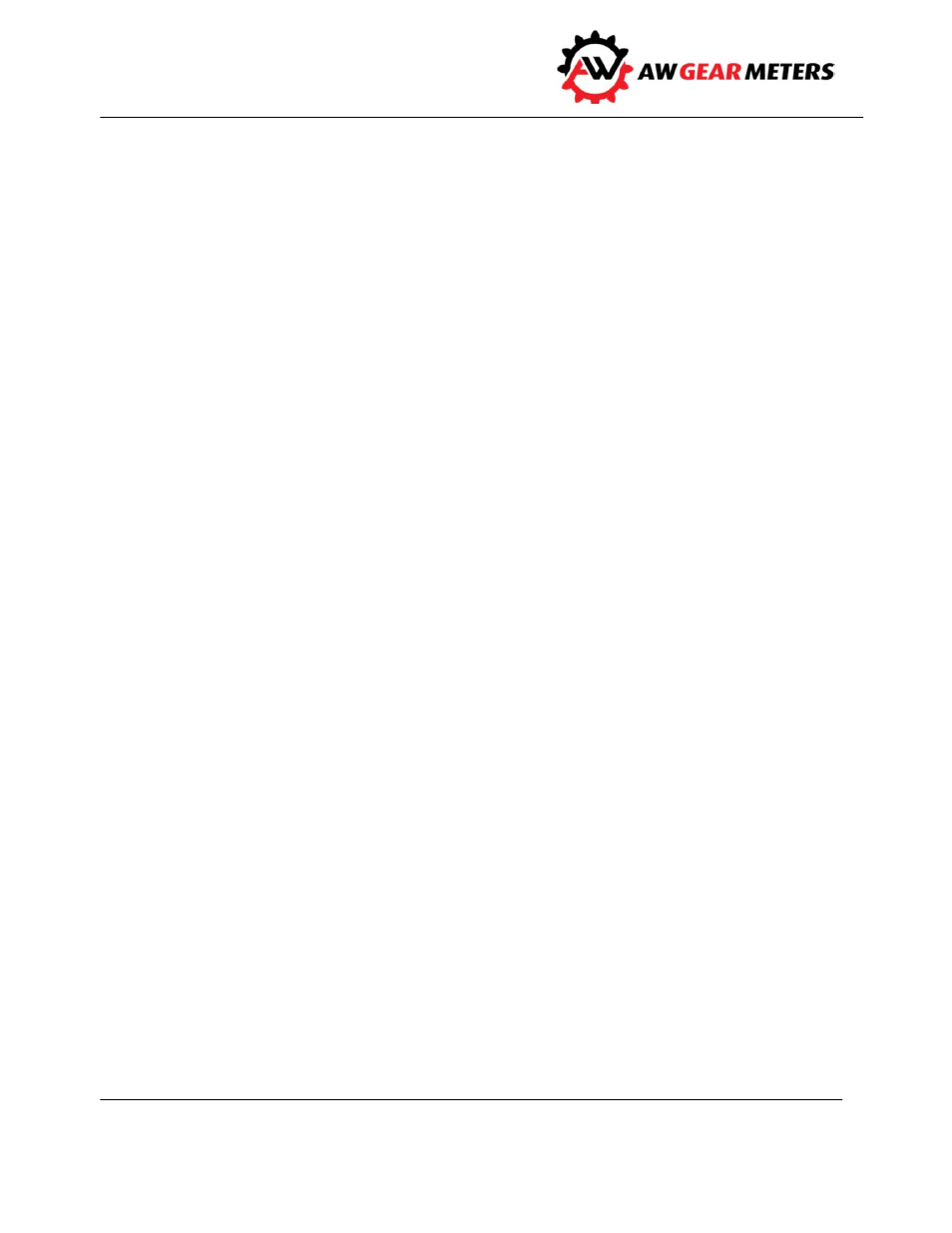
EMO‐3000
Operation and Programming Manual
7
Principle of Operation (Example: Paint Application)
A PLC transmits
flow instructions to
the EMO‐3000. The EMO‐3000 then uses an I/P converter and
pneumatic pressure to control the fluid regulator. The meter measures the flow to the paint nozzle. The
EMO‐3000 compares this value to the set‐value and makes any adjustments required.
The device’s internal memory retains flow values from earlier cycles and continuously modifies them as
new conditions occur. The EMO‐3000 builds adaptive data tables for up to 30 fluids or colors, ensuring a
fast, highly precise response for a wide variety of fluids and conditions.
Hardware
The EMO‐3000’s power supply and channel cards neatly integrate into a durable, efficient, and
convenient anodized‐aluminum housing compatible with EURO module plug‐in types. The unit is
expandable to a maximum of 12 channels, in 4‐channel increments. Each interlocking section has its
own independent power supply.
The EMO‐3000’s power supply uses plug‐in type fuse holders, which allow for easy replacement without
having to remove the entire power supply card. Three LEDs indicate whether the AC, positive, and
negative legs are supplying the channel cards (refer to Appendix I). An anodized aluminum strip secures
the cards to the housing. On one end of this strip, the screw terminal slot secures the card in place. At
the other end, a 90‐degree bend helps with removal or insertion of the card. The watchdog chip
monitors the microprocessor activity and issues a reset after a 1.6 second delay. Each channel card also
has a red LED that blinks when the microprocessor is running, and blinks faster when a frequency input
is applied to the channel.
EMO‐3000 units manufactured after July, 1993 have RS‐232 and 4‐wire RS‐485 serial communication
protocol. The RS‐485 serial communication is backward compatible to the previously used 4‐wire RS‐
422. As an option, these communications ports can be optically insulated from the rest of the EMO‐
3000. The RS‐232 to the (optional) DM‐3000 display is not optically insulated.
Features
Standard unit will hold four channels, expandable to 12 channels
Program each channel as a flow monitor or as a closed loop controller
Program four alarm limits for each channel to indicate rate, total, or ratio conditions
Choose and display over 30 different engineering units
Self‐teaching memory retains previous values
I/O interface allows for remote data collection, programming, and PLC interface
Multi‐unit interfacing
Technical Data
Ratio: flow A, flow B, or flow A/B