Emo‐3000 – AW Gear Meters EMO-3000 User Manual
Page 13
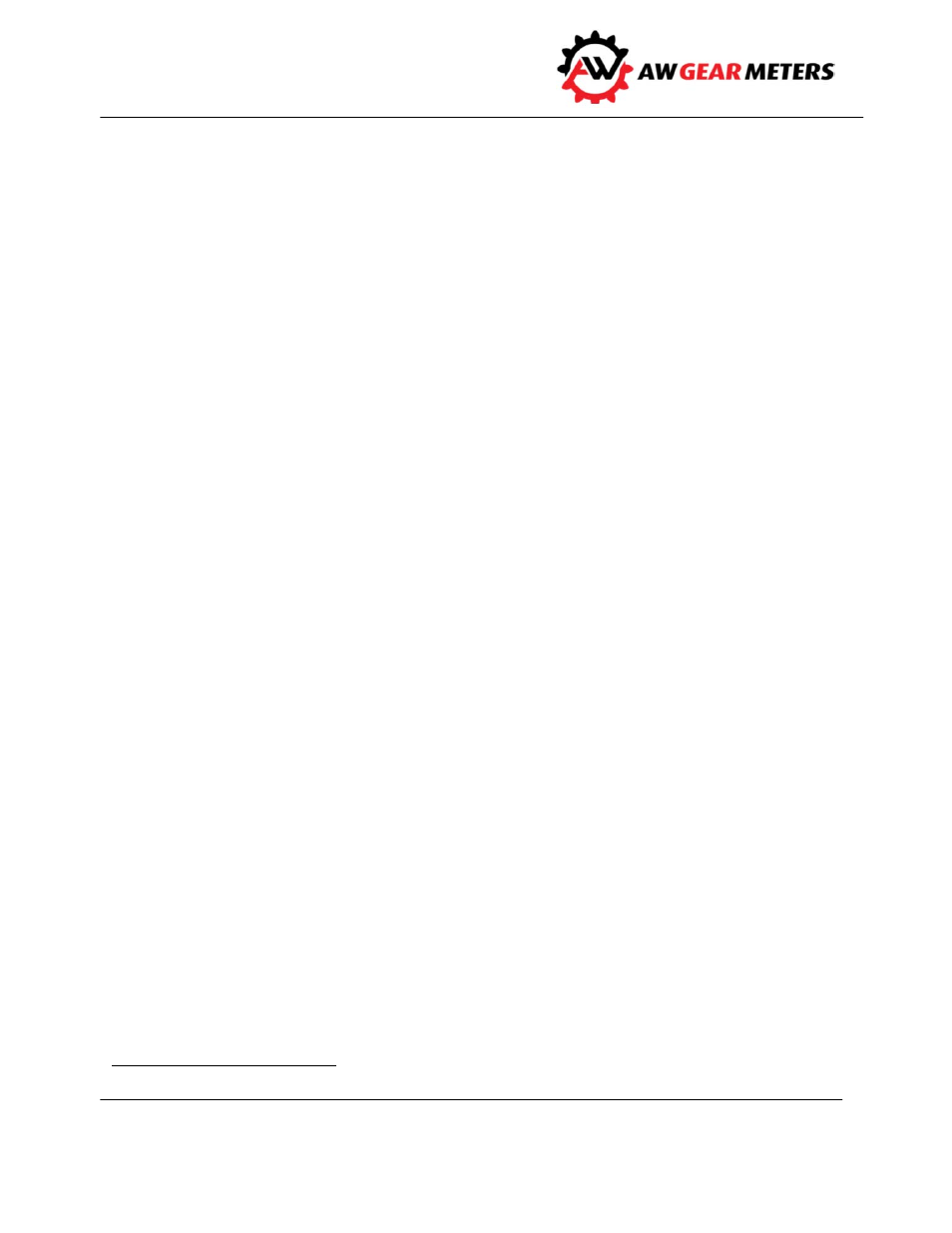
EMO‐3000
Operation and Programming Manual
12
Integral
This variable is used in slow reacting, closed loop systems where a high proportional
factor causes the unit to go in to oscillation. In most cases, it is best to make a design change to improve
the system and hysteresis
†
before employing this variable.
Derivative
The derivative part of the PID formula works against the proportional part if the general
direction is towards the selected set‐value. Often used to stabilize the instability of high gain factors.
Like the proportional factor, experiment to adjust.
Tolerance
The margin for “Set Point Reached.” This variable determines when the PID pursuit of
reaching the set‐value is stopped. For example, if the tolerance is 3 cc/min and the set value is 200 cc/m,
then no PID correction is made between 197 and 203 cc/m. Depending on the mechanics of the system,
start with a large window. Then, after you finish tuning the system, you can reduce this number.
PID Delta Step Delta step determines when a new variable is being accepted into the scratch pad table.
In general, when the range the closed loop covers is very wide, the delta step ought to be relatively
large. With the delta step, it is possible to manipulate the adaption speed. Program this variable
between 0 and 600Hz.
Initial Kick
The initial kick is beneficial in cases where the regulator has a large hysteresis. The kick
value is applied to the analog output if there is a set‐value present, no fluid flow, and the analog out is
less than the kick value. Program in a range of 0000 to 4096 steps, where 0000 = 0mA and 4095 = 20
mA.
PID delay
The time delay in which PID control is activated. The delay initiation starts from the
selection of a new set point input or table pick. PID delay is adjustable from 10 milliseconds to 600
seconds. In some cases, the delay is the best way to make the PID wait for steady state flow.
†
Lag in response