1 storage, 2 safety, 3 maintenance – GE Industrial Solutions EntelliGuard 800–2000 A Frames, 240–600 Vac Maintenance Manual User Manual
Page 15
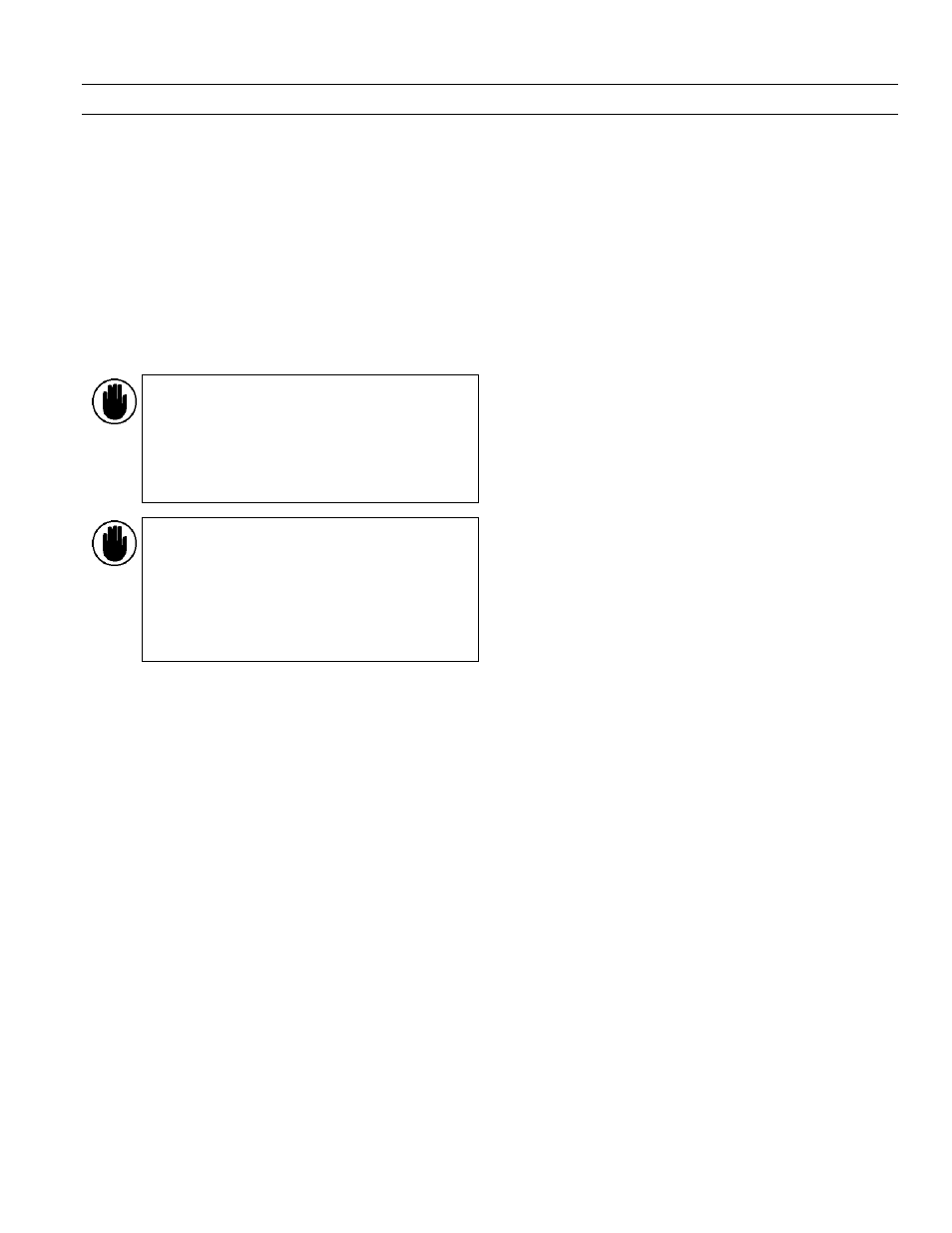
EntelliGuard™ 800–2000 A Power Circuit Breakers
Chapter 3. Storage, Safety, and Maintenance
5
3.1 Storage
The breaker should be put into service immediately in its
permanent location. If this is not possible, the following
precautions must be taken to ensure proper storage of the
breaker
• Protect the breaker against condensation, preferably
by storing it in a warm, dry room, since water absorp-
tion has an adverse effect on the insulating parts.
• Store the breaker in a clean location free from corro-
sive gases or fumes. It is particularly important to
protect the equipment from moisture and cement
dust, as this combination is corrosive to many parts.
CAUTION: If the breaker is stored for any
length of time, inspect it periodically to ensure
that steel parts have not begun to rust and to
ensure good mechanical condition. If the
breaker has been stored under unfavorable
atmospheric conditions, it must be cleaned and
dried before being placed in service.
ATTENTION: Si le disjoncteur est remisé pour
peu importe la période de temps, inspectez-le
périodiquement afin de vous assurer que les
pièces d’acier n’ont pas commencé à rouiller et
de vous assurer de leur bonne condition
mécanique. Si le disjoncteur a été remisé à des
conditions atmosphériques défavorables, il doit
être nettoyé et séché avant d’être mis en service.
3.2 Safety
Each facility must maintain a safety program for the pro-
tection of personnel, as well as other equipment, from the
hazards associated with electrical equipment.
The following requirements are intended to augment a
facility’s safety program, not to supplant local responsibil-
ity for devising a complete safety program. The following
basic industry-accepted safety requirements are applicable
to all major electrical equipment, such as switchgear and
switchboards. General Electric neither condones nor
assumes any responsibility for practices that deviate from
these requirements.
1. All conductors must be assumed to be energized
unless their potential has been measured as ground
and suitable grounding conductors have been
applied to prevent energizing. Many accidents have
been caused by back feeds from various sources.
2. Although interlocks are provided to reduce some of
the risks, each individual’s actions are essential to
prevent accidents when performing service or main-
tenance. Each person’s knowledge, mental aware-
ness, and planned and executed actions often
determine if an accident will occur. The most
important principle for avoiding accidents is that all
associated personnel carefully apply a thorough
understanding of the specific equipment with
regard to its purpose, its construction, its operation,
and situations that could be dangerous.
3. All personnel associated with installation, operation,
and maintenance of electrical equipment, such as
power circuit breakers and other power-handling
equipment, must be thoroughly instructed, with
periodic retraining, about power equipment in gen-
eral and the specific equipment with which they will
be working in particular. Instruction books, actual
devices, and appropriate safety and maintenance
procedures, such as OSHA publications, the
National Electrical Safety Code (ANSI C2), the
National Electrical Code, and NFPA 7 OB Electrical
Equipment Maintenance, must be closely studied
and followed. During actual work, supervisors
should audit procedures to ensure conformance.
4. Excellent maintenance is essential for reliability and
safety of all electrical equipment. Industry publica-
tions of recommended maintenance practices, such
as ANSI/NFPA 70B, Electrical Equipment Maintenance,
are readily available.
3.3 Maintenance
Both long- and short-term maintenance of all electrical
equipment is essential for reliability and safety. Mainte-
nance programs must be well-planned and carried out
consistently with both industry experience and the manu-
facturer’s recommendations. The local environment must
always be considered such programs, including such
variables as ambient temperature, extreme moisture,
number of operations, corrosive atmosphere, significant
insect problems, and any other unusual or abusive condi-
tion of the application.
One of the critical service activities, sometimes neglected,
is the calibration of various control devices. These moni-
tor conditions in the primary and secondary circuits,
sometimes initiating emergency corrective action, such as
opening or closing circuit breakers. In view of the vital
roles of these devices, it is important to follow a periodic
test program.
General Electric recognizes that the interval between peri-
odic checks will vary, depending on the environment, the
type of device, and the customer’s experience. GE recom-
mends that, until the customer has accumulated sufficient
experience to select a test interval best suited to the local
requirements, all significant calibrations be checked at
one- to two-year intervals.
Operation and maintenance guides supplied by manufac-
turers normally address components that require service
or maintenance during the useful life of the equipment.
However, they cannot include every possible part that
could require attention, particularly over a long service
period or under adverse conditions. Maintenance
personnel must be alert to deterioration of any part of the