6 sl cy cles – HEIDENHAIN iTNC 530 (340 49x-02) ISO programming User Manual
Page 386
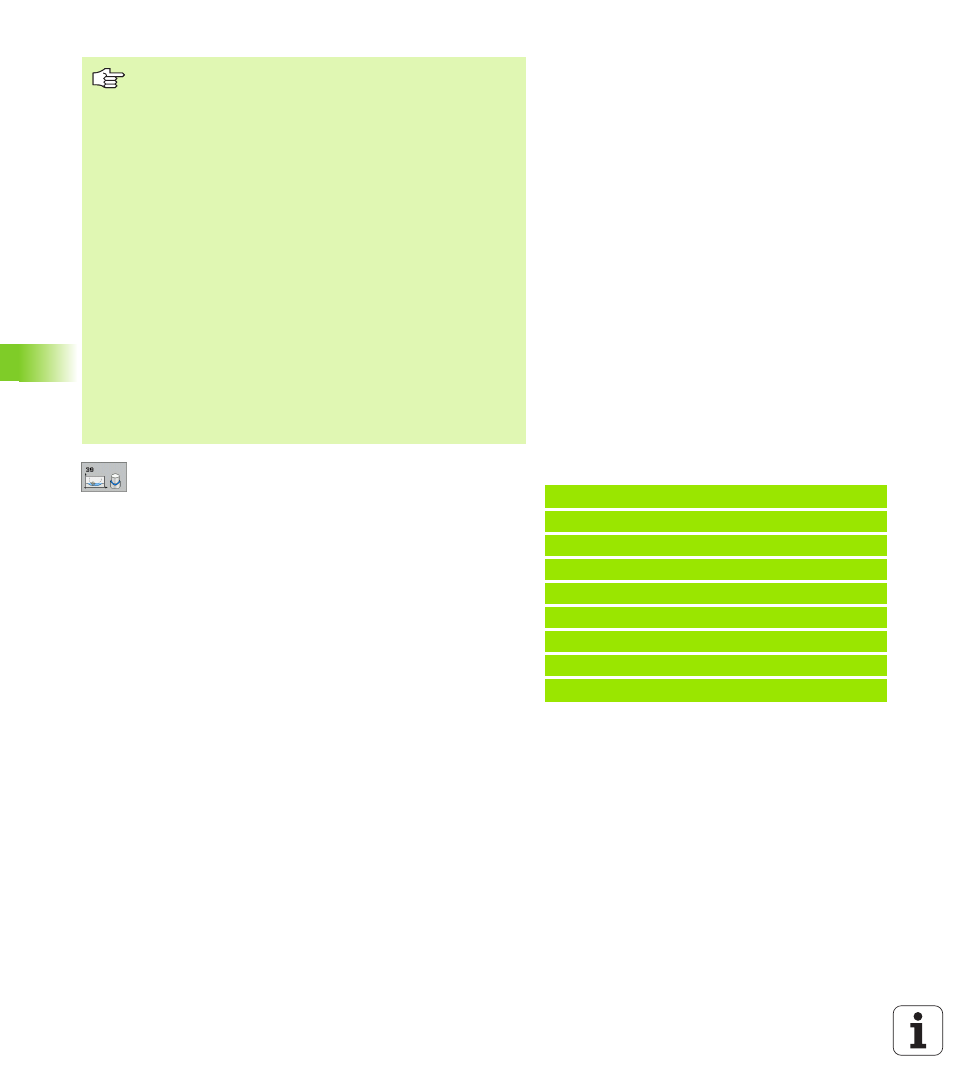
386
8 Programming: Cycles
8.6 SL Cy
cles
8
Milling depth
Q1 (incremental value): Distance
between the cylindrical surface and the floor of the
contour.
8
Finishing allowance for side
Q3 (incremental
value): Finishing allowance on the contour wall.
8
Set-up clearance
Q6 (incremental value): Distance
between the tool tip and the cylinder surface.
8
Plunging depth
Q10 (incremental value): Dimension
by which the tool plunges in each infeed.
8
Feed rate for plunging
Q11: Traversing speed of the
tool in the tool axis.
8
Feed rate for milling
Q12: Traversing speed of the
tool in the working plane.
8
Cylinder radius
Q16: Radius of the cylinder on which
the contour is to be machined.
8
Dimension type ? ang./lin.
Q17: The dimensions for
the rotary axis of the subprogram are given either in
degrees (0) or in mm/inches (1).
Before programming, note the following:
Ensure that the tool has enough space laterally for contour
approach and departure.
The memory capacity for programming an SL cycle is
limited. For example, you can program up to 1024 straight-
line blocks in one SL cycle.
The algebraic sign for the cycle parameter DEPTH
determines the working direction. If you program
DEPTH = 0, the cycle will not be executed.
The cylinder must be set up centered on the rotary table.
The tool axis must be perpendicular to the rotary table. If
this is not the case, the TNC will generate an error
message.
This cycle can also be used in a tilted working plane.
The TNC checks whether the compensated and non-
compensated tool paths lie within the display range of the
rotary axis, which is defined in machine parameter 810.x.
If the error message “Contour programming error” is
output, set MP 810.x = 0.
Example: NC blocks
N50 G139 CYL. SURFACE CONTOUR
Q1=-8
;MILLING DEPTH
Q3=+0
;ALLOWANCE FOR SIDE
Q6=+0
;SET-UP CLEARANCE
Q10=+3
;INFEED DEPTH
Q11=100
;FEED RATE FOR PLUNGING
Q12=350
;FEED RATE FOR MILLING
Q16=25
;RADIUS
Q17=0
;DIMENSION TYPE