Rough-out (cycle g122), 6 sl cy cles – HEIDENHAIN iTNC 530 (340 49x-02) ISO programming User Manual
Page 374
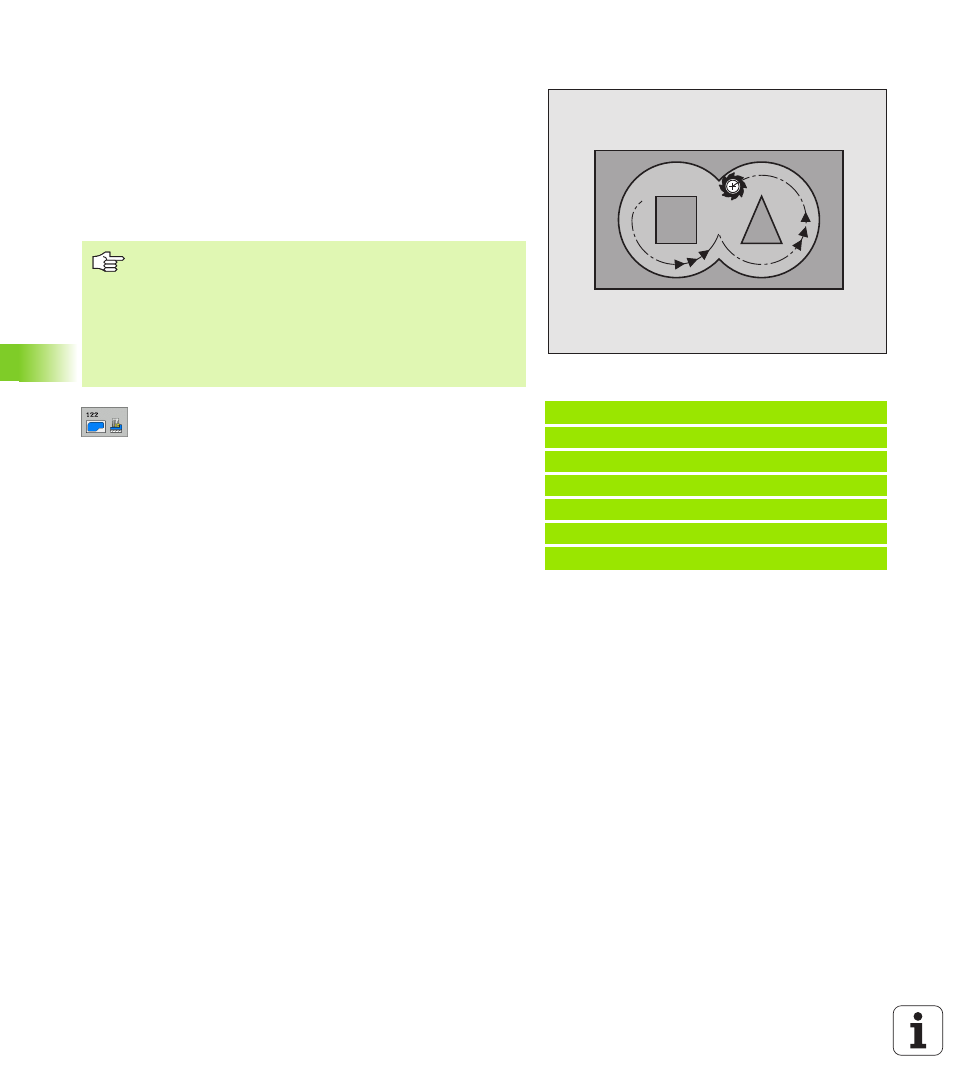
374
8 Programming: Cycles
8.6 SL Cy
cles
ROUGH-OUT (Cycle G122)
1
The TNC positions the tool over the cutter infeed point, taking the
allowance for side into account.
2
In the first plunging depth, the tool mills the contour from inside
outward at the milling feed rate.
3
First the island contours (C and D in the figure at right) are rough-
milled until the pocket contour (A, B) is approached.
4
Then the pocket contour is rough-milled and the tool is retracted to
the clearance height.
8
Plunging depth
Q10 (incremental value): Dimension
by which the tool plunges in each infeed.
8
Feed rate for plunging
Q11: Traversing speed of the
tool in mm/min during penetration.
8
Feed rate for milling
Q12: Traversing speed for
milling in mm/min.
8
Coarse roughing tool number
Q18: Number of the
tool with which the TNC has already coarse-roughed
the contour. If there was no coarse roughing, enter
“0”; if you enter a value other than zero, the TNC will
only rough-out the portion that could not be machined
with the coarse roughing tool.
If the portion that is to be roughed cannot be
approached from the side, the TNC will mill in a
reciprocating plunge-cut; For this purpose you must
enter the tool length LCUTS in the tool table TOOL.T
(see “Tool Data”, page 165) and define the maximum
plunging ANGLE of the tool. The TNC will otherwise
generate an error message.
8
Reciprocation feed rate
Q19: Traversing speed of
the tool in mm/min during reciprocating plunge-cut.
8
Retraction feed rate
Q208: Traversing speed of the
tool in mm/min when retracting after machining. If
you enter Q208 = 0, the TNC retracts the tool at the
feed rate in Q12.
Example: NC block
N59 G122 ROUGH-OUT
Q10=+5
;INFEED DEPTH
Q11=100
;FEED RATE FOR PLUNGING
Q12=350
;FEED RATE FOR ROUGHING
Q18=1
;COARSE ROUGHING TOOL
Q19=150
;RECIPROCATION FEED RATE
Q208=99999 ;RETRACTION FEED RATE
C
D
A
B
Before programming, note the following:
This cycle requires a center-cut end mill (ISO 1641) or pilot
drilling with Cycle G121.
If you define a plunge angle in the ANGLE column of the
tool table for the roughing tool, the TNC moves on a helical
path to the respective roughing depth (see “Tool table:
Standard tool data” on page 167).