Watson-Marlow MM440 User Manual
Page 244
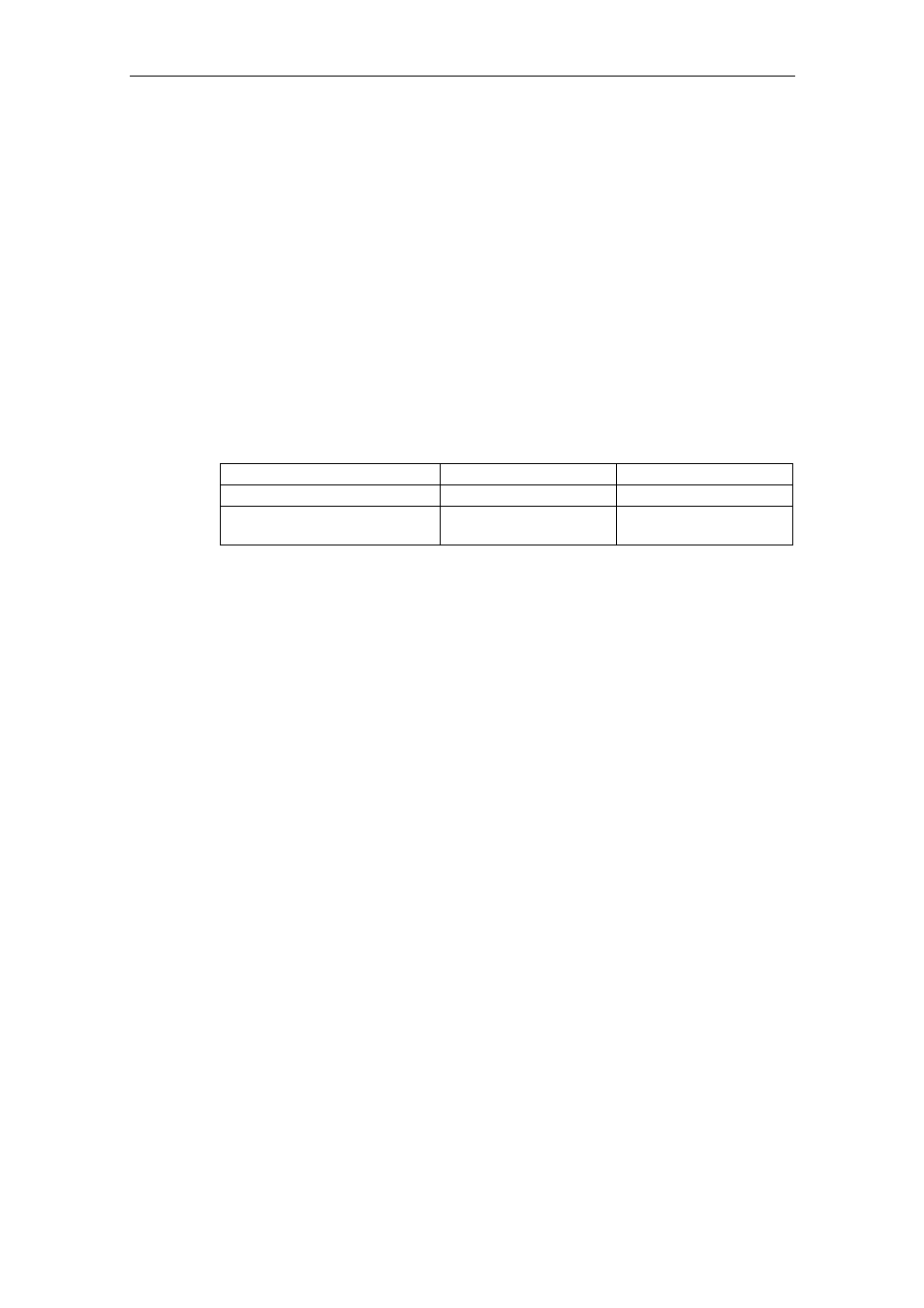
3 Functions
Issue 10/06
MICROMASTER 440 Operating Instructions
244
6SE6400-5AW00-0BP0
The following criteria provide a basis as to when a speed actual value encoder is
required:
¾
High speed accuracy is required
¾
High requirements are placed on the dynamic response
♦ Improved control performance
♦ Improved immunity to disturbances
¾
The torque is to be controlled over a control range greater than 1:10
¾
A defined and/or a changing torque has to be maintained for speeds below
approx. 10 % of the rated motor frequency P0310
When it comes to entering a setpoint, the Vector control (refer to Table 3-40) is
sub-divided into
¾
Closed-loop speed control, and
¾
Closed-loop torque/current control (briefly: Closed-loop torque control).
Table 3-40
Vector control versions
Vector control (closed-loop)
Without encoder
With encoder
Closed-loop speed control
P1300 = 20, P1501 = 0
P1300 = 21, P1501 = 0
Closed-loop torque control
P1300 = 20, P1501 = 1
P1300 = 22
P1300 = 21, P1501 = 1
P1300 = 23
When closed-loop speed control is used, the closed-loop torque control is
secondary. This type of cascaded closed-loop control has proven itself in practice
regarding commissioning and increased transparency.