Delta RMC101 User Manual
Page 57
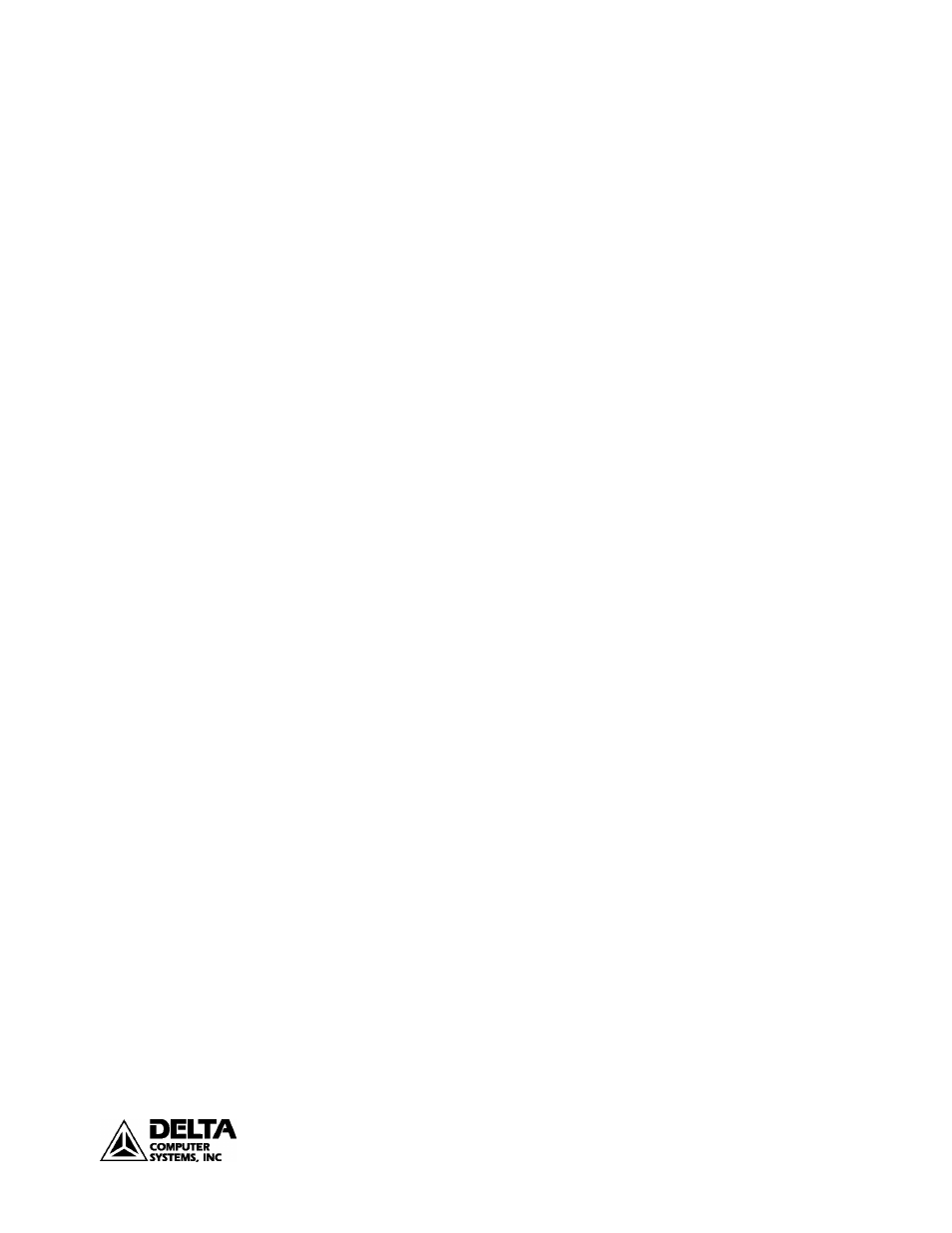
RMC100 Startup
Appendix B: Tuning
57
deltamotion.com
• Selecting Calculate Ramp Time in the Mode word allows the RMC to
automatically calculates the Ramp Time. This is useful if it is difficult to
determine a Ramp Time.
• The following three steps also address parameters affecting the transition.
9. Adjust the Feed Forwards
The Extend and Retract Feed Forwards provide extra drive when extending or
retracting.
• Adjust the Feed Forwards to help the actual pressure track the target
pressure when it is changing.
• If the actual pressure leads the target pressure, decrease the Feed Forwards.
• The Feed Forwards may need to change for different rates of pressure
change. See Feed Forwards for more information.
10. Integrator Preload
Upon transition from position control to pressure control, the drive normally
goes immediately toward zero. In some cases, this is undesirable. The
integrator preload can be set to some value (positive or negative) to provide
some drive immediately upon the transition. If your system overshoots or
undershoots when entering pressure control, you may want to adjust this value.
See Integrator Preload for more information.
Using the Integrator Preload is useful for systems with predictable position-to-
pressure transitions. It always provides the same amount of drive.
11. Drive Transfer Percent
The Drive Transfer Percent acts similarly to the Integrator Preload. The
difference is that the Integrator Preload places a constant value into the integral
drive term, while the Drive Transfer Percent places a certain percentage
(positive or negative) of the current drive into the integral drive term. If your
system overshoots or undershoots when entering pressure control, you may
want to adjust this value. See Drive Transfer Percent for more information.
Using the Drive Transfer Percent is useful for systems with unpredictable
position-to-pressure transitions, such as entering with different speeds.
Because it is a percentage, the transferred drive will vary with the drive
required immediately prior.
12. Fine-tune the System
The final tuning of the system should be made at the speed of intended
operation.
Look for following errors, overshoot, or oscillations.
• Should the system seem a little sloppy, try adjusting the Proportional Gain.
• If the actual position lags or leads the target position during the entire
constant velocity section of the move, adjust the Feed Forwards.
• If an overdrive error occurs, there is not enough drive capacity to drive the
axis at the requested rate of pressure change. Should this occur, increase
the Ramp Time or decrease the speed of the system.
• If the Drive is not high, the gains can probably be increased for better
control, depending on system stability.