Position/pressure tuning procedure – Delta RMC101 User Manual
Page 55
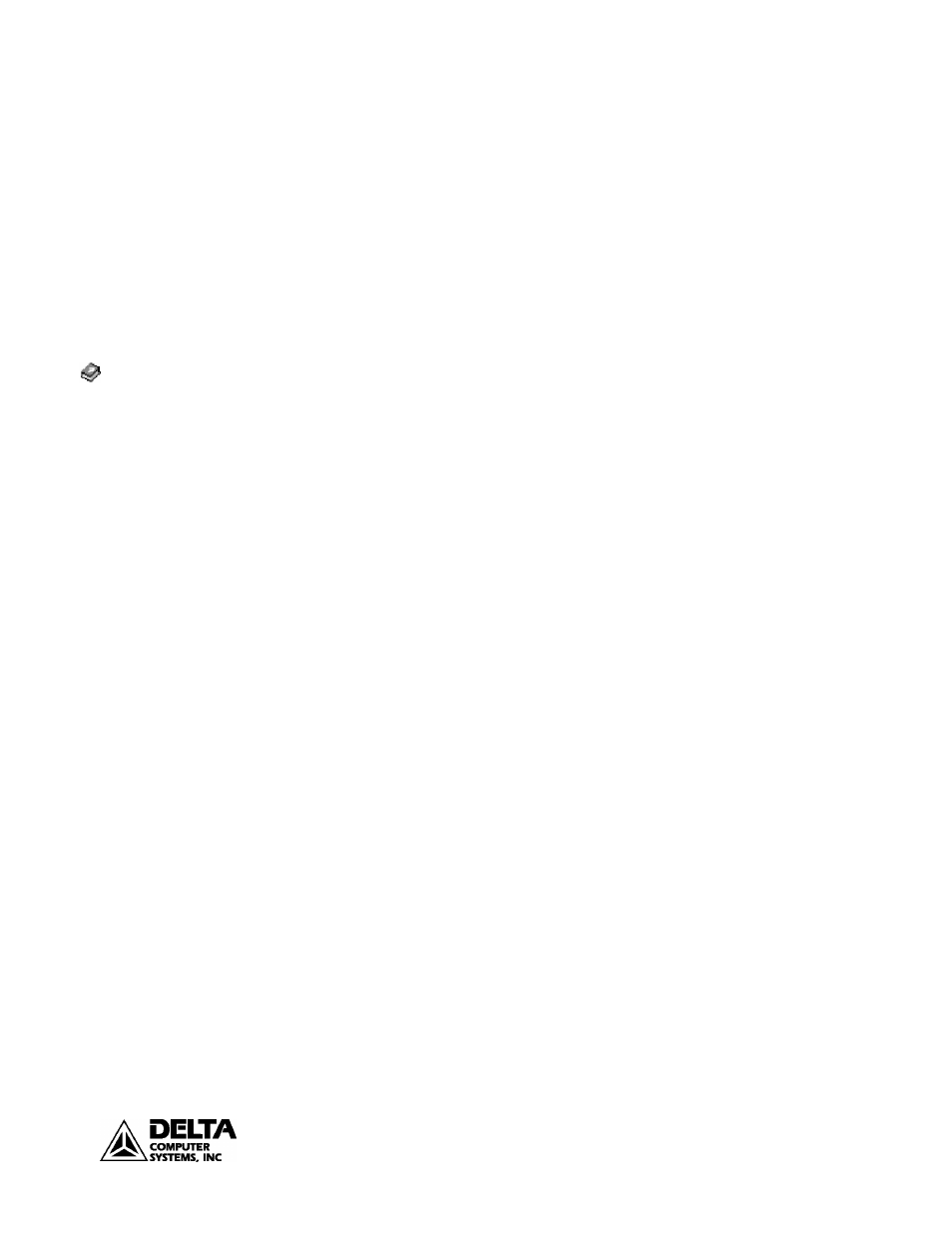
RMC100 Startup
Appendix B: Tuning
55
deltamotion.com
and Set Parameters (P) commands will not be sent to the pressure axis
because they are also valid on the position axis.
• When editing the event table you will have to keep in mind that for
pressure commands, you should enter values for Pressure Set A in the
Acceleration field, values for Pressure Set B in the Deceleration field, and
values for Ramp Time in the Speed field.
Once you have set up your Event Steps table, continue to Tuning a
Position/Pressure System.
Position/Pressure Tuning Procedure
The following procedure may be used to tune a system that transitions from position
control to pressure control.
There is no substitute for experience when tuning an axis. This procedure offers
some guidelines, tips, and suggestions for tuning your system. While these steps
will work for some systems, they may not be the best for a particular system.
1. Tune the Position Gains
The position gains should be tuned before attempting to tune the axis for
pressure. Obtaining control of the axis' position greatly simplifies the tuning of
the pressure gains. If you have not yet tuned the position gains, follow the
procedure outlined in Tuning a Position Axis before continuing.
2. Set Null Drive.
When the axis is holding position (stopped) in closed loop, issue a Set Null
Drive to Integral Drive (n) command. For best accuracy, this should be done
after the axis has been in position for a while, such as 1 second.
The null drive is the drive required to hold the axis in position. In some
systems, such as hydraulics with servo valves, this value may change with
time. Therefore, this step should be performed periodically.
For the remainder of the tuning procedure, use an Event Step sequence as
described in the Position/Pressure Setup topic and illustrated in the
Position/Pressure Example
3. Adjust the Proportional Gain
The Proportional Gain should be adjusted first to gain some control over the
pressure before continuing the tuning procedure.
Note: If negative drive causes an increase in pressure, use negative values
throughout the tuning procedure.
• Set the Proportional Gain to a small value, such as 2.
• Use an Event Step table that makes a position move with the Monitor
Pressure bit set so the axis will transition to pressure control when the
Pressure Set A threshold is crossed. Use a fairly long ramp time initially,
such as 1000 msec.
• Once the axis is in pressure control, ramp the pressure between two
pressures (this is best done in Event Steps). Gradually increase the
proportional gain to minimize the following error. When you see a
tendency to oscillate as the axis moves or stops, decrease the gain 10 to 30
percent.
Index/position-pressure
transition/tuning a position-
pressure system