2 gas piping and pressures, 0 mechanical (cont'd), Warning – Reznor SC Duct Furnace Unit Installation Manual User Manual
Page 8: Gas connection sizing gas supply lines, Pressure testing supply piping
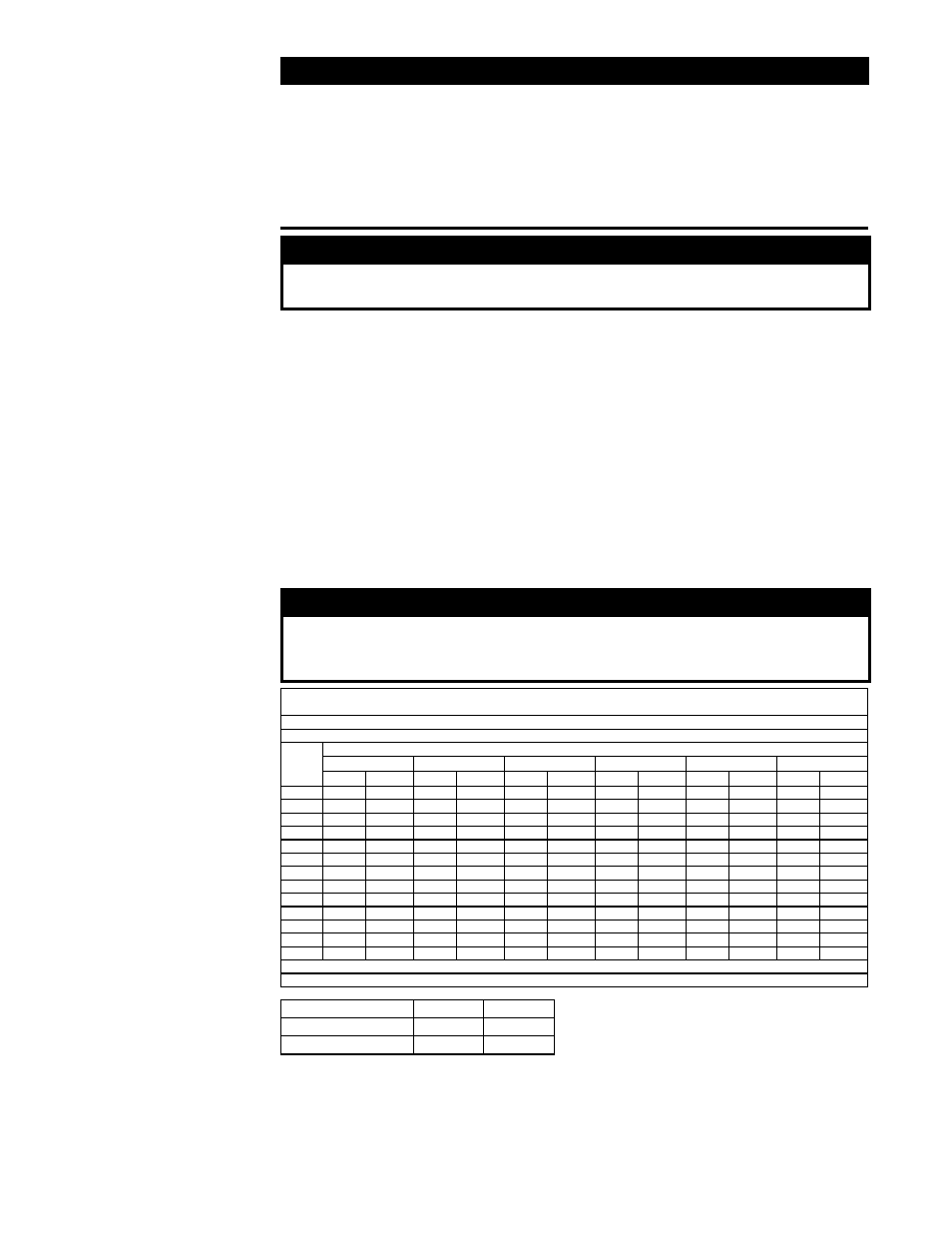
Form I-SC, P/N 207696 R11, Page 8
6.2 Gas Piping and
Pressures
Gas Connection
Sizing Gas Supply
Lines
WARNING
This appliance is equipped for a maximum gas supply pressure of 1/2 psi, 3.5 kPa,
or 14 inches water column. NOTE: Supply pressures higher than 1/2 psi require
installation of an additional service regulator external to the unit.
Pressure Testing Supply Piping
Test Pressure Above 1/2 PSI: Disconnect the heater and manual valve from the gas
supply which is to be pressure tested. Cap or plug the supply line.
Test Pressure Below 1/2 PSI: Before testing, close the manual valve on the heater.
WARNING
Manifold gas pressure must never exceed 3.5" w.c. for natural gas or
10" w.c. for propane gas.
All piping must be in accordance with requirements outlined in the National Fuel
Gas Code ANSI/Z223.1 (latest edition) or CSA B149.1 and B149.2 (See Paragraph
1.4.) Gas supply piping installation should conform with good practice and with local
codes.
These separated-combustion units for natural gas are orificed for gas having a heating
value of 1000 (±50) BTU per cubic ft. If the gas at the installation does not meet this
specification, consult the factory for proper orificing.
Seal the opening for the gas supply pipe with the grommet provided.
Pipe joint compounds (pipe dope) shall be resistant to the action of liquefied petroleum
gas or any other chemical constituents of the gas being supplied.
Install a ground joint union and manual shutoff valve upstream of the unit control sys-
tem. The 1/8" plugged tapping in the shutoff valve provides connection for supply line
pressure test gauge. The National Fuel Gas Code requires the installation of a trap
with a minimum 3" drip leg. Local codes may require a longer drip leg, typically 6".
WARNING
All components of a gas supply system must be leak tested prior to
placing the equipment in service. NEVER TEST FOR LEAKS WITH AN
OPEN FLAME. See Hazard Levels, page 2.
Model SC Sizes 100-250 300-400
Natural Gas
1/2"
3/4"
Propane
1/2"
1/2"
NOTE: The above are gas connection
sizes; not supply line sizes.
After all connections are made, discon-
nect the pilot supply at the control valve
and bleed the system of all air. Reconnect
the pilot line and leak test all connections
by brushing on a soap solution.
Capacity of Piping
Cubic Feet per Hour based on 0.3" w.c. Pressure Drop
Specific Gravity for Natural Gas -- 0.6 (Natural Gas -- 1000 BTU/Cubic Ft)
Specific Gravity for Propane Gas -- 1.6 (Propane Gas -- 2550 BTU/Cubic Ft)
Length
of Pipe
Diameter of Pipe
1/2"
3/4"
1"
1-1/4"
1-1/2"
2"
Natural Propane Natural Propane Natural Propane Natural Propane Natural Propane Natural Propane
20'
92
56
190
116
350
214
730
445
1100
671
2100
1281
30'
73
45
152
93
285
174
590
360
890
543
1650
1007
40'
63
38
130
79
245
149
500
305
760
464
1450
885
50'
56
34
115
70
215
131
440
268
670
409
1270
775
60'
50
31
105
64
195
119
400
244
610
372
1105
674
70'
46
28
96
59
180
110
370
226
560
342
1050
641
80'
43
26
90
55
170
104
350
214
530
323
990
604
90'
40
24
84
51
160
98
320
195
490
299
930
567
100'
38
23
79
48
150
92
305
186
460
281
870
531
125'
34
21
72
44
130
79
275
168
410
250
780
476
150'
31
19
64
39
120
73
250
153
380
232
710
433
175'
28
17
59
36
110
67
225
137
350
214
650
397
200'
26
16
55
34
100
61
210
128
320
195
610
372
Note: When sizing supply lines, consider possibilities of future expansion and increased requirements.
Refer to National Fuel Gas Code for additional information on line sizing.
Manifold or Orifice
(Valve Outlet) Pressure
Settings
Measuring manifold gas pressure cannot be done until the heater is in operation. It
is included in the steps of the "Check-Test-Start" procedure in Paragraph 9.0. The
following warnings and instructions apply.
6.0 Mechanical
(cont'd)