Figure 2.9, Input/output (i/o) box location, 7 0 – 10v out – AERCO KC Series Equipped with C-More Controller for Massachusetts Only User Manual
Page 17: Installation
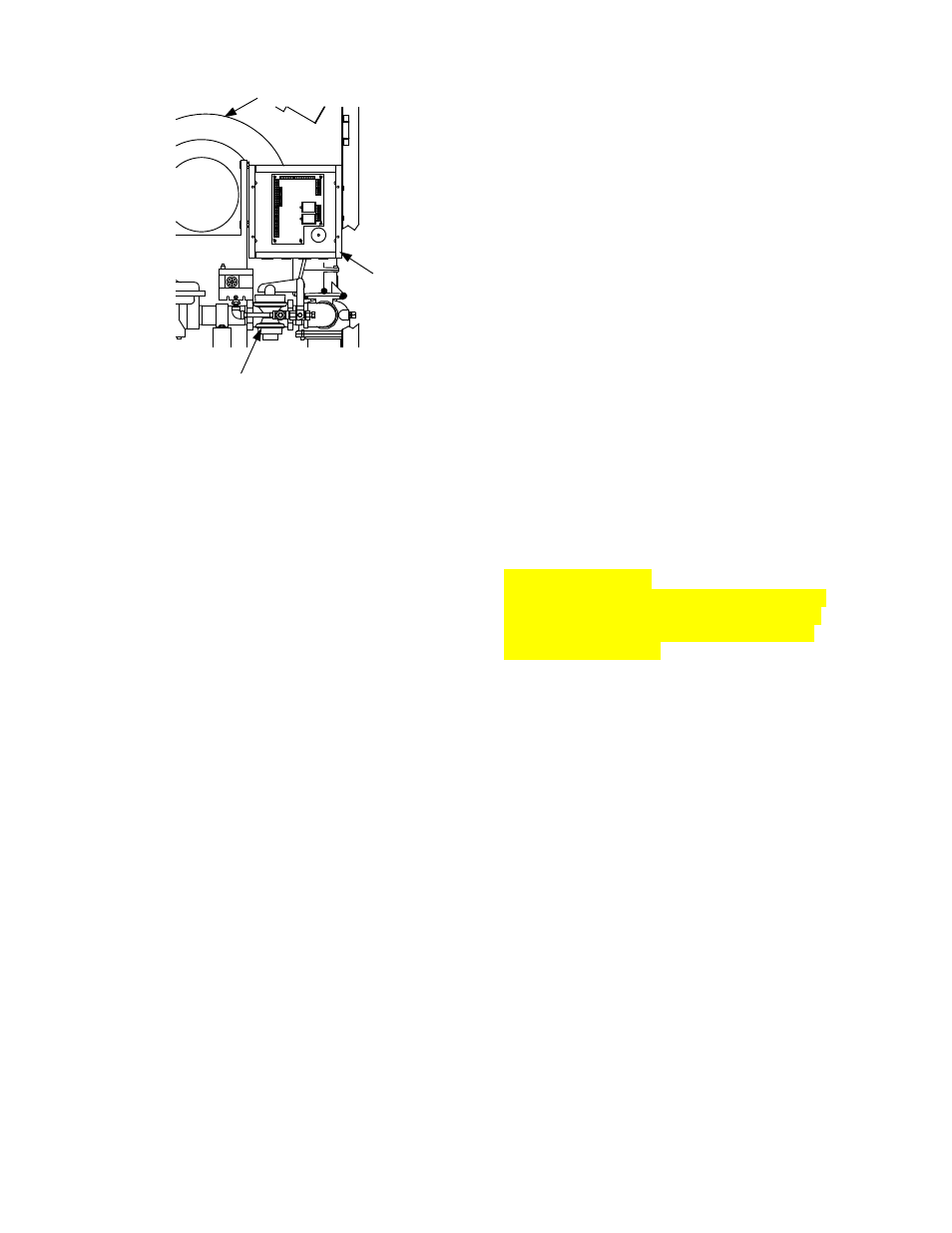
INSTALLATION
2-7
GAS SHUT-OFF
VALVE
I/O BOX
BLOWER
Figure 2.9
Input/Output (I/O) Box Location
2.6.1 OUTDOOR AIR SENSOR IN
Not applicable to Water Heaters.
2.6.2 AUX SENSOR IN
The AUX SENSOR IN terminals can be used to
add an additional temperature sensor for
monitoring purposes. This input is always
enabled and is a view only input that can be
seen in the operating menu. The sensor must be
wired to the AUX SENSOR IN and SENSOR
COMMON and must be similar to AERCO
BALCO wire sensor P/N 12449. A resistance
chart for this sensor can be found in Appendix C.
2.6.3 ANALOG IN
The ANALOG IN + and – terminals are used
when an external signal is used to change the
setpoint of the water heater when operating in
the Remote Setpoint Mode.
Either a 4 to 20 mA / 1 to 5 VDC or a 0 to 20 mA/
0 to 5 VDC signal may be used to vary the
setpoint or valve position. The factory default
setting is for 4 to 20 mA / 1 to 5 VDC, however
this may be changed to 0 to 20 mA / 0 to 5 VDC
using the Configuration Menu described in
Section 3. If voltage rather than current is
selected as the drive signal, a DIP switch must
be set on the CPU Board located inside the
Control Box. Contact the AERCO factory for
information on setting DIP switches.
All supplied signals must be floating
(ungrounded) signals. Connections between the
source and the Heater’s I/O Box must be made
using twisted shielded pair wire of 18 –22
AWG,,such as Belden 9841(see Fig. 2.10).
Polarity must be maintained and the shield must
be connected only at the source end. It must be
left floating (not connected) at the Heater’s I/O
Box.
Whether using voltage or current for the drive
signal, they are linearly mapped to a 40°F to
240°F setpoint or a 0% to 100% valve position.
No scaling for these signals is provided
2.6.4 B.M.S. (PWM) IN
Not applicable to Water Heaters.
2.6.5 SHIELD
The SHIELD terminals are used to terminate any
shields used on sensor wires connected to the
unit. Shields must only be connected to these
terminals.
2.6.6 mA OUT
These terminals provide a 4 to 20 mA output that
can be used to monitor setpoint ( to 220°F),
outlet temperature (
to 245°F), or valve position
(0% to 100%). This function is enabled in the
Configuration Menu (Section 3, Table 3.4).
2.6.7 0 – 10V OUT
These terminals provide a 0 to 10 volt output to
control the rotational speed of the blower. This
function is enabled in the Configuration Menu
(Chapter 3, Table 3-4).
2.6.8 RS-485 COMM
These terminals are used for RS-485 MODBUS
serial communication between the unit and an
external “Master”, such as an Energy Manage-
ment System.
2.6.9 EXHAUST SWITCH IN
These terminals permit an external exhaust
switch to be connected to the exhaust manifold
of the boiler. The exhaust sensor should be a
normally open type switch (such as AERCO P/N
123463) that closes (trips) at 500°F.
2.6.10 INTERLOCKS
The unit offers two interlock circuits for
interfacing with Energy Management Systems
and auxiliary equipment such as pumps or
louvers or other accessories. These interlocks
are called the Remote Interlock and Delayed
Interlock (Fig. 2.10). The wiring terminals for
these interlocks are located inside the I/O Box
on the left side of the unit. The I/O Box cover
contains a wiring diagram which shows the
terminal strip locations for these interlocks
labeled REMOTE INTL’K IN and DELAYED