Basic welding transmig 250i – Tweco 250i Transmig Inverter User Manual
Page 61
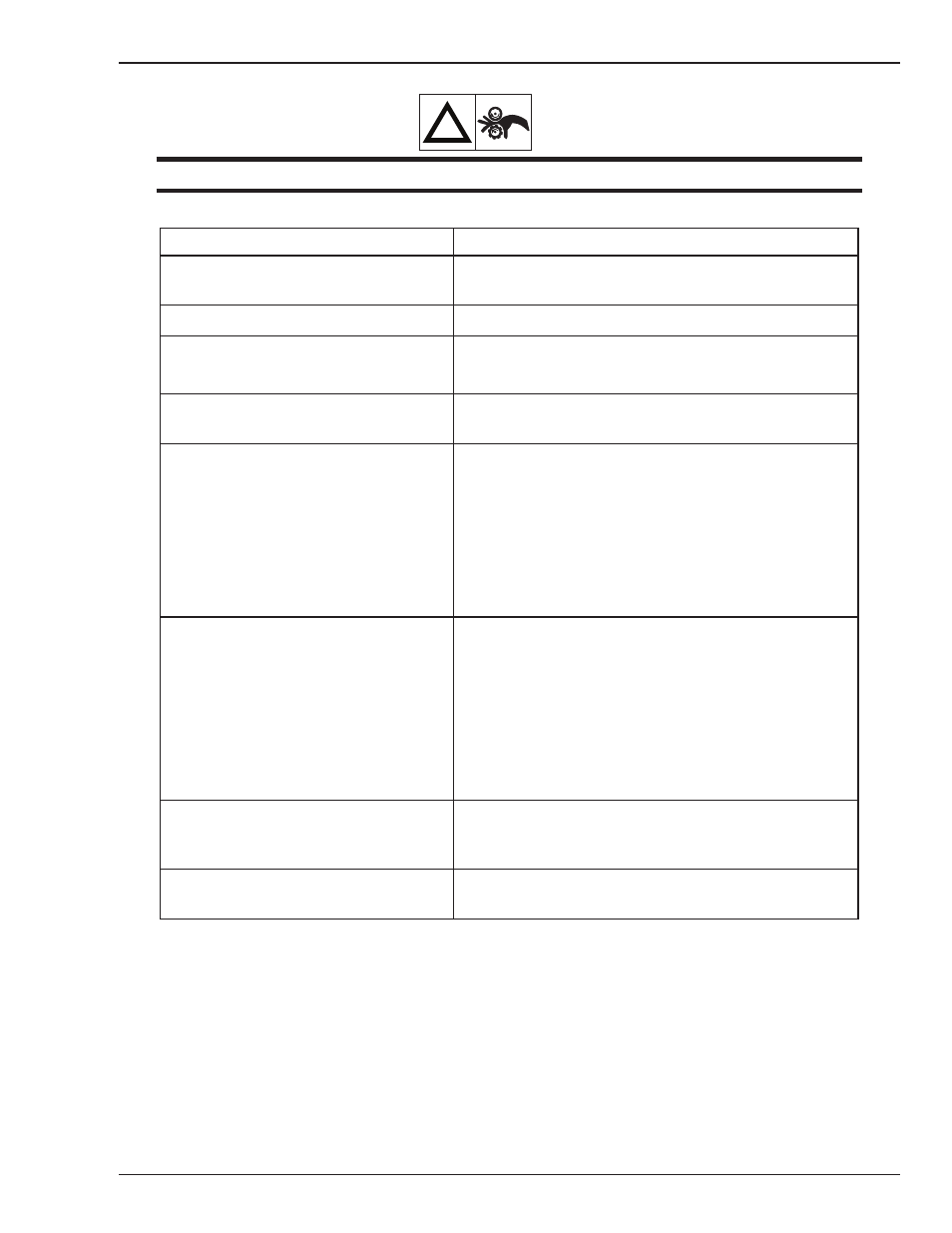
BASIC WELDING
TRANSMIG 250I
Manual 0-5187
4-5
BASIC WELDING
Problem 2 - Inconsistent Wire Feed
!
WARNING
Disengage the feed roll when testing for gas flow by ear.
Wire feeding problems can be reduced by checking the following points.
FAULT
CAUSE
1 Feed roller driven by motor in the
cabinet slipped.
Wire spool brake is too tight.
2 Wire spool unwound and tangled.
Wire spool brake is too loose.
3 Worn or incorrect feed roller size
A Use a feed roller matched to the size you are welding.
B Replace feed roller if worn.
4 Wire rubbed against the misaligned
guides and reduced wire feed ability.
Misalignment of inlet/outlet guides
5 Liner blocked with swarf
A Increased amounts of swarf are produced by the wire
passing through the feed roller when excessive pres-
sure is applied to the pressure roller adjuster.
B Swarf can also be produced by the wire passing
through an incorrect feed roller groove shape or size.
C Swarf is fed into the conduit liner where it accumu-
lates thus reducing wire feed ability.
6 Incorrect or worn contact tip
A The contact tip transfers the weld current to the elec-
trode wire. If the hole in the contact tip is too large
then arcing may occur inside the contact tip resulting
in the wire jamming in the contact tip
B When using soft wire such as aluminium it may
become jammed in the contact tip due to expansion of
the wire when heated. A contact tip designed for soft
wires should be used.
7 Poor work lead contact to work piece
If the work lead has a poor electrical contact to the
work piece then the connection point will heat up and
result in a reduction of power at the arc.
8 Bent liner
This will cause friction between the wire and the liner
thus reducing wire feed ability
Table 4-2: Wire Feeding Problems