Tweco Weld Sequencer User Manual
Page 37
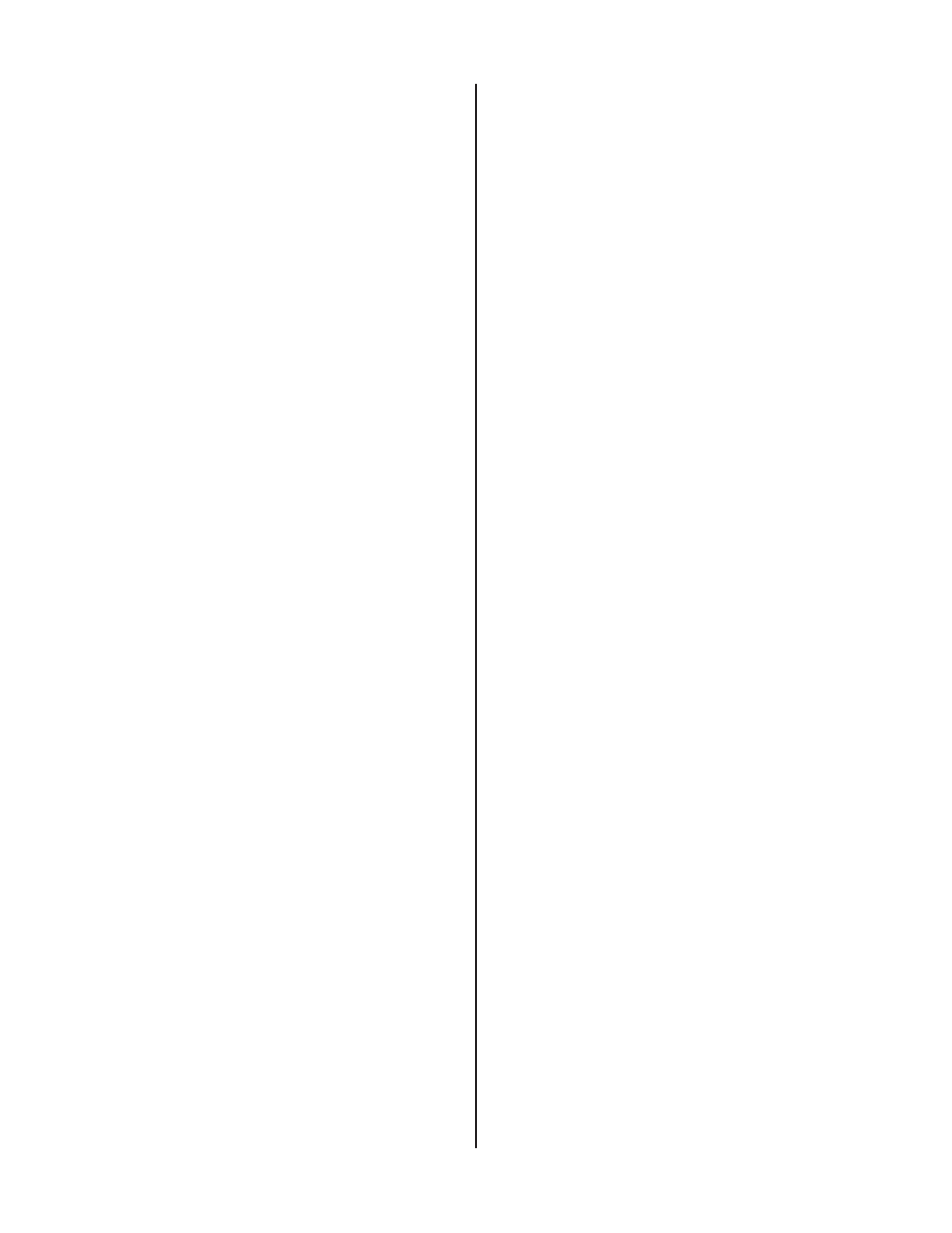
Manual 0-2023
31
Section Name
5. CS1 faulty
a. Disconnect J8, connect to jumper plug, if arc
transfers replace CS1 PC Board. If no transfer,
refer to Section 5.04-C
GS1, CS1 & RP1 used
6. GS1 (if used) in MANUAL position
a. Switch to AUTO
D. Contactor stays on
CS1 and WT1 not used, GS1 and CP1 on or off
1. Console or power supply not switched to remote con-
tactor control
a. Check & correct
2. RP1 contactor switch faulty
a. Replace
WT1 used. Contactor does not shut off at end of tim-
ing period but shuts off with RP1 contactor switch
3. Faulty CC relay
a. Check & replace; Refer to Setion 5.04-B
4. Faulty WT1
a. Check per Section 5.04-A and replace WT1 PC
Board if necessary
CS1 used. Transfer occurs as soon as RP1 contactor
switch turned on, prior to start sequence
5. Faulty CC relay
a. Check replace
6. Faulty CS1
a. Replace CS1 PC board
E. No current control or incorrect current level
CS1 & CP1 not used
1. Power supply on wrong range
a. Set to proper range
2. Power supply or console not set to remote current
a. Set to remote
3. RP1 current control faulty
a. Check & replace (refer to Section 5.04-C)
4. If CS1 or CP1 not installed, J7 or J8 not plugged into
jumper plugs
a. Install jumper(s)
CS1 used, Initial or Final Current incorrect
5. Improper setting or faulty CS1
a. Correct setting or replace CS1 PC Board
CP1 used, Welds at background current only (no
pulse)
6. BACKGROUND CURRENT knob (pull for display) is
pulled out
a. Push knob in
7. Faulty CP1 PC board
a. Replace
CS1 used, Welds at peak only
8. Background current set to same as peak
a. Set properly
9. Stop pulse signal applied at wrong time (J7-13, TB2-3
wire #22 connected to signal common wire #11 TB1-1,
2, 3, 4)
a. Remove stop pulse signal (refer to Appendix)
10. Faulty CP1 PC Board
a. Replace
F. At end of set initial current time current does not
start to increase
1. Initial current set same as weld current
a. Reset
2. CS1 faulty
a. Replace CS1 PC Board
G. Gas does not start to increase at end of set initial
current time
1. GS1 not ON
a. Turn GS1 to ON
2. Gas supply not on
a. Open supply valve
3. MIN gas flow set to close to MAX flow
a. Check MIN flow setting
4. Plasma gas control valve in welding console not opened
all the way
a. Open valve completely
5. Faulty GS1 valve
a. Replace (refer to Section 5.05-F)