Rockwell Automation Liqui-Flo DBT Reach Drive User Manual
Page 235
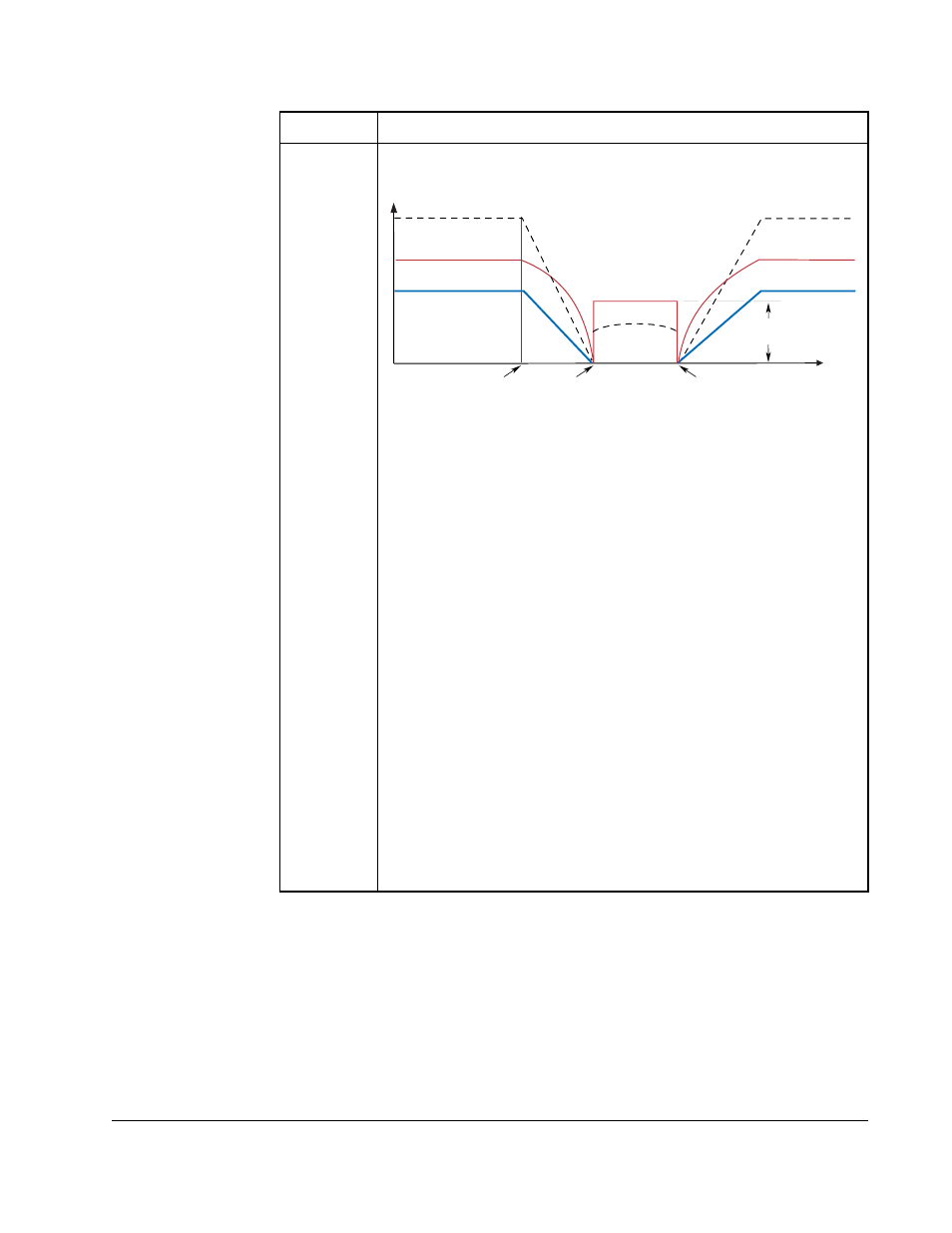
Application Notes
Appendix D-21
Ramp to
Hold
This method combines two of the methods above. It uses drive
output reduction to stop the load and DC injection to hold the load at
zero speed once it has stopped.
1.
On Stop, drive output will decrease according to the
programmed pattern from its present value to zero. The pattern
may be linear or squared. The output will decrease to zero at the
rate determined by the programmed Maximum Freq (55) and the
programmed active Decel Time x.
2.
The reduction in output can be limited by other drive factors such
as bus or current regulation.
3.
When the output reaches zero 3 phase drive output goes to zero
(off) and the drive outputs DC voltage on the last used phase at
the level programmed in DC Brake Level (158). This voltage
causes a “holding” brake torque.
4.
DC voltage to the motor continues until a Start command is
reissued or the drive is disabled.
5.
If a Start command is reissued, DC Braking ceases and he drive
returns to normal AC operation. If an Enable command is
removed, the drive enters a “not ready” state until the enable is
restored.
Mode
Description
DC
Hold Level
Time
Output Voltage
Output Voltage
Output Current
Output Current
Motor Speed
Output Voltage
Output Current
Motor Speed
Re-issuing a
Start Command
Stop
Command
Zero
Command
Speed