6 wiring start / stop control – Rockwell Automation VSM500 Integrated Drive/Motor User Manual
Page 42
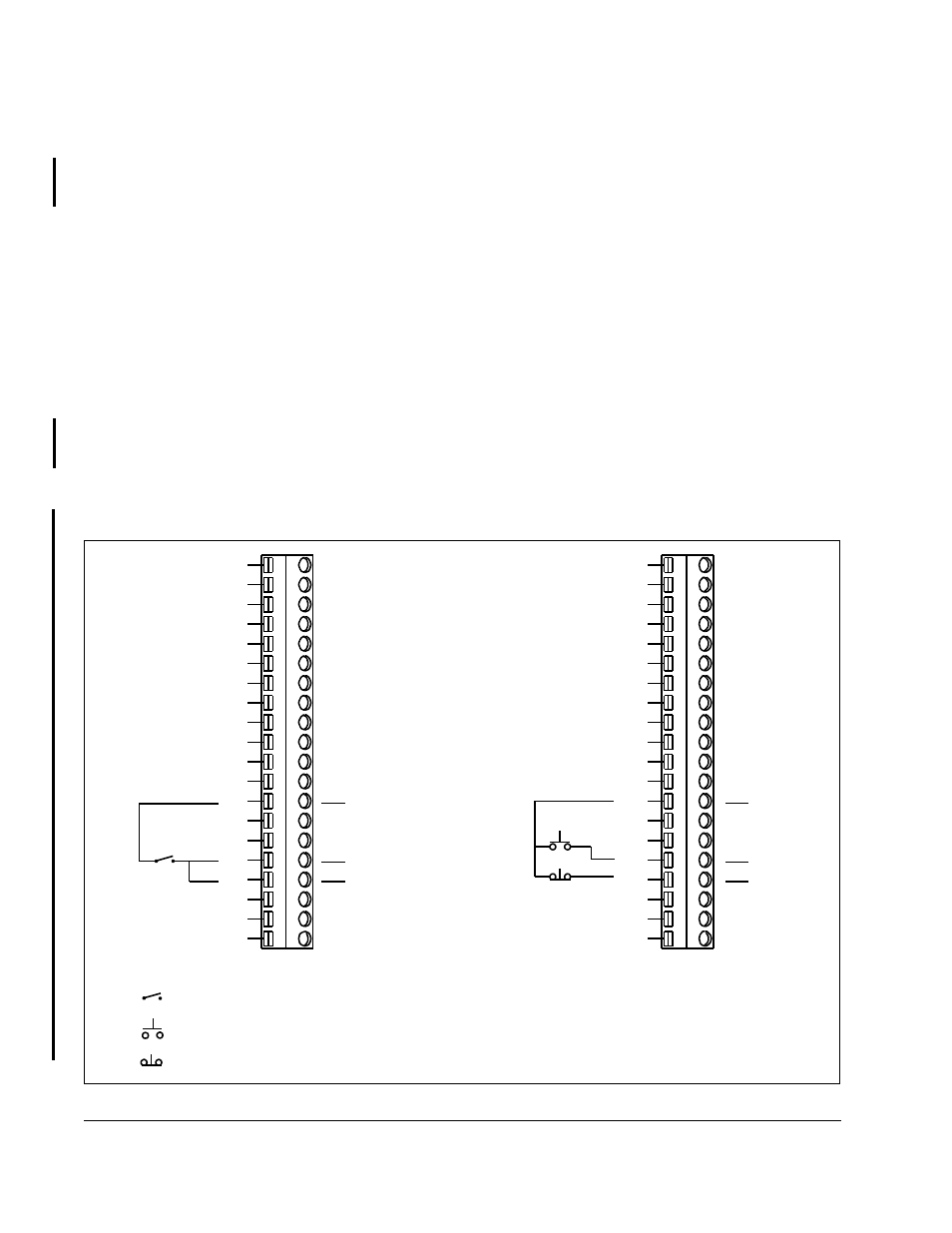
7-12
Installing and Operating the VSM500 Integrated Drive/Motor, Version 3.0
7.6
Wiring Start / Stop Control
Important: This applies only to standard units and local operator control units set up
for terminal block control (setup slide switch position 9 = ON, see section
8.3.9).
The system looks for an open-to-closed transition at the Start input before starting the
unit unless you have the Power-Up Start switch (setup slide switch 1, see section
8.3.1) set to ON. If you use a maintained start device and power to the unit is lost, you
must open and reclose the start device before the unit will start again. Both the Stop
and the Function Loss input signals must be present and there must be no active
faults for the unit to start.
In order for the unit to run, you must maintain a signal at the Stop input. If the signal is
interrupted, the unit coasts to rest (default) or ramps to rest (user option). To restart
the unit, you must restore the signal and reassert the Start input.
The unit ships from the factory with a jumper on the Stop input terminals (terminals 13
and 17) which permits the unit to be started. To stop the unit using the terminal block
inputs, you must remove the factory jumper and install appropriate stop wiring.
Figure 7.12 illustrates wiring for a maintained 2-wire and for a momentary 3-wire
Start / Stop control.
Figure 7.12 – Start / Stop Control Wiring
19
18
17
16
15
14
13
12
11
10
9
8
7
6
5
4
3
2
1
Stop
Start
24V DC
18
19
12
15
17
16
14
13
9
10
11
7
8
6
4
5
3
1
2
N.O
N.C.
Maintained 2-Wire
Momentary 3-Wire
= Maintained Contact - Open
= N.O. Momentary Contact
= N.C. Momentary Contact
24V DC
Start
Stop
20
20
Important: To stop the unit using the
terminal block inputs, the jumper between
terminals 13 and 17 must be removed when
wiring the Stop input.