Hapter, Step 7 - wire the control signal terminal block – Rockwell Automation VSM500 Integrated Drive/Motor User Manual
Page 31
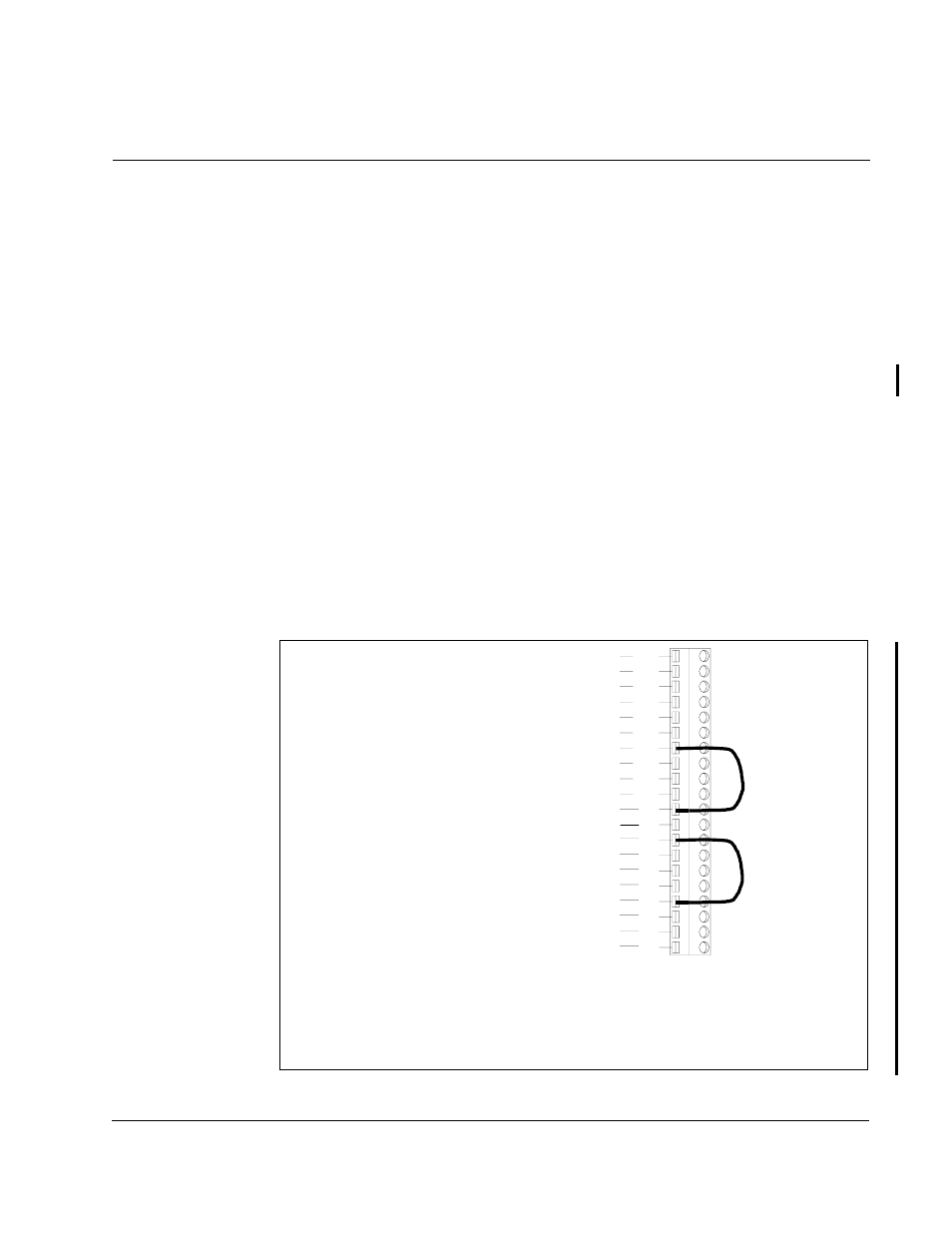
Step 7 - Wire the Control Signal Terminal Block
7-1
C
HAPTER
7
Step 7 - Wire the Control Signal
Terminal Block
The following sections describe how to wire the control signal terminal block shown in
figure 7.1.
Refer to either figure 7.2 (standard units or local operator control units set up for
terminal block control) or figure 7.3 (local operator control units) before you begin
wiring. These figures show typical wiring connections and the sections in this chapter
where the signals are described in detail.
Note the following when wiring the terminal block:
•
The terminal block is isolated from the input power.
•
Route the control wires separately from the power wires.
•
The terminal block accepts 0.326 mm
2
(22 AWG) through 3.31 mm
2
(12 AWG) wire.
•
The maximum lead length is 300 meters (1000 ft
).
•
The maximum tightening torque is 0.8 Nm (7 in-lb).
Figure 7.1 – Control Signal Terminal Block
Control Signal Terminal Block
19
18
17
16
15
14
13
12
11
10
9
8
7
6
5
4
3
2
1
Relay Common
N.O. Relay
24V DC Common
Stop
Start
Reset
Forward/Reverse
24V DC
Function Loss
Speed Preset 0
Speed Preset 1
Speed Preset 2
24V DC
Common
0 to 10V Output
Common
4 to 20mA Speed Reference Input
0 to 10V Speed Reference Input
10 Volt Reference
RPM / %Load Display
20
1>
2>
1> The jumper between terminals 7
and 11 must be removed when
wiring the Function Loss input. See
section 7.1 for more information.
2> Important: To stop the unit using the
terminal block inputs, the jumper
between terminals 13 and 17 must be
removed when wiring the Stop input.
See section 7.6 for more information.