Rockwell Automation SP600 User Manual Version 3.0 User Manual
Page 131
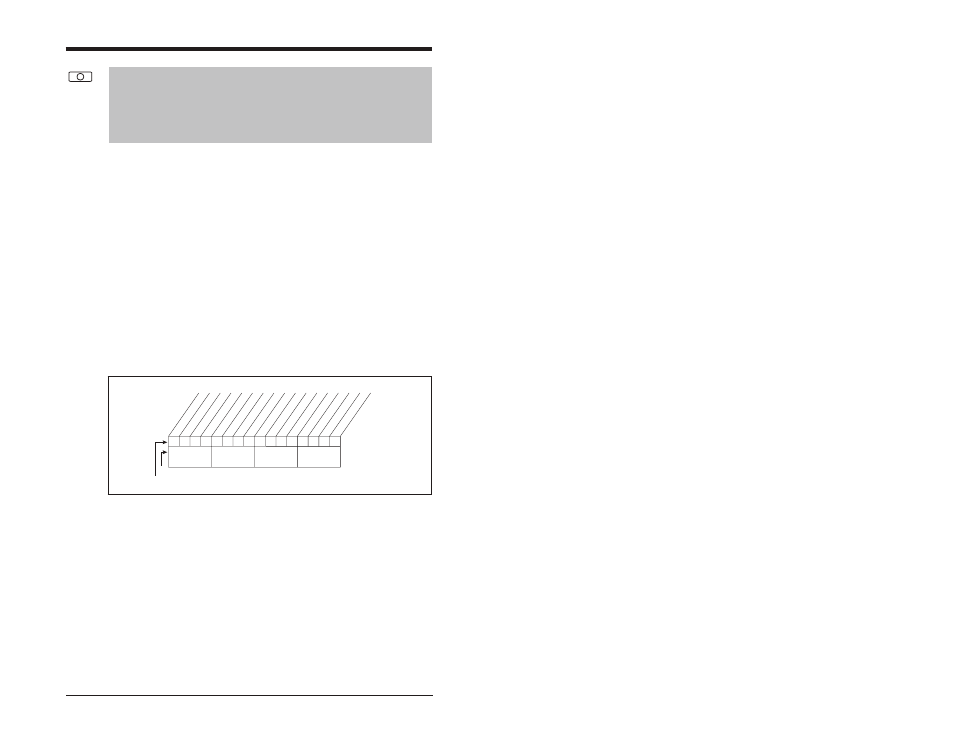
Parameter Descriptions
11-29
.
Selects specific features of the PI regulator (see appendix E.)
Proportional control (P) adjusts the output based on the magnitude
of the error (larger error = proportionally larger correction). If the
error is doubled, then the output of the proportional control is
doubled; and, conversely, if the error is cut in half, then the output of
the proportional output will be cut in half. With proportional control
only, there is always an error, so the feedback and the reference are
never equal.
Integral control (I) adjusts the output based on the duration of the
error. The longer the error is present, the larger the correction
output value will become. The integral control by itself is a ramped
output correction and typically gives a smooth output correction and
will continue to integrate until zero error is achieved. By itself,
integral control is slower than many applications require and
therefore is combined with proportional control (PI). It also
contributes to overshoot of the correction value.
Bit 0 - Excl Mode (Exclusive Mode)
• Enabled = Selects speed regulation (PI output used as
speed command).
• Disabled = Selects trim regulation (PI output summed with
speed command).
Bit 1 - Invert Error
• Enables/disables the option to invert the sign of the PI error
signal. Enabling this feature creates a decrease in output for
an increasing error and an increase in output for a
decreasing error.
Bit 2 - Preload Mode
124
PI Configuration
Range:
See figure 11.10
Default:
See figure 11.10
Access:
2
Path: Speed Command>Process PI
See also:
80, 125-138
Figure 11.10 – PI Configuration (124)
0
0
0
0
0
0
0
0
x
x
x
x
x
x
x
x
10
0
1
2
3
4
5
6
7
8
9
11
12
13
14
15
1 =Enabled
0 =Disabled
x =Reserved
Bit #
Factory Default Bit Values
Excl Mode
In
ve
rt Error
Preload Mode
Ramp Ref
Zero Clamp
Feedbak Sqr
t
Stop Mode
Anti Wind
Up
Nibble 1
Nibble 2
Nibble 3
Nibble 4